Casting is one of the oldest and most well-known manufacturing methods in the world. For over seven thousand years, the casting process has been continuously used and improved. Even with advancements in modern manufacturing methods, casting remains effective and efficient because it is affordable, easy to use, simple, and versatile. It works well with many different materials, making it valuable in today’s world.
Casting plays an important role in helping businesses and manufacturers control costs while producing high-quality items. This process allows materials to be shaped into finished products that are useful across many industries, such as consumer goods, automotive, and aerospace. It enables the creation of unique designs and functional products or components for different needs. This article will explain the casting process in more detail, discuss the different types of casting methods, and highlight the key benefits and applications of casting.
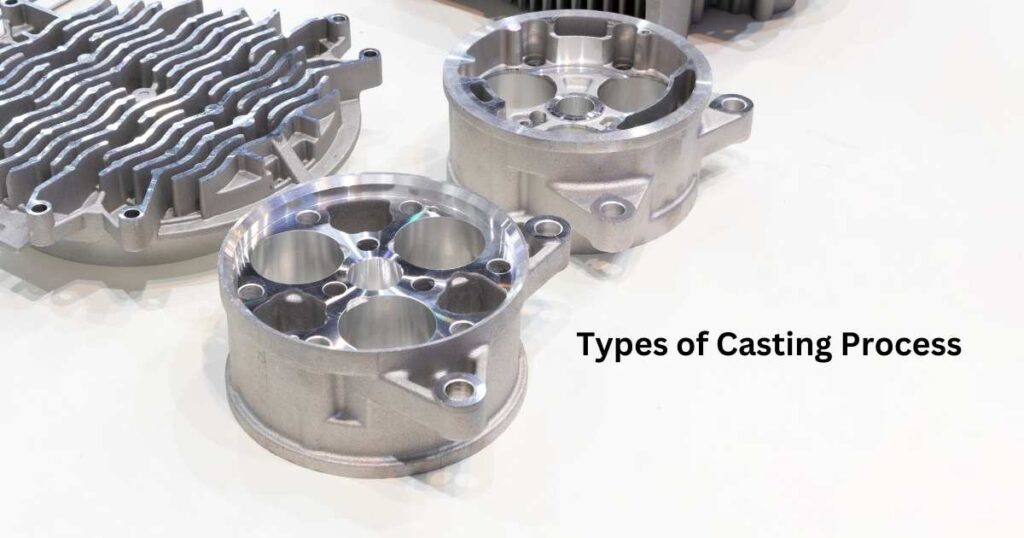
What is Casting?
Casting is a manufacturing process used to create parts in specific shapes by pouring molten material into a mold. The material is left to cool and solidify at room temperature, forming the desired part. This method can produce parts of all sizes, even those with complex and detailed designs.
Casting is a reliable method for producing large quantities of metal parts with uniform properties, making it ideal for mass production. Additionally, there are various types of casting processes, each designed to suit specific materials and molds to meet different user needs.
How Does Metal Casting Work?
The metal casting process involves four main steps. Here’s a simple breakdown of each step, from design to the finished product:
Making the Pattern
The first step is creating a pattern, which is a model of the final product. This pattern is used to shape the mold. Materials like wax, wood, or plastic are commonly used, depending on the type of casting.
Creating the Mold
Next, a mold is made based on the pattern. The mold is typically made from materials like sand, clay, or ceramic, which can handle the high heat of molten metal. The mold forms the hollow space where the metal will be poured.
Melting and Pouring the Metal
The metal or alloy needed for the product is selected and melted in a furnace. Once it is fully liquid, the molten metal is carefully poured into the mold to fill its shape. This step must be done carefully to avoid defects like air pockets.
Cooling, Removing, and Finishing
After pouring, the metal is left to cool and solidify in the mold. Once solid, the cast piece is removed. Finally, finishing techniques like sanding, grinding, or machining are used to make the cast product smooth and ready for use.
Different Types of Casting Process
Engineers use different casting methods to shape raw materials into precise parts and components. Each type of casting process is designed to suit specific materials, meet the required properties of the final product, and ensure manufacturing efficiency. Below are some popular types of casting processes.
Sand Casting
Sand casting is a popular method for shaping hot liquid metals or alloys into complex objects. It uses molds made of sand, typically designed in multiple halves or with cores. These molds create impressions of parts from different angles, and when combined, they form the final shape of the product. Special features in the mold allow the molten metal to flow smoothly through the design.
The sand used in this process isn’t the same as beach sand. It’s usually silica-based, chemically bonded, or “green sand.” Depending on the design, the mold may be reused or discarded after casting. Once the metal solidifies, the part undergoes finishing processes like grinding or machining to remove extra material and refine details.
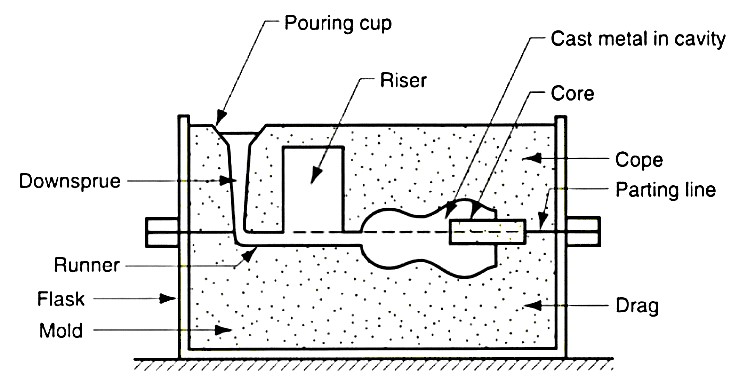
Key Benefits of Sand Casting:
- Simple and cost-effective mold-making process.
- Works with almost any alloy, both ferrous and non-ferrous.
- Can produce parts in a wide range of sizes, even those weighing over 200 tons.
- Post-processing is easy and quick, even though dimensional accuracy is lower.
Applications:
- Engine cylinder blocks, heads, and crankshafts.
- Jewelry and decorative items.
- Automotive and industrial castings.
Gravity die casting
Gravity die casting, also known as permanent mold casting, is a process where molten metal is poured into reusable molds made from materials like steel or iron. Unlike other casting methods, the metal flows into the mold using gravity rather than being forced. This technique produces components with consistent shapes and high precision.
This process is ideal for creating large volumes of small to medium-sized metal parts with uniform wall thickness. It is commonly used for non-ferrous metals like aluminum, magnesium, and copper alloys.
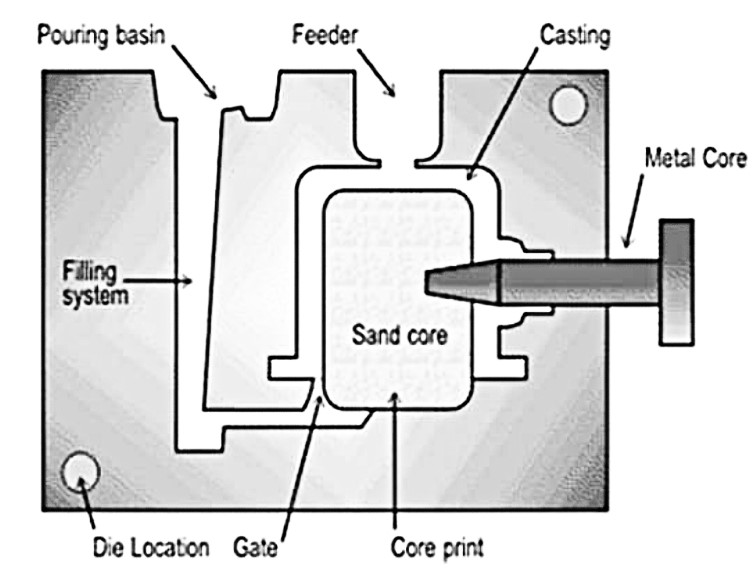
Key Benefits of Gravity Die Casting:
- Provides better dimensional accuracy and a smoother surface finish.
- Produces parts with stronger mechanical properties due to denser structures and faster cooling rates.
- Offers quicker production cycles, making it efficient for larger production volumes.
Applications:
- Gears, splines, and wheels.
- Cookware and pipe fittings.
- Gear housings, fuel injection housings, and pistons for automotive engines.
- Various other automobile components.
High Pressure Die Casting
High pressure die casting is a fast and efficient method that uses high pressure, speed, and heat to create flawless, consistent products. In this process, molten metal is injected into a mold at high pressure, ensuring it fills the mold completely and solidifies quickly. This technique is highly effective for producing detailed and precise parts that are easy to reproduce in large quantities.
To achieve the best results, it’s important to carefully control the machine’s settings, such as pressure and capacity, to ensure the metal fills the mold properly and cools as needed. High pressure die casting is widely used across various industries, from making toys to manufacturing automotive and appliance parts.
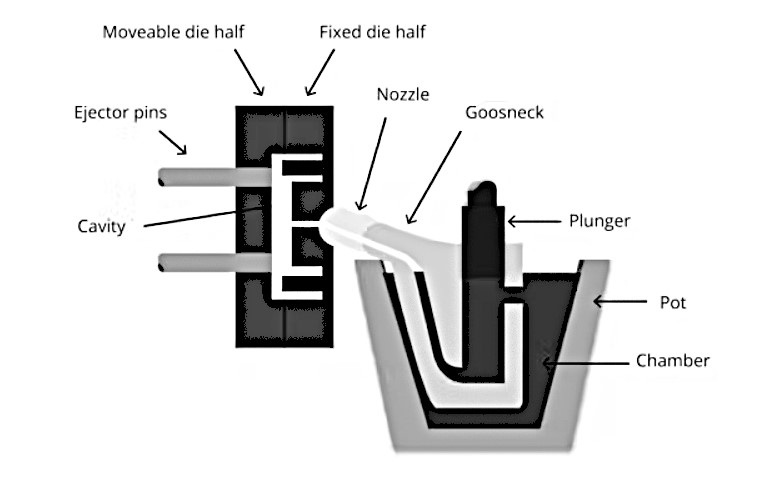
Key Benefits of High Pressure Die Casting:
- Produces highly accurate and detailed parts with excellent surface finishes.
- Offers rapid production cycles, making it ideal for mass production.
- Reduces the need for extensive post-processing.
Applications:
- Toys, tools, and other metal products requiring precision.
- Automotive parts such as engine components and housings.
- Appliances and electronic casings.
Low-Pressure die Casting
Low-pressure die casting uses lower pressures (0.02–0.06 MPa) to mold molten metal, creating strong and durable parts with accurate shapes and smooth fills. This method is ideal for components requiring intricate details, sharp edges, and smooth surfaces but is less suitable for thin-walled parts or fast production cycles.
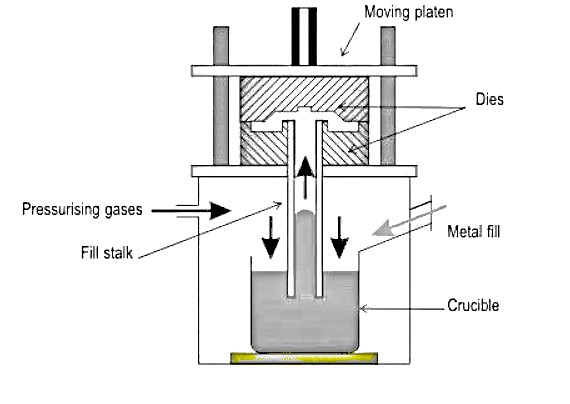
Key Benefits of Low-Pressure Die Casting:
- Precise control of molten metal flow reduces defects like porosity and shrinkage.
- High accuracy and ability to create intricate designs and sharp corners.
- Produces dense, high-strength structures with smooth surfaces, ideal for large or thin-walled components.
Applications:
- Cylinder hubs and frames.
- Wheel hubs.
- Kitchenware and custom hollow parts.
Vacuum Casting
Vacuum casting involves pouring liquid materials like silicone and polyurethane into a vacuum chamber mold to prevent air bubbles and ensure high-quality finished products. This process is used to create polymer parts in silicone cavities and uses heat, pressure, and vacuum to produce hardened components. It is perfect for creating high-quality prototypes, small production runs, and parts with smooth surfaces and fine details, such as custom models, medical devices, and vehicle components.
Vacuum casting is particularly valuable for accurately copying detailed designs while maintaining the original texture of the prototype. Different resins can be used to achieve various material properties, such as stiffness or flexibility. The molds are easy to create and cost-effective, making vacuum casting ideal for small-batch production. Urethane casting is a common form of vacuum casting, known for its versatility in producing durable, fine-quality parts.
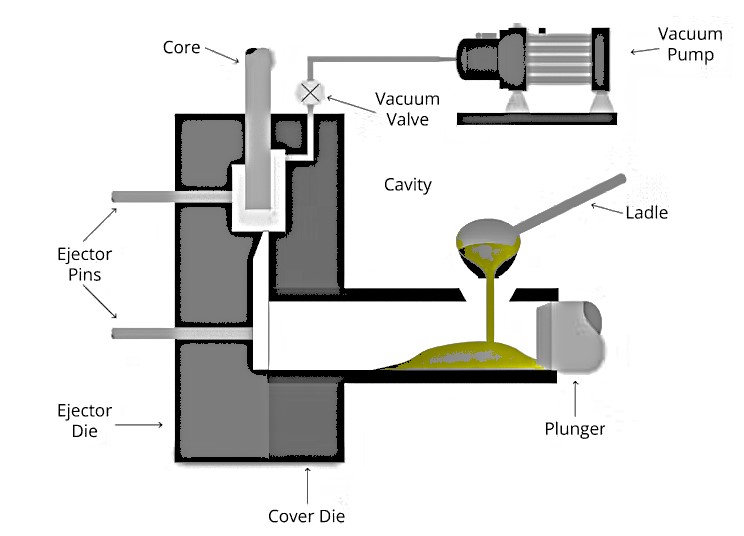
Key Benefits of Vacuum Casting:
- High precision and accuracy, especially for 3D printed molds.
- Produces fine castings with intricate details.
- Eliminates the risk of pore formation inside the cast.
- Can cast parts with thinner walls.
Applications:
- Functional plastic prototypes, medical implants, and prosthetics.
- Consumer goods, automotive body panels, and other components.
- Food processing components and more.
Investment Casting
Investment casting, also known as lost-wax casting, has been around since the Bronze Age and is still used today to create a variety of products, such as gas turbines, jewelry, and medical devices. It’s commonly used in industries like aerospace, automotive, and healthcare, where parts require complex designs, precise dimensions, and high-quality materials. Examples include turbine blades, gun parts, and medical implants.
The process begins with creating a wax pattern of the desired part, which is then covered in a ceramic shell. After the wax is melted and evaporates, molten metal is poured into the mold to form the final product. Investment casting can use various materials, including metals like stainless steel, bronze, and titanium. The process offers excellent precision and smooth surfaces with minimal material waste.
Key Benefits of Investment Casting:
- Allows the creation of hollow sections, undercuts, and internal channels without the need for a core.
- Provides a fine grain structure and a smooth surface finish.
- Offers good dimensional accuracy (± 0.1mm) and the ability to produce thin-walled, complex parts.
Applications:
- Military and aircraft engine parts.
- Complex components in industries like aerospace, automotive, and healthcare.
Shell Molding
Shell molding, also known as shell mold casting, is a precision casting process that uses a sand-resin mixture to create a mold around a heated metal template. First, a metal pattern is heated, and then a coating of sand mixed with a thermosetting resin is applied. This mixture hardens into a thin shell, forming one half of the mold. The process is repeated to create both halves of the mold, which are then joined to form the final mold cavity. After the molten metal is poured into the mold and cooled, the shell is broken to reveal the finished part.
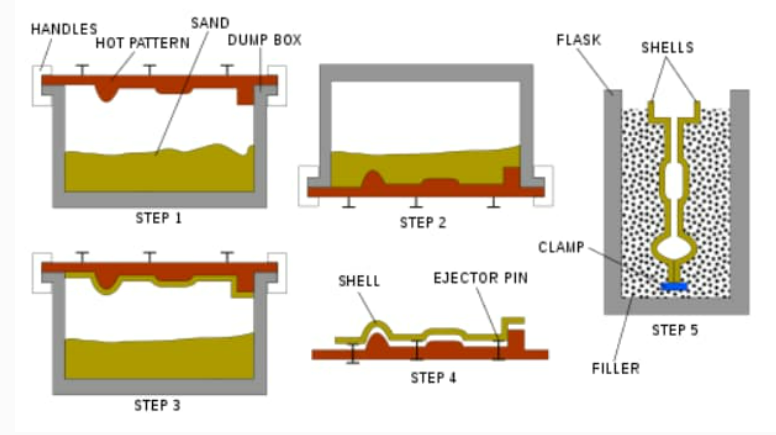
Key Benefits of Shell Molding:
- Excellent surface finish and high accuracy in size and shape, especially for thin sections.
- Produces parts more quickly and with less waste than traditional sand casting.
- Ideal for medium to large batches, offering precise dimensions.
Centrifugal Casting
Centrifugal casting, also known as roto casting, involves pouring molten metal into a revolving mold to create cylindrical parts. As the mold rotates rapidly, the centrifugal force pushes the molten metal outward, causing it to press against the inner walls of the mold and form the desired shape. This process is ideal for producing large quantities of standardized products, such as pipes, flywheels, and cylinder liners. It can also be used with various materials.
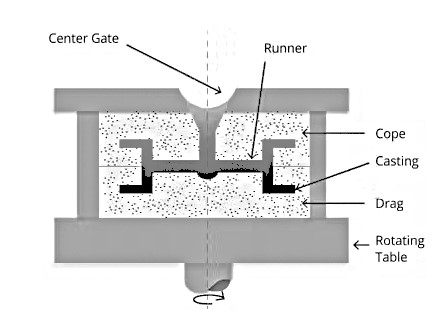
Key Benefits of Centrifugal Casting:
- Eliminates porosity due to continuous metal feeding.
- Reduces the risk of gas pockets and shrinkage cavities as the metal solidifies inward.
- No riser is needed, reducing material waste during pouring.
- Results in a dense, homogeneous grain structure for better strength and durability.
Applications:
- Hollow cylinders, shaft sleeves, pipes, tubes, pressure vessels, and disk shapes.
- Primarily used for symmetrical, large-scale production parts.
Continuous Casting
Continuous casting is a method used to turn melted metal into semi-finished products, such as billets, blooms, or slabs, which may require further processing. As the molten metal is poured into water-cooled molds, it solidifies as it moves through the system. While the metal forms a hard outer shell, the inside remains liquid. The metal is then cut into appropriate lengths for further processing.
Key Benefits of Continuous Casting:
- Produces high-quality metal with minimal defects like porosity or inclusions.
- Offers better metal quality, lower scrap, and more economical production.
- Reduces energy consumption and costs compared to traditional casting methods.
Applications:
- long castings with constant cross-sectional shapes, such as ingots, slabs, billets, pipes, and more.
Lost-foam Casting
The lost-foam casting method is similar to investment casting, but instead of using wax, it uses foam to create the pattern. After the pattern is formed, it is coated with a refractory ceramic through dipping, spraying, brushing, or coating. Then, molten metal is poured into the mold to create the final product. This technique can be used with materials like alloy steel, carbon steel, alloy cast iron, and ferrous alloys.
Key Benefits of lost-foam casting
- Allows for intricate geometries with excellent surface quality.
- Provides high precision.
- No parting surface, offering flexible design and a high degree of freedom.
- Clean production with no pollution.
Applications
- pump housings, fire hydrants, valves, and fittings.
Conclusion
Overall, casting is a prominent manufacturing technology for producing complex metallic parts that require high strength, structural integrity, wear and corrosion resistance, and precise tolerances. It is widely used in various industrial applications. The diversity of casting methods, ranging from sand casting to die casting and lost foam casting, makes it adaptable to meet a broad range of manufacturing needs.
Whether you’re creating a prototype for testing or planning a small production run, expertise in these casting techniques provides a solid foundation for making informed decisions. From urethane vacuum casting to aluminum die casting and the advanced processes used by companies like Kusla Prototype, you have various options to bring your ideas to life.
FAQ
How many casting methods are there?
There are over 12 different casting methods used in manufacturing, each offering its own advantages depending on the material, design, and production requirements. Some of the most common casting methods include sand casting, low-pressure die casting, high-pressure die casting, investment casting, vacuum casting, gravity die casting, and centrifugal casting.
What is the cheapest casting process?
The cheapest casting process depends on the production volume and the specific requirements of the part being produced. For large-volume production, die casting is often the most economical choice due to its rapid production cycle and ability to produce parts quickly and efficiently. For lower to medium production volumes, methods like sand casting or investment casting may be more cost-effective, as these processes have lower setup costs and are suitable for smaller batches.
What is the best casting process for intricate design parts?
Investment casting is considered the best casting process for intricate design parts. It allows for the creation of components with complex shapes and fine details while maintaining high dimensional accuracy. This method is ideal for parts that require smooth surfaces, tight tolerances, and intricate geometries, making it popular in industries such as aerospace, automotive, and healthcare.