When working on a project, engineers often want to know which process is better: urethane casting or injection molding. This is because both methods can be used to make small batches of plastic parts and prototypes. This article will compare the two processes to help you decide which one is best for your manufacturing needs.
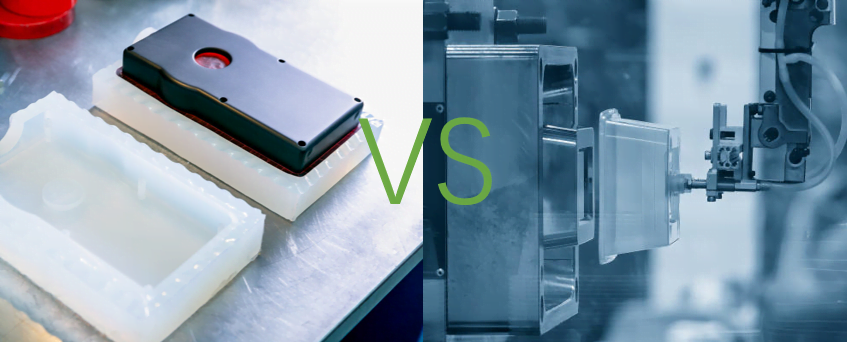
What is Urethane casting?
Urethane casting is a process used to make high-quality parts in small to medium quantities. It starts with a master pattern, which is usually made from a 3D-printed or CNC-machined prototype. This pattern is used to create a silicone mold. Then, liquid urethane resin is poured into the mold and left to cure. Once it hardens, you have a strong and detailed copy of the original pattern.
What is injection molding?
Injection molding is a popular process for making large numbers of plastic parts with high precision. Plastic pellets are melted and injected into a steel or aluminum mold under high pressure to fill the cavity of the mold. After the plastic cools and hardens, the mold is opened to release the finished part. Injection molding is known for being fast and reliable, producing consistent, and high-quality parts in large quantities.
While urethane casting uses hand-poured resin, injection molding requires special machines and automation to do the job.
Advantages of Urethane Casting over Injection Molding
Urethane casting is highly valued in manufacturing for its flexibility and range of advantages, especially when compared to the more rigid injection molding process. Here we list the major advantages of Urethane casting over injectionn molding:
Cost-effective for Small Runs
Urethane casting is a more affordable option when you need to produce only a small number of parts. The molds used in urethane casting are made from silicone, which costs much less to create than the metal molds used in injection molding. This makes urethane casting a great choice if you’re working with prototypes or small production runs, as you can keep costs low without needing to invest in expensive equipment.
Quick Turnaround
The process of making molds for urethane casting is much faster than injection molding. Silicone molds are quicker to produce, which means you can start making parts sooner. This is especially helpful in the early stages of product development, where getting parts quickly can help you test and refine your design without long delays.
Flexible Materials in Early Stage
With urethane casting, you have many options for the type of material you can use to make your parts. Urethane resins come in a wide range of hardness, flexibility, and durability. Whether you need a soft, flexible material or a hard, strong one, urethane casting allows you to choose exactly what you need for your project. This flexibility is great when you want to test different material properties before committing to a final product. In comparison, injection molding uses mainly thermoplastics like ABS, which are more limited in flexibility compared to urethane casting’s wide range of options.
Advantages of Injection Molding over Urethane Casting
Injection molding offers several key advantages over urethane casting, particularly when it comes to high-volume production. Its efficiency and consistency make it ideal for large runs, delivering precise, durable parts at a faster rate compared to urethane casting. let us find out the major points:
Efficient for Large Runs
Injection molding is ideal for producing large quantities of parts quickly and consistently. Once the mold is created, it can produce thousands or even millions of parts with little manual effort. This makes it highly efficient for mass production, where speed and cost-effectiveness are crucial. In contrast, urethane casting is slower and more labor-intensive, especially for larger volumes, making it less suitable for high-volume production.
Consistent Quality
Injection molding is known for producing parts with high precision. Once the mold is made, every part will be almost identical in shape, size, and quality. This level of consistency is especially important when you need exact measurements or design features. Urethane casting can also produce precise parts, but the quality may vary slightly between batches, especially for larger runs. Injection molding is more reliable when you need uniformity across a large number of parts.
Long-Lasting Molds
Injection molding uses metal molds, usually made of steel or aluminum, which are extremely durable. These molds can last for many years and produce hundreds of thousands of parts before needing replacement. This makes injection molding a better choice for ongoing, large-scale production. Urethane casting, on the other hand, uses silicone molds, which are much less durable. Silicone molds wear out after a certain number of parts, so they’re best for short runs or prototyping, but not for large-scale or long-term production.
Wide Range of Materials
Injection molding works with a wide variety of thermoplastic materials, such as ABS, polycarbonate, and polypropylene. Each material has its own unique properties, like strength, flexibility, or heat resistance, allowing you to choose the best one for your specific needs. This gives you more options to customize your parts for different industries, like automotive, medical, or consumer products. Urethane casting also offers material choices, but they’re more limited compared to the variety of thermoplastics available for injection molding. Additionally, urethane resins may not have the same mechanical properties as some thermoplastics used in injection molding.
Possibility of Material Reuse
Injection molding generates very little waste during production. Sprues, runners, and other leftover plastic can be easily ground down, melted, and recycled. This allows manufacturers to reuse material, cutting down on material costs and reducing waste. Urethane casting, while producing less waste overall, doesn’t offer the same level of material reuse, as the resin used in casting is often harder to recycle.

Urethane casting vs injection molding: Key Differences
While both methods are used for creating plastic parts with a mold, there are key differences between urethane casting and injection molding. let check them out:
Mold Tooling
The lifespan and maintenance of molds in these two processes are quite different, which affects their overall cost and suitability. In injection molding, molds are made from tough metals like steel or aluminum to handle high pressure and keep their shape. These metal molds are very durable and can last between 1,000 to 100,000 shots with good maintenance conditions.
However, urethane casting uses silicone rubber molds, which don’t last as long. They can wear out after making around 25 parts, this depends on the complexity of the part and the material used. This shorter lifespan makes urethane casting less suitable for long-term or high-volume production.
Lead time
Lead times for both processes depend on the complexity of the project and the number of parts needed. In injection molding, lead times can be longer, especially during the tooling stage. Simple parts may take 4 to 6 weeks, while more detailed designs might take 8 to 12 weeks or even longer.
In contrast, urethane casting usually has shorter lead times, making it ideal for quick prototyping and urgent projects. Simple parts can be ready in 1 to 2 weeks, while more complex parts might take 3 to 4 weeks.
Costs
A major difference between injection molding and urethane casting is their cost. in the case of small runs, the Urethane casting cost is much lower than the Injection molding cost. Here we explain from three components of the costs.
- Cost per Part: For high-volume production, injection molding is cheaper per part. For example, making 10,000 plastic gears might cost $2.00 each. Urethane casting is better for smaller runs, like 500 parts, where the cost per gear might be $3.50. The price varies depending on the design and materials.
- Tooling Cost: Injection molding uses expensive metal molds, general costs ranging from $1,000 to $100,000 and more, but they last a long time and are great for large production runs. Urethane casting uses cheaper silicone molds, but they don’t last as long and are better for small batches or prototypes. silicone molds cost ranging from $100 to $500 which is very low compared to injection molding metal molds.
- Material Costs: Injection molding uses thermoplastics, and the cost per part drops when produced in large quantities. Urethane casting uses resins, and the price can vary depending on the material properties needed.
Production Volume
Urethane casting is great for making a small number of parts, from one to a few hundred. It’s often used for prototypes or small production runs. Meanwhile, Injection molding is more suitable for making a large number of parts, from hundreds to millions.
Design flexibility
Urethane casting allows for more design flexibility compared to injection molding. This is because urethane casting uses flexible silicone molds that can accommodate design features like undercuts and small draft angles more easily.
Part materials
Urethane molding uses urethanes to create parts that look like those made with injection molding, while injection molding uses the actual production plastics. Both methods can mold parts that are either hard or soft. Anyway, You can make parts in standard colors, custom colors, or add textures with both techniques.
Tolerances
Achieving tight tolerances with cast urethane is challenging because the flexible silicone molds can shift during production. If precise dimensions are needed, urethane casting is not ideal. Metal injection molds offer better consistency since the hard molds don’t move. However, molten plastic contracts as it cools, so injection molding tolerances must account for slight size variations.
Injection molded parts typically have tolerances of 0.1mm for the first inch and 0.05mm for each additional inch. Urethane casting tolerances usually have larger tolerances with 0.2mm for the first inch and 0.1mm for each additional inch.
Undercuts
Undercuts are any protrusions or indentations that make it difficult to eject a part from a one-piece mold without causing damage. Urethane casting, with its flexible silicone molds, allows for easy adjustment to release the part if undercuts are present. In contrast, metal molds used in injection molding are less flexible. To handle undercuts, the mold may need extra features, like holes or slots, or a redesign to ensure the part can be ejected. This increases tooling complexity and cost.
Wall Thicknesses
The ideal wall thickness depends on the part’s size, shape, and function. For injection molded parts, a thickness of 1-4 mm is recommended for best results. Urethane casting allows for varying wall thicknesses, but some shrinkage or deformation may occur during curing. In both methods, keeping wall thickness under 5 mm and Uniform wall thickness is ideal.
Surface Finish
The surface finish and appearance of the final product are important when choosing a manufacturing method. Injection molding is known for producing excellent surface finishes. It can incorporate textures and colors directly into the mold, resulting in parts with precise details and smooth surfaces. Urethane casting also delivers good surface finishes, but it may not match the quality of injection molding without additional post-production work, like painting or surface treatments. These extra steps can increase both cost and lead time.
Urethane Casting vs Injection Molding: What are the Similarities?
Despite their differences, both urethane casting and injection molding share some important similarities that make them valuable manufacturing methods:
Use of Molds
Both processes rely on molds to create the final product. In each case, the mold cavity matches the exact shape of the part, with either urethane resin or molten plastic filling the cavity to form the part.
Part Geometry
Both methods can produce parts with intricate details and non-linear features, which might be difficult or impossible with traditional manufacturing. The mold cavity serves as a precise template, capturing the design’s nuances, including thin walls, undercuts, and sharp corners.
Material Options
Both processes offer a wide range of material options. Urethane resin can be formulated in different hardness levels, from rigid plastics to soft elastomers. Similarly, injection molding supports various thermoplastics, from rigid engineering resins to flexible rubbers.
Finishing Options
Both methods can produce parts with smooth, glossy finishes or textured matte surfaces. Post-processing techniques such as sanding, polishing, buffing, and media blasting are used to achieve the desired finish, whether for visual appeal or enhanced grip.
Urethane Casting vs Injection Molding: Which is Best for Your Project?
Choosing between urethane casting and injection molding depends on your project’s specific needs. you may need to figure out the following questions before making the decision.
1. What Is the Production Volume?
For large production runs, injection molding is generally the better choice due to its efficiency and lower cost per part at scale. Urethane casting is better suited for smaller volumes or prototypes.
2. What Are the Material Requirements?
Injection molding offers a wider range of thermoplastic materials, making it ideal for projects that need specific material properties. If urethane resins can meet your requirements, urethane casting is a cost-effective alternative.
3. How much of the accuracy of parts Needed?
The level of accuracy required for your parts also affects the choice between urethane casting and injection molding. Urethane casting can produce parts with good accuracy, but it may not match the high precision of injection molding, especially for complex or highly detailed designs. Injection molding offers greater precision, with tighter tolerances, making it a better option if your parts need to fit together perfectly or require exact measurements.
4. What Are the Lead Time Requirements?
Making molds for urethane casting is faster than for injection molding. Urethane casting usually takes 5 to 7 days, while injection molding requires at least two weeks for mold preparation. So, if you need parts quickly and in small numbers, urethane casting is better. However, urethane molds can only be used 10 to 25 times, while injection molds last for hundreds or even thousands of uses.
Conclusion
Both urethane casting and plastic injection molding have their own advantages and limitations. By considering your project’s needs—such as production volume, material requirements, and budget—you can choose the method that best suits your project. Whether you’re creating a prototype or preparing for mass production, understanding these manufacturing techniques will help you make an informed decision and achieve the best results.
At KUSLA Prototype, we offer both urethane casting service and injection molding services to meet your manufacturing needs. Our team of experts is ready to help you choose the right process for your projects and help you save your costs with high-quality molded parts. Contact us now for an instant quote.
FAQs
Is casting cheaper than injection molding?
Not really. The cost comparison between casting and injection molding depends on the volume of your project. For part cost, casting tends to be more expensive than injection molding due to higher labor costs and the manual nature of the process. However, for mold costs, casting is generally cheaper than injection molding, as silicone molds used in casting are less expensive to create compared to the complex, high-pressure molds required for injection molding. For large production runs, injection molding becomes more cost-effective due to its efficiency and speed in producing parts.
What are the alternatives to Urethane casting and injection molding?
Alternatives to urethane casting and injection molding include 3D printing, CNC machining, thermoforming, and compression molding. Each of these methods has its own advantages depending on the project’s requirements.