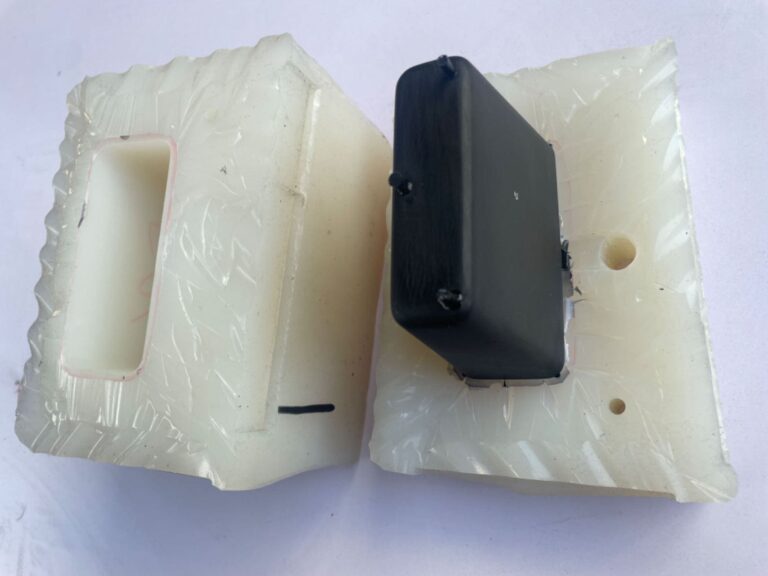
Faster your business to market with Kusla rapid manufacturing services
- Rapid Prototyping & low volume Manufacturing Service
- Machining and Molding For Plastic & Metal Parts
- ISO 9001:2015 Certified Factory
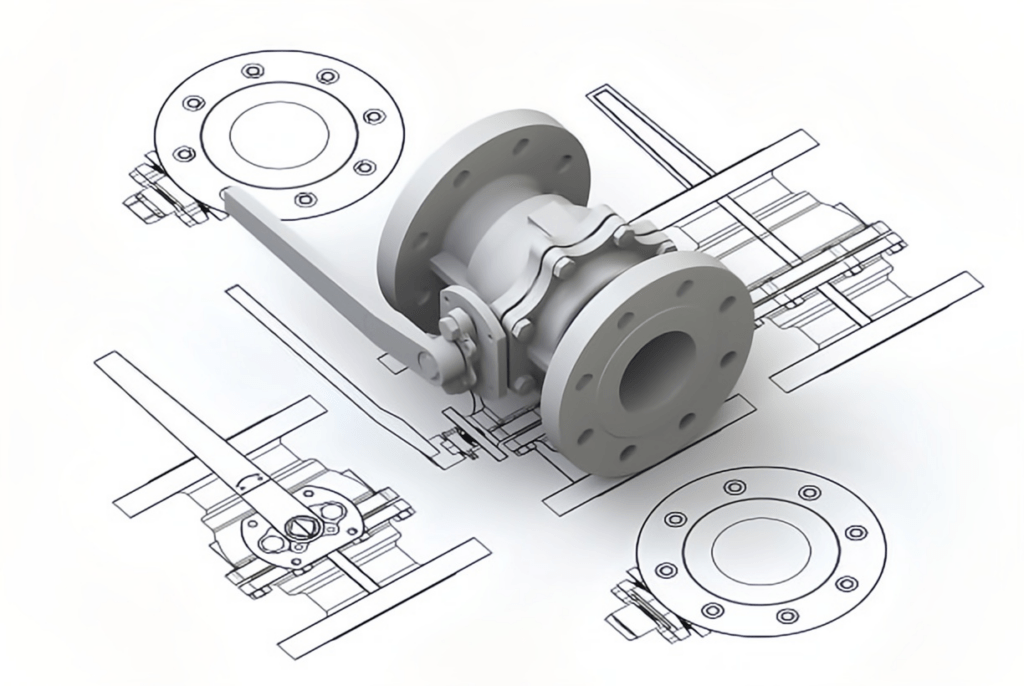
Rapid Prototyping Services & Rapid Manufacturing
Kusla, established in 2013, is a rapid prototyping & rapid Manufacturing company based in Suzhou, China.
We have the most advanced machines and the best engineers to provide you with unparalleled rapid prototyping and manufacturing services.
We can offer you plastic and metal prototyping services and low-volume manufacturing utilizing CNC machining, 3D Printing, Sheet Metal Fabrication, Urethane Casting, Injection Molding, and Diamond turning.
Kusla can be a reliable partner with your R&D team. With our rapid prototyping service, you can get your prototypes in hand with high-quality standards faster than ever. We use the best rapid prototyping technology to meet your design challenges, and work with your team to solve the issues during the function tests. Our rapid prototyping techniques include CNC prototyping, 3D printing, Urethane casting, prototype injection molding, sheet metal prototyping, and surface finishing.
Kusla also offers low-volume manufacturing services with a wide range of solutions to help you scale from rapid prototypes to low-volume production parts. With our rich experiences in parts manufacturing, you will get plastic and metal parts with high-quality standards. Our Custom manufacturing services include CNC machining, plastic injection molding, sheet metal fabrication, and parts finishing. No matter the volume, from low to high, we can manage your projects.
We provide precision CNC machining services, including CNC milling, CNC turning, and 5-axis CNC machining.
We can complete your prototype in as fast as 24 hours with FDM, SLS, SLA, and Metal 3D printing technologies.
Our capability covers sheet metal cutting, bending, welding, and stamping with no minimum order quantity.
We can utilize superior materials to accomplish the Urethane Casting Prototyping, ensuring completion within 5 days for quantities less than 100.
We provide both insert molding and overmolding techniques, with production materials in a short time, less than 4 weeks.
Custom High precision optic components from prototypes to production in a short lead time of less than 2 weeks.
Kusla has a factory spanning over 10,000 square meters, a team of more than 100 employees, and over 200 high-end machines, with the capacity to produce over 100,000 parts per month. We can provide you low-volume manufacturing services based on a range of techniques including
Kusla specializes in automotive prototyping and parts manufacturing with a one-stop service for most automotive components.
Kusla offers a wide range of Medical Device prototyping services and high-quality medical device prototypes in a short lead time.
Kusla has many years of experience in Consumer product prototyping services which could help you get product prototypes quickly.
Trusted by numerous large companies.
We can provide you with better service and lower prices.
We possess 15 years of experience in prototyping and manufacturing. We consistently work alongside our clients to enhance the quality of our products. Numerous large-scale manufacturing companies have expressed their satisfaction with us.
After you send us a request for a quote, we will respond with a price within 24 hours and can have your prototype produced within as little as one working day.
Thanks to our engineers’ efficiency and advanced machinery, our prices are typically 20% lower than our competitors, helping you save on costs.
With over 100 experienced engineers and more than 200 state-of-the-art machines, we are the top choice for your prototyping and manufacturing needs.
Our services have received praise from numerous clients, and here are some testimonials from our happy clients.
Share your rapid prototyping or manufacturing needs with us now, and our expert team will deliver a quote to you within 24 hours.
Get in touch with our professional team today, and we will respond to you within 24 hours.
Marketing Director
Project Manager
Project Manager
Technical Sales
Technical Sales
Technical Sales
Get in touch with our professional team today, and we will respond to you within 24 hours.
Marketing Director
Project Manager
Project Manager
Technical Sales
Technical Sales
Technical Sales