Urethane casting cost is a key factor in a plastic prototype project. It is a low-cost solution for plastic prototyping when small quantities are required. However, how much does urethane casting cost? What factors affect the urethane casting cost? How is it calculated? This article will answer these questions for you.
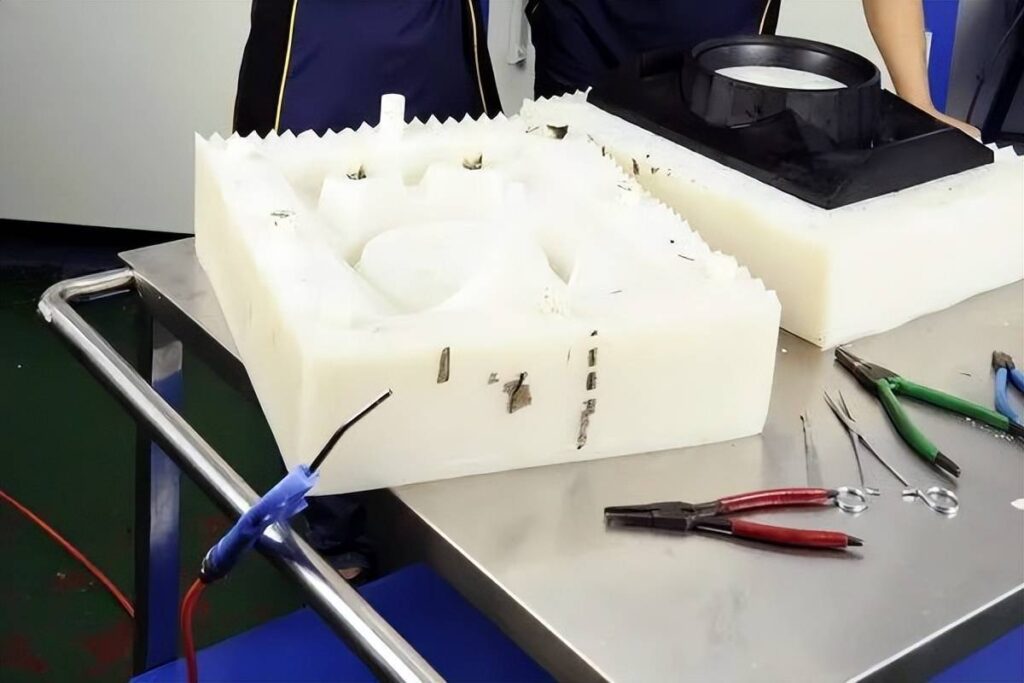
What is Urethane casting?
Urethane casting utilizes liquid polyurethane resin, which is poured into a silicone mold to create plastic or rubber parts under vacuum conditions. It is a cost-effective method for producing a small series of parts, typically ranging from 10 to 100 units.
Urethane casting Processes
Before you understand the cost of urethane casting, it is important to first understand the process, as each step contributes to the final cost of the urethane parts.
Master Pattern Creation
The first step is to create the master pattern part using CNC machining or 3D printing. CNC machining is commonly used to create parts with a smooth surface, such as clear parts. 3D printing is ideal for parts with complex structures.
Making the Silicone Mold
The master pattern is surrounded by a mold frame, and then liquid silicone material is poured into it. After solidification, the silicone mold is formed. Once the mold is cured, it is removed, and the mold is cut along the product’s parting line. The master pattern is then removed, leaving the mold cavity empty.
Casting Urethane Parts
The liquid urethane material is poured into the silicone mold under vacuum conditions. The urethane part is then heated and cured at a high temperature to create a replica of the mold cavity.
Post-processing
Once the urethane part is cured and removed from the silicone mold, post-processing is required, such as removing burrs and gates, repairing pores, polishing, and conducting assembly tests.
Surface Finishing
The final step is surface finishing on the urethane parts according to the specific requirements, such as spray painting, screen printing, laser engraving, etc.
Factors that affect the cost of urethane casting
After understanding the urethane casting process outlined above, you can better understand the key factors that affect the cost of urethane casting, as explained below.
Master Pattern
The cost of a master pattern is similar to that of manufacturing a one-off prototype through CNC machining or 3D printing. 3D printing is a low-cost solution for creating master patterns. So, if you want to lower the total cost of urethane casting parts, choose 3D printing for making the master pattern whenever possible.
Silicone mold
Typically, the cost of a silicone mold used for urethane casting ranges from $50 to $500, but it can vary significantly depending on factors such as its nature, size, complexity, and manufacturing location. The cost of the silicone mold can be amortized across the unit cost, meaning that the more prototypes you produce, the lower the unit cost will be.
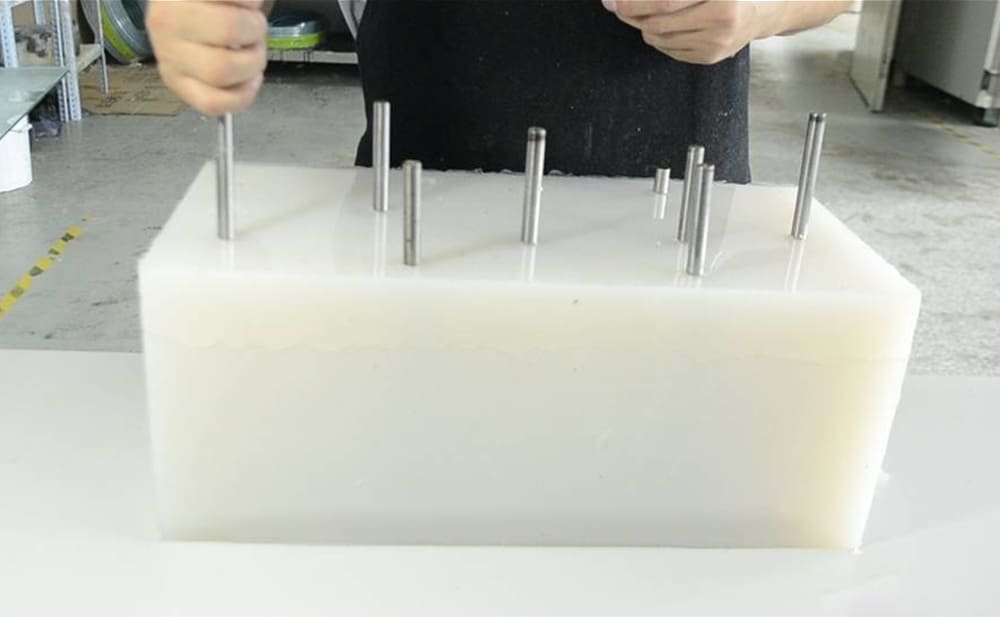
Urethane Casting material
Typically, the cost of urethane casting materials ranges from $0.50 to $1.50. Urethane casting materials are varied, with different types representing thermoplastics such as ABS, nylon, or PC-like materials. There are several brands available, and the prices can vary significantly.
Surface finishes
Surface finish is another factor that affects the urethane casting cost, as surface finish costs vary depending on the technique used, such as spray painting, screen printing, or laser engraving. These techniques also contribute to the final cost of the urethane part.
How to Calculate Urethane casting cost?
The total urethane casting cost is calculated as: master pattern cost + silicone mold cost + (unit urethane part cost * quantity). The silicone mold typically supports only up to 25 copies, so if the quantity exceeds 25, a new silicone mold is required. The unit urethane part cost is calculated as: urethane material cost per gram * part weight + surface finish cost.
Urethane casting cost overview
Urethane casting usually works for a production volume of 10 to 100 units. On average, the urethane casting for small parts is around $100 – $1000 in total, and the per-unit price ranges from $10 to $100. let us take an example with 10 – 100 parts run to explain each item:
Assume plastic part information:
- Plastic part size: 100mm*100mm*10mm
- Thickness: 2mm
- weight: 20g
- material: ABS-like plastic
The Urethane casting cost is calculated below:
- Number of parts: 10 Units
- Mater pattern cost by CNC machining: $100
- Unit material cost: $5
- silicone mold cost: $100
- Unit surface finishing cost: $0.5
- Logistic cost per part: $0.5
- total volume cost: $100+$100+($5+$0.5+$0.5)*10=$260
- Final cost per Part: $26
Tips for Reducing the cost of urethane casting
Here are some tips according to our experiences of many projects:
- Use a carton box as a mold frame
- Use proper and low-cost urethane materials
- Simplify the product geometry
- design constant wall thickness
- Order quantities according to the capacity of one silicone mold
- Reduce Waste during casting and mold design
Conclusion
This article explains how to calculate the urethane casting cost according to all the factors, However, to get an accurate budget or price for your urethane casting project, you need to work with a professional manufacturer of urethane casting service. At KUSLA, we’re experienced with urethane casting service and Our expert team can provide technical assistance, ensuring your designs are optimized for the casting process.
FAQ
Is urethane casting expensive?
It depends. Urethane casting is much less expensive than other rapid prototyping methods such as CNC machining and injection molding when you want production parts in small batches of 10 to 100 pieces.
What is the lead time for urethane casting?
Urethane casting parts can be ready in as few as one to two weeks, no matter the part size.