Plastic products are everywhere in our lives, available in different types, shapes, and properties. They are the most common components in various industries, such as consumer products and medical devices. To make these plastic products, a wide variety of manufacturing processes are used to cover a broad range of applications.
This article provides a comprehensive guide to plastic manufacturing processes for designers and engineers working in product development. It will help you understand nearly all the manufacturing options available today and how each process works. Let’s dive in!
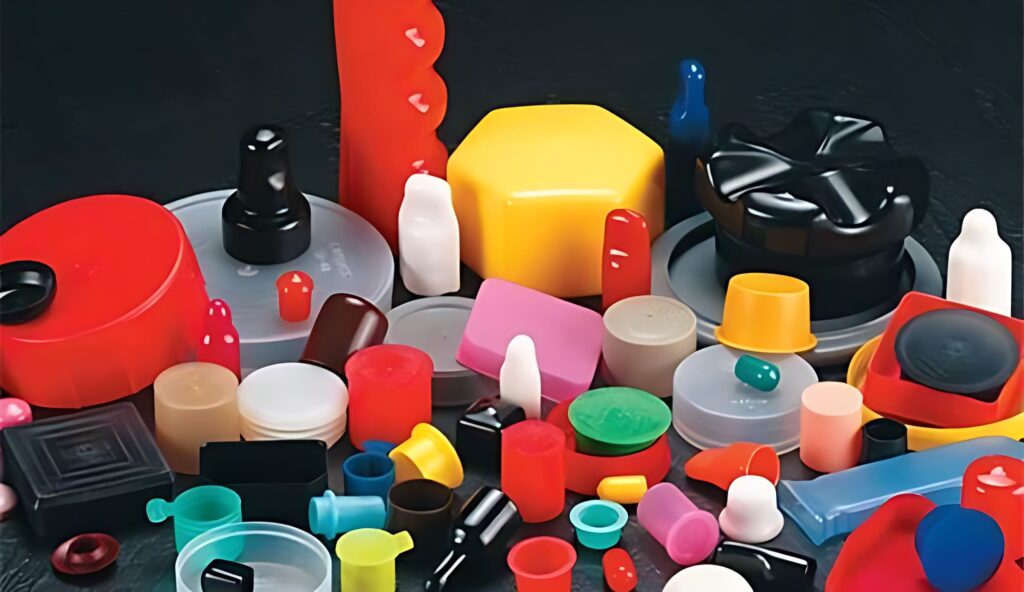
Plastic Materials form: Pellets, Resins, and Powders
Before diving into the plastic manufacturing processes, it’s important to understand what plastic is and the different types of plastics available.
Plastic is a synthetic or semi-synthetic material made from polymers. At room temperature, it exists in various forms, such as pellets, resins, and powders. These materials are then heated during manufacturing to shape or mold them into parts. Let’s check each of these plastic material forms:
Pellets
Most engineering plastics are produced in the form of pellets, which are small, solid granules. These pellets are then melted by heat and molded into desired shapes through processes like injection molding or extrusion. This is the most common form for high-volume manufacturing.
Resins
Resins are typically the raw polymer material used in plastic production. They can be in liquid or solid form and are often used in molding or casting processes. For example, urethane resins are popular for their flexibility and durability, making them ideal for applications like seals, gaskets, and coatings.
Powders
Plastic powders are often used in processes like powder coating or 3D printing. These fine particles can be melted and fused to create solid parts. Materials like nylon or polyamide powders are frequently used in 3D printing for their strength and versatility in creating complex shapes.
Types of Plastics
Plastics can be divided into two main types: thermoplastics and thermosetting plastics. Let’s take a closer look at each:
Thermoplastics
Thermoplastics are plastics that can be softened and shaped when heated. Once cooled, they harden again and can be reheated and reshaped. This makes them recyclable and reusable. Thermoplastics are often used for parts that need to be molded.
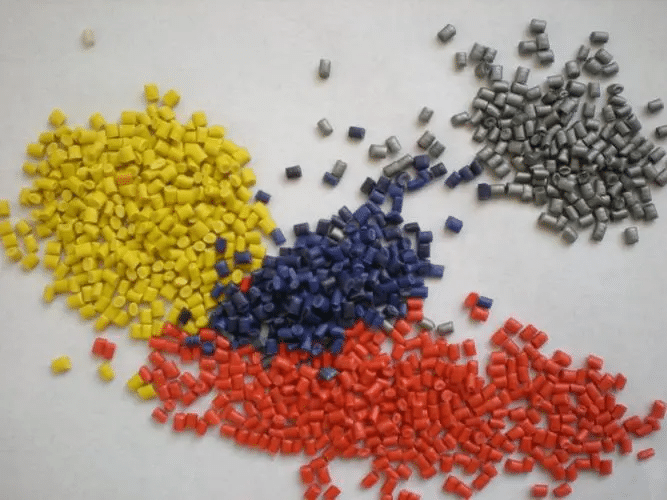
Common types of thermoplastic materials:
- Polyvinyl chloride (PVC)
- Acrylic (PMMA):
- Acrylonitrile butadiene styrene (ABS)
- Polyamide (PA)
- Polylactic acid (PLA)
- Polycarbonate (PC)
- Polyether ether ketone (PEEK)
- Polyethylene (PE)
- Polypropylene (PP)
Thermosetting Plastics
Thermosetting plastics are different because they harden permanently after being heated or chemically treated. Once set, they cannot be reshaped or remelted. These plastics are known for their strength, heat resistance, and stability, making them ideal for parts that need to handle extreme conditions.
Common types of thermoplastic materials:
- Cyanate ester
- Epoxy
- Polyester
- Polyurethane
Introduction to Plastic part manufacturing process
Plastic manufacturing is the process of transforming raw plastic materials, such as powders, pellets, or liquid resins, into finished products with the desired shape. The process includes several key steps to ensure high-quality plastic parts. These steps include preparing the materials, polymerizing, adding additives, molding, and finishing. Let’s take a look at each of these processes.
Material Preparation
Material preparation is the first step in the plastic manufacturing process. It involves extracting and refining raw materials, primarily hydrocarbons sourced from coal, natural gas, and petroleum.
Polymerization
The next step is polymerization, where monomers are chemically bonded to create plastic polymers—large, chain-like molecules. Different polymerization methods are used depending on the plastic type. For example, polyethylene and polypropylene are made through addition polymerization, while nylon and polyester are created through condensation polymerization. Resin is commonly used in this process.
Additives
After polymerization, additives are mixed into the plastic to enhance its properties such as color, strength, heat or UV resistance, flexibility, and more. Common additives include plasticizers, stabilizers, flame retardants, and colorants. The specific additives used depend on the desired properties of the final product.
Molding
In this step, plastic form to final shape through molding process. Various molding techniques are used, including rotational molding, blow molding, extrusion, and injection molding. The choice of method depends on the plastic type, part complexity, and production volume. For example, extrusion is ideal for creating long, continuous shapes, while injection molding is suited for complex parts in large volumes. For small runs or prototypes, CNC plastic machining and 3D printing are more suitable.
Finishing
The final stage of plastic manufacturing is finishing, which includes post-processing steps to refine the part’s appearance and functionality. The specific finishing process depends on the product’s needs. For example, a car part might need painting to match the vehicle’s color, while a plastic bottle might require printing for branding and labeling.
Common Types of Plastic Manufacturing Processes
Various plastic manufacturing processes are widely used due to their versatility and ability to produce a wide range of products. let us dive into the details of each one.
Injection Molding
Injection molding is a widely used plastic manufacturing process where molten plastic pellets are injected into a mold, cooled, and cured to form the final shape. The molding cycle is fast, typically ranging from a few seconds to a few minutes, making it ideal for high-volume production of parts with simple geometries.
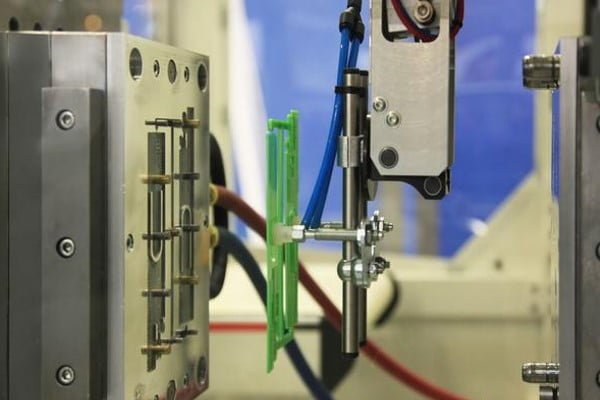
Advantages of Injection Molding:
- Can produce complex shapes
- High production rates
- Excellent repeatability
- Low scrap rates
Extrusion
Extrusion is a process where plastic pellets are melted in an extruder and forced through a mold to create a continuous profile in the desired shape, and then cut to the desired size. It’s commonly used to produce pipes, sheets, and profiles.
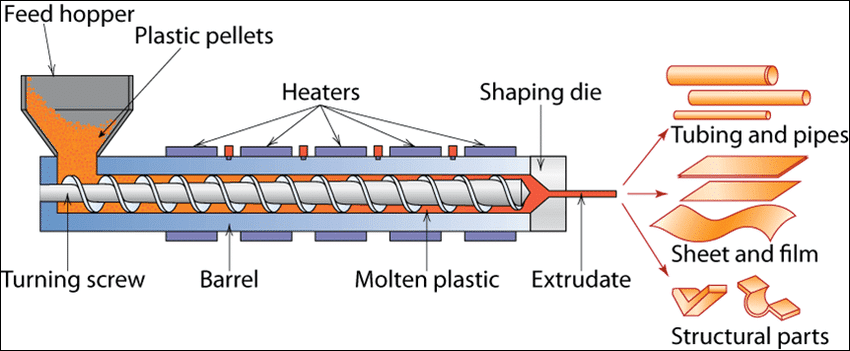
Advantages of Extrusion:
- High production efficiency
- Low cost
- Ability to produce long, continuous shapes
- Good dimensional stability
Thermoforming
Thermoforming is a process where flat thermoplastic sheets are heated to a softened state and then molded into various shapes. The heated sheet is clamped onto a frame and, using mechanical pressure or a vacuum chamber, is pressed against a mold to take its shape. After cooling, the plastic retains the mold’s shape. Thermoforming is commonly used for products like packaging, automotive parts, and medical trays.
Advantages of Thermoforming:
- Ideal for low to medium production volumes
- Low tool and setup costs
- Fast production cycle
- Suitable for large parts or shallow shapes
Vacuum Casting
Vacuum casting, also known as urethane casting, involves creating a silicone mold from a master part under a vacuum. Urethane and other materials are then cast into the silicone mold to produce an exact replica of the master part. This process is ideal for producing plastic prototypes and small batches of plastic parts.
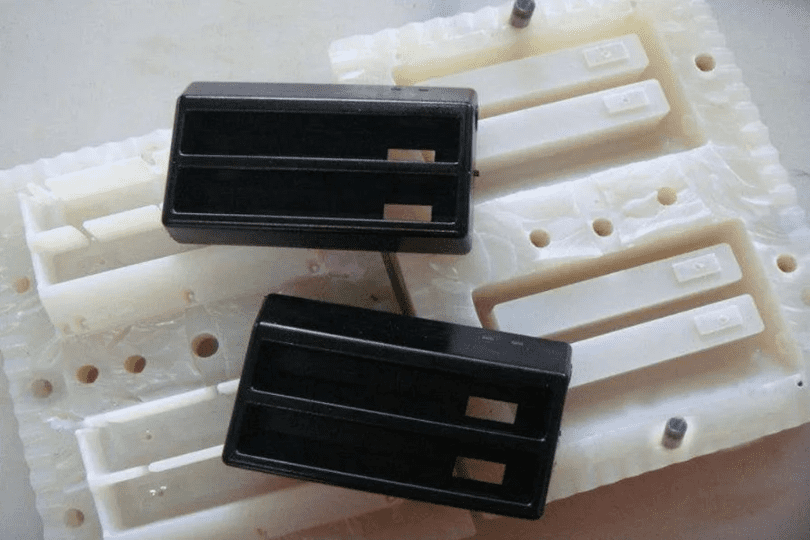
Advantages of Vacuum Casting:
- Ideal for prototyping and small production runs
- Quick turnaround time
- High accuracy and detail
- Low tooling costs
CNC machining
CNC machining is a subtractive process that uses computer-controlled tools to remove material from a plastic block, shaping it into a high-precision part. This process is commonly used for creating plastic prototypes before moving to mass production, such as injection molding.
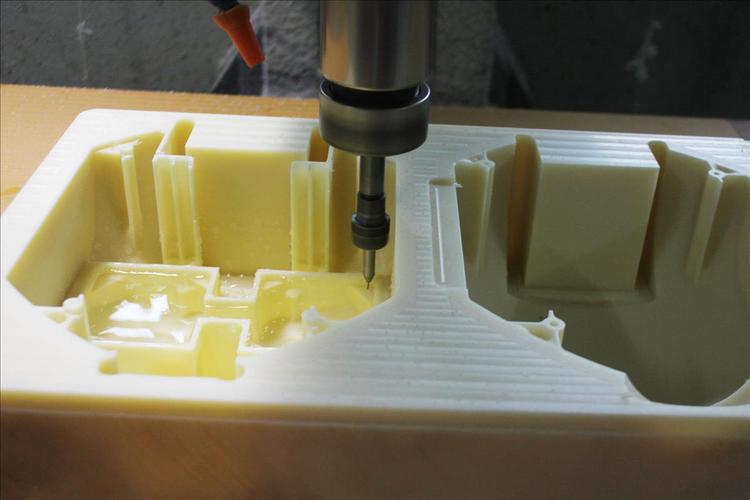
Advantages of CNC Machining:
- No need for molds or tooling
- High precision and accuracy
- Suitable for complex geometries
- Ideal for prototype and small batch production
3D Printing
3D printing is an additive manufacturing process that builds plastic parts layer by layer using plastic powders or liquid resin. Guided by a digital model, this method is ideal for prototyping and low-volume manufacturing due to its rapid lead time and cost-effectiveness.
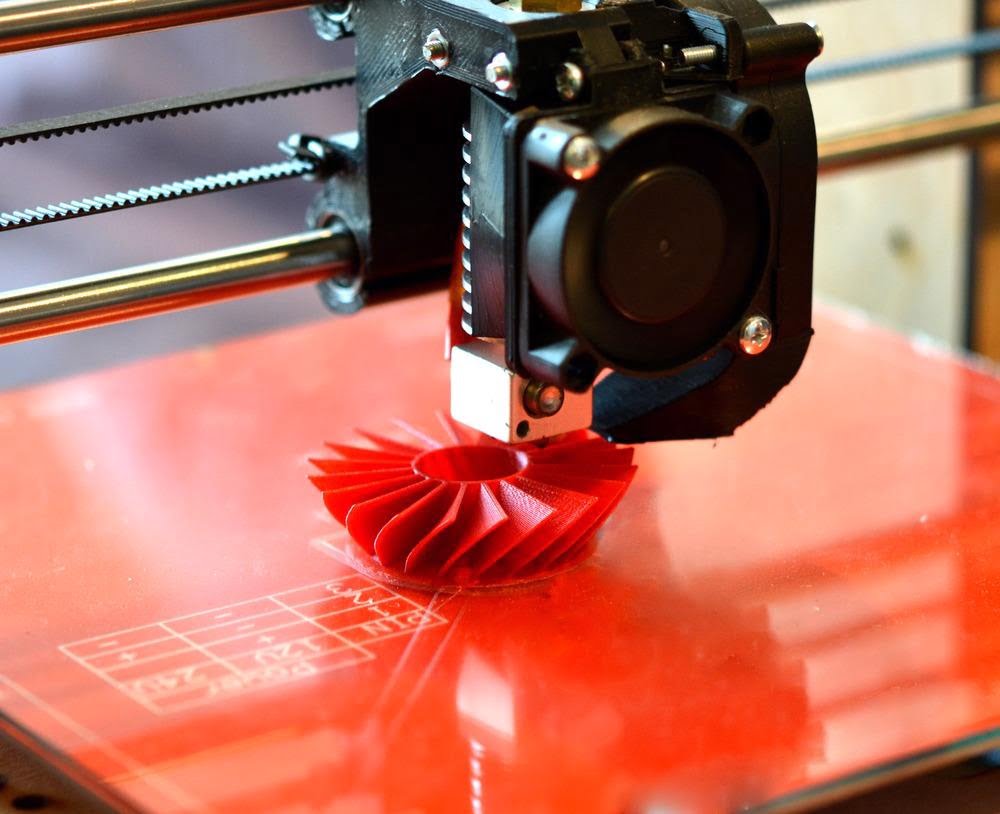
Advantages of 3D Printing:
- Ability to create complex and customized shapes
- No tooling or molds required
- Fast prototyping and design iteration
- Cost-effective for small production runs
Blow Molding
Blow molding, also known as hollow blow molding, involves extruding molten thermoplastic material into a mold and then blowing air to expand the material, causing it to form the shape of the mold cavity. Once cooled, the material solidifies into the desired product shape. This process is mainly used for manufacturing packaging containers, bottles, and other hollow products.
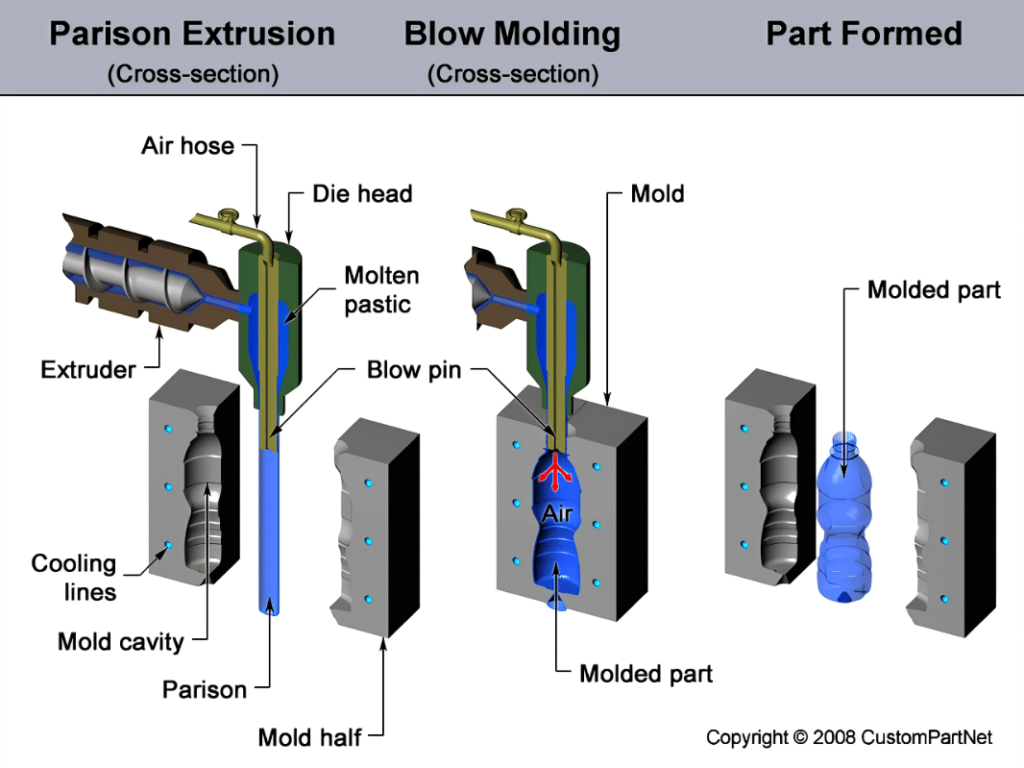
Advantages of Blow Molding:
- Ideal for hollow products like bottles and containers
- Cost-effective for high-volume production
- High production speed
- Low material waste
Compression Molding
Compression molding is a primary process for molding thermoset plastics. In this process, raw materials are placed into a heated mold, where pressure and heat cause the materials to melt, flow, and evenly fill the mold cavity. After a set time under heat and pressure, the materials solidify and take the shape of the mold. This process is commonly used for creating automotive parts, electrical components, and appliance housings.
Advantages of Compression Molding:
- Suitable for high-strength and durable components
- Ideal for thermoset plastics
- Can produce large, complex parts
- Low material waste
Rolling Forming
Rolling forming is a process where molten thermoplastic material passes through a gap between two or more counter-rotating rollers. As the plastic is extruded, the rollers stretch it into a continuous sheet. This process is commonly used in the production of plastic films, sheets, and other thin, flexible products.
Advantages of Rolling Forming:
- Low material waste
- High production efficiency
- Produces consistent sheet thickness
- Ideal for large-volume production of thin plastic sheets
Rotational Molding
Rotational molding is a process where plastic particles are loaded into a mold, which is then rotated while heated. The rotating mold causes the plastic to melt and evenly coat the interior surface, forming the desired shape. This process is commonly used for producing large, hollow plastic items like chairs, flower pots, and tanks.
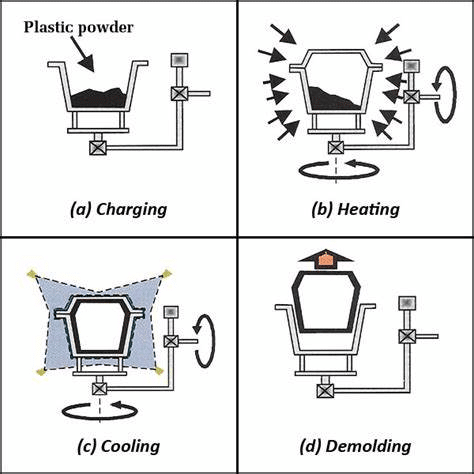
Advantages of Rotational Molding:
- Ideal for low to medium production volumes
- Can create complex, seamless shapes
- Low-cost manufacturing process
- Suitable for producing large, hollow parts
Guide to Choose the Right Plastic Manufacturing Process
There are many factors to consider when choosing the right plastic manufacturing process for your part manufacturing project. Here, we discuss some major factors for detailed consideration.
Part Geometry
Part Geometry is the first factor to be considered when you choose the plastic manufacturing process, this is because some processes are used for solid geometry and some processes only work for hollow parts. Even if it is a solid geometry part design, complexity, and undercut will also affect the choice. for example, some undercuts such as interior geometry can not be molded with a molding process, then you can choose 3D printing. if you are going to make sheets or tubes, then extrusion will be your first consideration.
Precision
Precision is another factor that affects the choice of plastic manufacturing process due to different processes creating different levels of precision products. for example, injection molding and CNC machining are the best processes to create high-precision parts that can achieve 0.01mm tolerance. if you need high-precision parts, then injection molding and CNC machining will be your first choice.
Production Volume
Production Volume can largely determine the process you are going to choose. for example, 3D printing and CNC machining are ideal for low-volume manufacturing of plastic, and vacuum casting is ideal for mid-volume productions. For high-volume parts manufacturing, injection molding, thermoforming, and extrusion will be the best choices in terms of the cost of each piece.
Materials
thermoplastics and thermosetting plastics are used for different plastic manufacturing processes. you need to consider the final function to determine the materials, and after that choose the right manufacturing process for the material you choose. For example, compression or transfer molding is ideal for creating parts with thermosetting polymers, which harden permanently following an initial heat form.
if you need exactly engineering plastic parts, then 3D printing and vacuum casting will not be a good option due to they are using plastic resins. you may consider low-volume injection molding or high-volume injection molding.
Cost
Cost is one of the major factors to be considered in all projects. it can influence the choice of the manufacturing process heavily. for prototype projects, 3D printing, CNC machining, and vacuum casting will be cost-effective choices. For mass production, if possible, thermoforming will be a more cost-effective choice than injection molding.
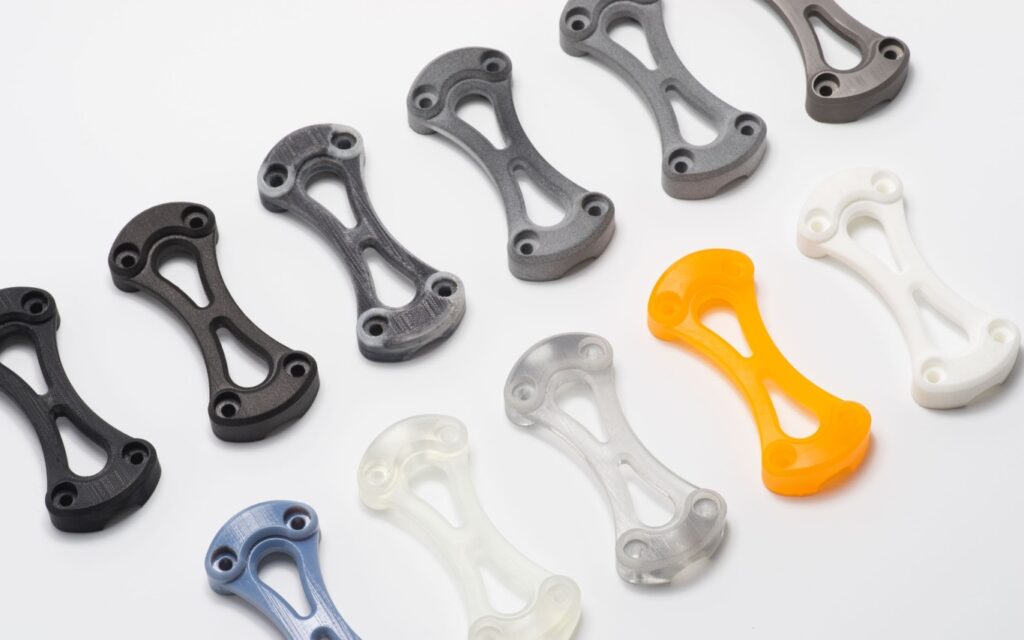
How To Control Quality in Plastics Manufacturing?
Quality control is essential to ensure plastic products are made consistently and meet the required standards. It involves testing and checking parts during and after production. Here are the main steps in the process:
Material Testing
Before making parts, raw materials are tested to check their properties like color, thickness, and melting point. This helps ensure the materials are compliance with the design and suitable for making high-quality products.
Statistical Process Control (SPC)
Before starting production, it’s important to define SPC (Statistical Process Control). SPC is used to monitor the manufacturing process by collecting data and looking for patterns or problems. By analyzing this data, it helps keep the production process consistent and reduces the number of defective parts.
In-Line Inspection
During production, it is important to have in-line inspection systems to check parts as they are made. These systems use cameras or lasers to measure the parts, check for defects, and reject any parts that don’t meet the standards. Once a problem is detected, engineers can fix it quickly to avoid producing large numbers of defective parts.
Dimension Inspection
Once the part is finished, it’s time to check its size and shape. For basic measurements, tools like calipers and gauges work well, but they can be slow for checking many dimensions. Vision systems, which use cameras and software, can quickly scan the part and spot any differences from the required specs. Many companies also use Coordinate Measuring Machines (CMMs), which use lasers or probes to measure key dimensions and compare them to the original 3D design to ensure accuracy.
Visual check
Sometimes, a visual check is needed for features that are difficult to test with tools. Trained workers inspect the parts to spot any surface problems, such as cracks, discoloration, or defects.
Documentation
last but not least, Documentation is important in quality control. It keeps records of test results, operator instructions, and other important details for review and tracking purposes.
Conclusion
In conclusion, each plastic manufacturing processes has its own advantages and limitations, with applications that depend on the specific properties of the plastic product being produced. Kusla, specializing in low-volume manufacturing services, can help you achieve high-quality results for your unique production needs.
FAQ
What is the most common plastic part manufacturing process?
For solid parts, injection molding is the most common plastic manufacturing process. It is widely used for producing a variety of parts, ranging from small components to large items. For hollow parts, blow molding is the most common process used in mass production, particularly for making containers, bottles, and other hollow plastic products.
What are the raw materials for manufacturing plastic?
The raw materials for making plastic include cellulose, coal, natural gas, salt, and crude oil. Crude oil is a major source of petroleum-based plastics, while natural gas is used for producing plastics like polyethylene and polypropylene. Cellulose, derived from plants, is used for creating biodegradable plastics, and coal is used in some specialized plastic production processes. Salt is often involved in the production of certain plastics, such as PVC (polyvinyl chloride).