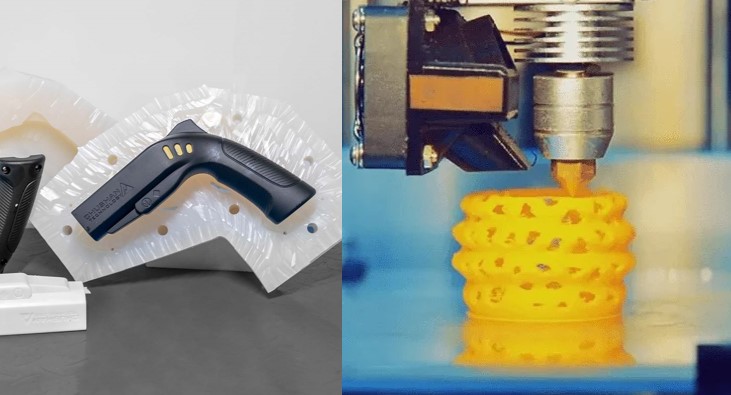
Urethane casting and 3D printing are both known for their cost-effectiveness in producing small-volume parts and prototypes across various industries, including medical devices, automotive, and consumer products. However, what are the key differences between them, and how do you choose the right method for your project? In this article, we will provide a detailed comparison to help you understand the differences and make the best decision for your needs.
Overview of Urethane casting
Urethane casting is a process where a liquid urethane material is poured into a silicone mold to create plastic parts. the silicone mold is created in a vacuum state based on a master pattern and the urethane casting parts are the replicas of the master pattern.
This method is great for making prototype parts and creating small batches of parts. it is cost-effective and quick, which makes it an good option for manufacturers looking to produce low-volume or pre-production parts.
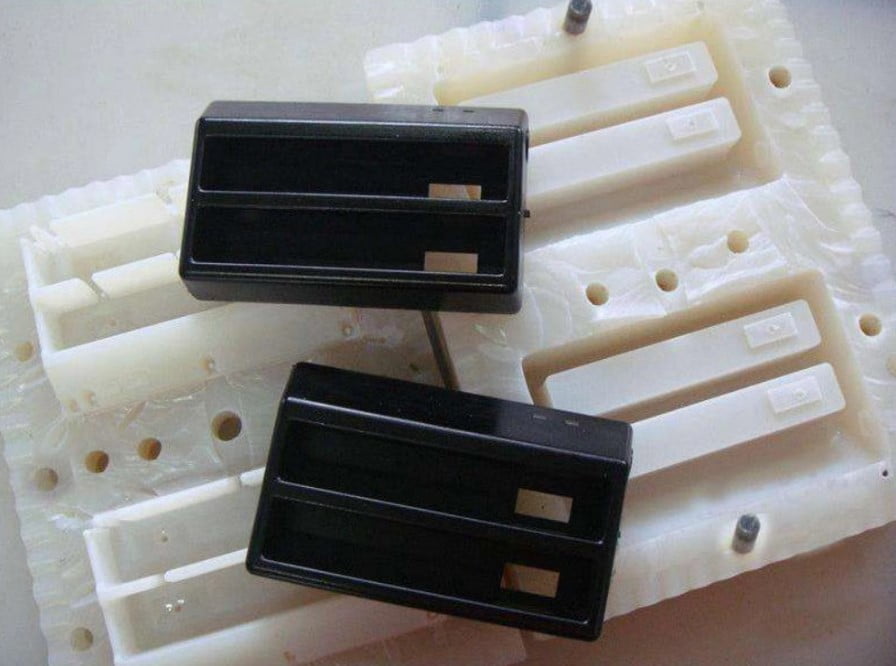
Advantages of Urethane casting
Before comparing urethane casting and 3D printing, let’s first take a look at the advantages of urethane casting.
Cost-Effective:
Urethane casting is often cheaper than 3D printing (additive manufacturing) when many prototypes are needed. 3D printing may require several builds for a larger batch, increasing the cost. In contrast, urethane casting can mold many parts in one go. The silicone molds used for urethane casting are also much cheaper than the aluminum or steel molds needed for injection molding. Silicone molds typically cost a few hundred dollars, while injection molds can cost tens of thousands.
Design Flexibility
Urethane casting offers great design flexibility. Since silicone molds are used, it’s easy to make design changes based on feedback without significant costs. Silicone molds wear out after 25-30 uses, so new molds can be quickly made with updated designs. This is much more affordable and faster than updating expensive injection molds. Also, urethane casting can create parts with difficult features, like undercuts or thick sections, that may be hard to achieve with injection molding.
Shorter Lead Times
The time needed to create molds for urethane casting is much shorter than for injection molding. While injection molds can take 4-12 weeks to make, silicone molds for urethane casting can be ready in just 1-2 weeks, regardless of part size.
Wide Range of Materials:
Urethane casting offers a wide variety of materials, including rigid and flexible options. These materials can be customized in terms of hardness (durometer), color, and specifications, including clear, FDA-approved, and UL-certified materials. Urethane casting can also over-mold onto plastic or metal components, giving more flexibility in part design.
Custom Part Finishes
Urethane cast parts can be finished to look similar to injection-molded parts. They can be custom-colored, textured, and painted, giving them a professional look even after wear and tear. If parts are scratched or damaged, the finish can be restored, keeping the parts looking good over time.
Overview of 3D printing
3D printing is a process that creates plastic parts by building them layer by layer from a digital 3D model. The printer deposits a plastic resin or material, which solidifies as each layer is added to form the final part. There are several types of 3D printing methods, including FDM (Fused Deposition Modeling), SLS (Selective Laser Sintering), SLA (Stereolithography), and DMLS (Direct Metal Laser Sintering). Each method uses different techniques and materials, making 3D printing a good option for creating custom parts, prototypes, and complex geometries.
3D printing also allows for easy customization without the need for large production runs, making it ideal for small batches and prototypes.
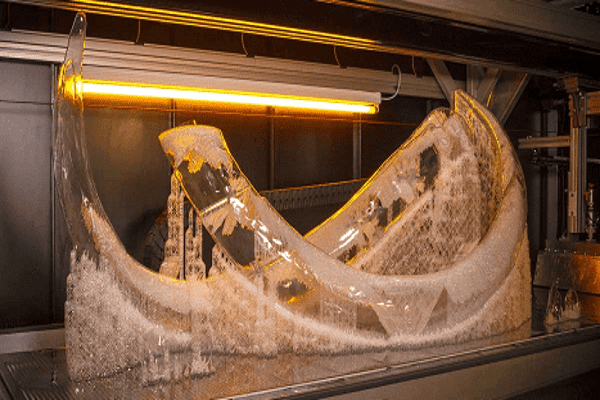
Advantages of 3D printing
By reviewing the advantages of 3D printing, you can gain a better understanding of the process. Let’s take a look at the key benefits it offers.
Fast Speed
One of the biggest advantages of 3D printing is rapid prototyping, which allows you to quickly design, create, and test parts. Unlike traditional methods, where prototyping could take weeks and involve long delays for changes, 3D printing lets you make adjustments and produce parts in a matter of days—sometimes even less. For small businesses or individuals, this speed is especially important as it eliminates the need for expensive machinery and long lead times.
Cost-Effective
For small production runs, 3D printing is much more cost-effective than traditional manufacturing methods like CNC machining or injection molding. Traditional methods require expensive machines and skilled labor, increasing both the cost and complexity. In contrast, 3D printing typically requires fewer machines and less labor, leading to lower costs. It also creates less waste because parts are built layer by layer instead of being carved out of solid material, which further reduces costs.
Flexibility
3D printing offers unmatched flexibility. Unlike traditional methods, which need new tools or molds for each new part, 3D printing only requires the design to be loaded into the printer, with little to no change in the equipment. This means you can quickly modify designs without major setup changes. 3D printing also allows you to create complex shapes, like hollow parts or internal features, that would be impossible or costly to make with traditional methods. You can even combine multiple materials in a single print, giving you more design options in terms of texture, color, and mechanical properties. Whether you’re a beginner or an expert, 3D printing makes it easy to edit and customize designs, allowing for unique and personalized parts.
Comparison of urethane casting vs 3D printing
Both urethane casting and 3D printing are fast, cost-effective, and offer design flexibility. However, they differ in several ways. Let’s compare these two processes based on key factors:
Lead time
Urethane casting involves two main steps that can affect lead time: creating the silicone mold and curing the cast parts. The process of making the mold itself can take a day or two, depending on complexity, and the casting process requires additional time for the parts to cure, typically taking several hours. This results in a longer overall lead time for urethane casting.
In comparison, 3D printing tends to be faster. Since 3D printing doesn’t require the creation of molds, the lead time is usually much shorter. Once the design is prepared, the printer can create the part in a matter of hours, and sometimes even less than a day. Therefore, in terms of lead time, 3D printing is generally faster than urethane casting, with most 3D printing projects taking under a day to complete, whereas urethane casting typically takes around 2-3 days to finish.
Cost
Both urethane casting and 3D printing offer cost-effective solutions for producing plastic parts. However, the material used in urethane casting is typically less expensive than the materials used in 3D printing. When considering the cost of the silicone mold, urethane casting becomes more cost-effective for larger production runs. Generally, when the volume exceeds 20 pieces, urethane casting is more economical than 3D printing. On the other hand, for smaller production runs—typically fewer than 10 parts—3D printing tends to be the more cost-effective choice, as it eliminates the need for mold creation.
Design Flexibility
Both urethane casting and 3D printing offer strong design flexibility, but in different ways. urethane casting provides design flexibility when creating parts with detailed or hard-to-mold features, while 3D printing excels in producing highly complex geometries and rapid design iterations without the need for molds or additional tooling. Both processes support customization, but 3D printing offers more freedom for unique and one-of-a-kind designs.
Production Volume
Urethane casting is ideal for producing small batches of parts, especially when the quantity is over 20 pieces. The silicone molds used in urethane casting make it efficient for creating multiple parts at once, making it a great option for low-to-medium volume production runs. In contrast, 3D printing is better suited for creating parts one at a time, as it offers quick lead times and doesn’t require the setup of molds. This makes 3D printing a good choice for very small production runs or custom, on-demand parts.
Strength
Generally, urethane casting parts are stronger than 3D printed parts when using similar materials. This is because urethane casting produces parts in one solid piece, which provides better strength and durability. In contrast, 3D printing builds parts layer by layer, which can sometimes lead to weaker points between the layers, affecting the overall strength of the part.
Temperature Resistance
Urethane casting parts generally have better temperature resistance than 3D printed parts. This is partly due to the stronger structure of urethane casting, as mentioned earlier. Additionally, there is a wider selection of high-temperature materials available for urethane casting, offering better heat resistance compared to the materials commonly used in 3D printing. As a result, urethane casting is often the better choice for applications that require parts to withstand higher temperatures.
Precision
In terms of precision, 3D printing generally offers better accuracy than urethane casting. 3D printed parts can achieve tolerances as tight as 0.15 mm, while urethane casting parts typically have a tolerance of around 0.2 mm. This difference is due to the deformation of the silicone mold during the casting process, especially at high temperatures, which can slightly affect the final part’s precision.
Appearance
When it comes to appearance, urethane casting parts generally do better. Urethane casting creates smooth, high-quality surfaces similar to those produced by injection molding. In contrast, 3D printed parts often have visible layer lines and may not be as smooth. To achieve a similar surface finish, 3D printed parts typically require additional post-processing steps like polishing or sanding.
Conclusion
Both urethane casting and 3D printing are excellent options for prototypes and small-volume production. The choice between these two processes depends on specific project requirements such as volume, quality, and budget. KUSLA, which specializes in both urethane casting service and 3D printing prototyping service, can help you determine the best solution for your needs. Contact us today for expert guidance on your rapid prototyping and part manufacturing projects.
FAQ
Is Urethane casting cheaper than 3D printing?
Generally, the cost comparison depends on the volume of parts you need. For a single part, 3D printing is usually cheaper since it doesn’t require the additional cost of making a mold. However, when the production volume exceeds a certain threshold—around 20 pieces—urethane casting becomes more cost-effective than 3D printing due to the lower cost of materials and the efficiency of using silicone molds for multiple parts.
What is the difference between 3D printing and Urethane casting?
The main difference between the two processes is that urethane casting is ideal for low-volume pre-production, allowing you to produce several parts quickly and cost-effectively. On the other hand, 3D printing is best suited for creating a small number of rapid prototypes, where speed and design flexibility are key, but it may not be as cost-effective for larger production runs.