Metals are commonly used materials in rapid prototyping because they offers a wide range of benefits. It’s versatile, durable, and suitable for many industries. Creating a functional metal prototype is essential for ensuring the final product works as intended. That’s why understanding the different methods for making metal prototypes is important.
In this article, we’ll explore the different methods to create metal prototypes, explain the benefits of each method, and help you decide which one is best for your specific project needs.
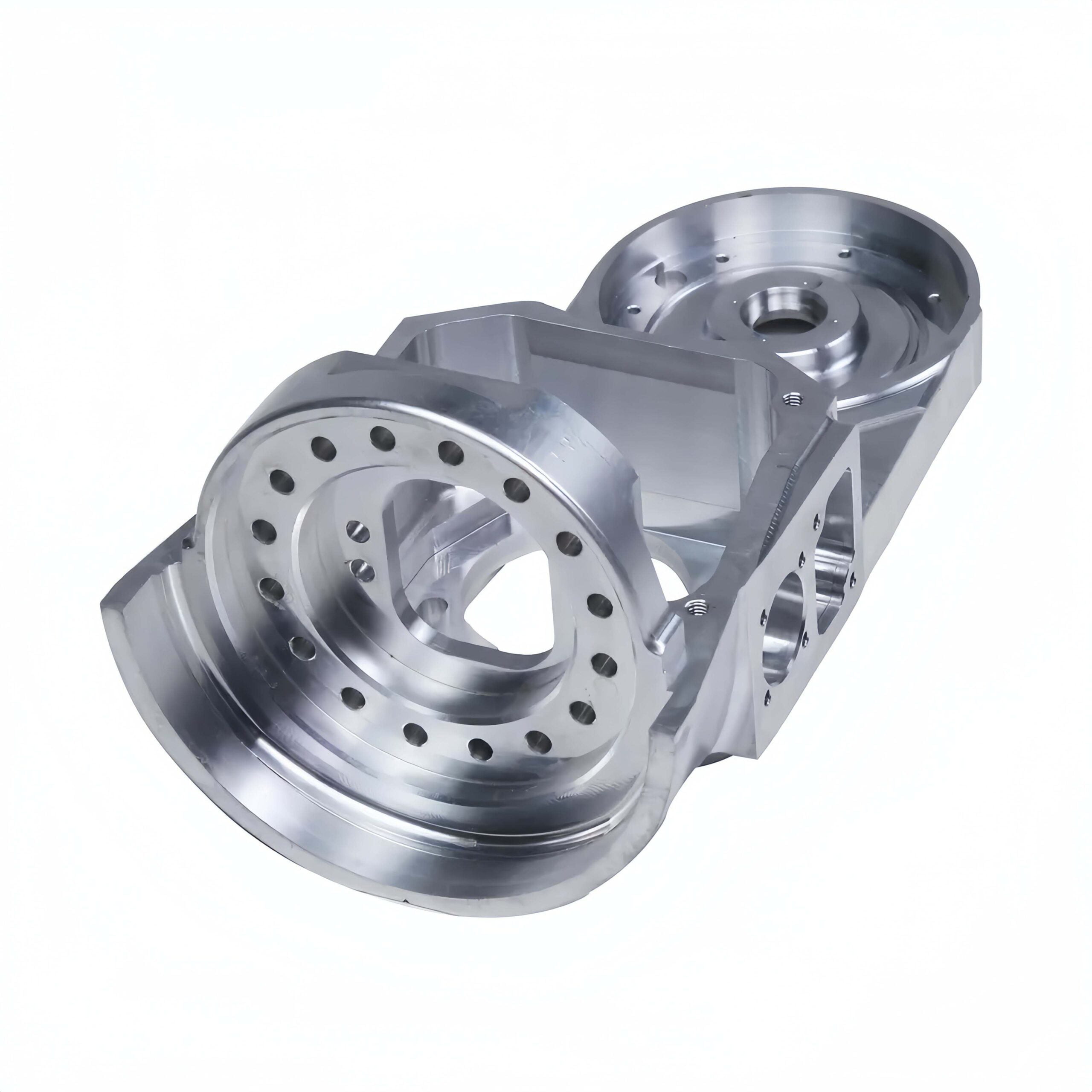
What Is A Metal Prototype?
A metal prototype is an early model of a metal product created using techniques like CNC machining, 3D printing, casting, extrusion, or sheet metal forming that can shape the metal material. Metal Prototypes are made before full production to allow designers to test and improve the design. Common metals used for these prototypes include aluminum, steel, Titanium, and Copper.
Benefits of metal prototypes over plastic
When deciding to make a rapid prototype, another question often comes up: should you go with metal prototypes or plastic prototypes? Metal prototypes have some clear advantages over plastic. Here’s why:
High Strength
Metals are much stronger and durable than plastics. If your design needs to handle tough conditions like high heat or heavy loads, metal is a better choice since most plastics aren’t as tough.
Cost-Effective
While plastic might seem cheaper, it wears out faster and may need more frequent replacements. Metal parts, on the other hand, are sturdier and often last longer, making them more cost-effective over time.
Metallic Surface Finish
For a sleek, metallic look, metal is the way to go. Metal prototypes can be anodized for a corrosion-resistant finish, while plastic can only be painted, giving metal an advantage in both appearance and durability.
Accuracy:
Metals can be precisely shaped and machined to tighter tolerance than plastics, which makes them ideal for applications that require high precision. CNC machining allows metal prototypes to be created with exceptional accuracy, ensuring they give the best function performance. for example, the optic reflector prototype in Automotive lighting, usually make in aluminum material to have the best optic test result.
Methods for making metal prototypes
There are several ways to make metal prototypes such as CNC machining, 3D printing, sheet metal fabrication, casting, and extrusion. Choosing the right method ensures strong, functional prototypes while saving both time and money. let us explore how each method works and their key benefits:
CNC machining
Custom CNC machining uses computer-controlled machines to make metal prototypes by cutting away material from solid metal blocks. CNC machines with 3, 4, or 5 axes can handle complex shapes and tight tolerances. You can easily change digital designs, making it simple to produce multiple copies.
Key Benefits of CNC Machining:
- flexible for small batches.
- High accuracy
- Fast and efficient production
- Wide choice of materials
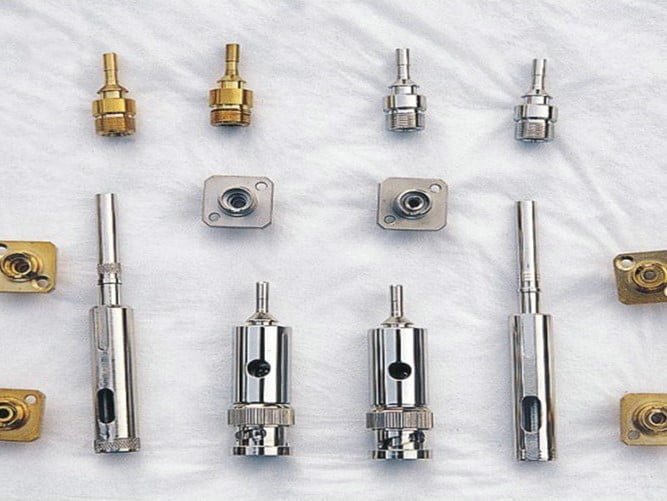
Metal 3D printing
3D printing is an affordable method for creating metal prototypes, though it may not offer the same level of accuracy as traditional techniques. The process works by using a laser to melt thin layers of metal powder, and then welded together to form the desired part. 3D printing is ideal for creating complex metal prototypes quickly, making it a great option for projects that require fast turnaround times.
Common metal 3D printing technologies include Selective Laser Melting (SLM) and Direct Metal Laser Sintering (DMLS). These methods can produce metal prototypes in just a few hours, making them perfect for rapid prototyping needs.
Key Benefits of Metal 3D Printing:
- Fast lead time
- low cost
- Suitable for complex geometry
Sheet Metal Fabrication
Sheet metal fabrication is another way to make metal prototypes. For sheet metal prototyping, thin sheets of metal are placed on a table, and a laser cutter creates patterns based on a computer design. Then, different processes like bending, punching, spinning, and welding shape the metal sheets into the right form. Sheet metal Fabrication are great for making enclosures, casings, and frames.
Key Benefits of Sheet metal fabrication:
- high precision parts
- Custom-built designs
- Cost-effective
Metal Casting
Metal Casting involves pouring hot liquid metal into a mold with a hollow space to form the desired shape. Once the metal cools and hardens, it takes on the final form of the prototype. Casting is an efficient method, especially for creating complex shapes, but it’s often avoided for prototypes due to the need for special equipment and a custom mold.
However, despite its higher initial cost, casting can be a good option for small production runs. By reusing the molds for multiple parts, manufacturers can save money in the long run.
Key Benefits of Metal Casting:
- Produces very strong parts
- High production quality
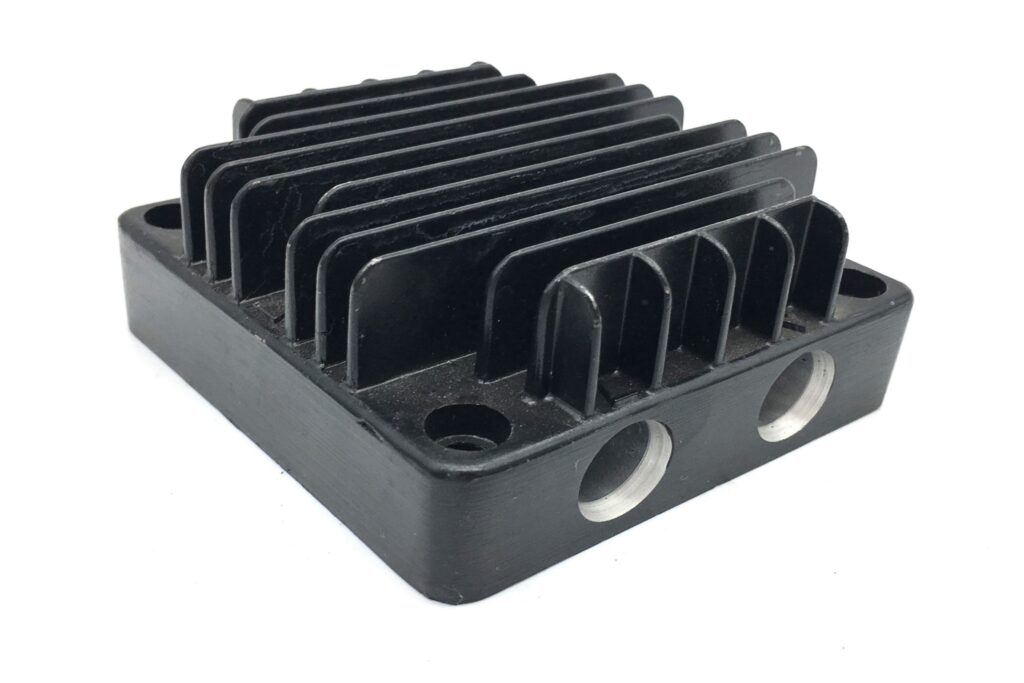
Metal Extrusion
Metal extrusion creates metal profile prototypes by forcing material through a shaped opening in a die, creating long parts part with a uniform cross-section. then the parts are cut to the right lengths. Metal extrusion is typically used for mass production, However, aluminum extrusion can still be useful for prototyping, especially for simpler parts like joints, brackets, and metal bars.
Key Benefits of Metal Extrusion:
- High precision
- Special profile design
- Suitable for high-performance use
- production quality
Common Metal Materials Used for Metal prototypes
The most common metal mateirals used in rapid prototyping include aluminum, steel, titanium, and copper. The choice of metal material is crucial to achieving the desired balance of strength, weight, durability, and cost for metal prototypes. Here’s the breakdown of these materials to check:
Aluminum
Aluminum is one of the most popular metals for prototyping, this is because It is lightweight, easy to shape, and resistant to rust and corrosion. Aluminum also conducts heat and electricity well, which makes it a good choice for electrical parts or parts that get hot. and It can be treated with anodizing to make it even more durable and give it a nice finish. Aluminum is a great option for prototypes that need strength without being too heavy.
Steel
Steel is another commonly used metal, especially for prototypes that need to be strong and durable. While steel is heavier than aluminum, it is tough and resistant to wear and tear. Steel can handle high stress and harsh conditions, making it a good choice for parts that need to last or support heavy loads.
Titanium
Titanium is very strong and resistant to corrosion, which makes it ideal for tough environments, like in aerospace or medical devices. It can withstand high temperatures, but it does not conduct heat or electricity as well as other metals. It is also more expensive and harder to work with, so it is typically used only for specialized prototypes.
Copper
Copper is used for prototypes that need excellent electrical conductivity, such as wires or electrical connectors. It’s easy to work with but softer than other metals, so it may not be the best choice for parts that need to be very strong or resistant to wear.
Other Metals
Other metals, such as chrome alloys, may be used when specific properties like hardness or resistance to wear are needed. Chrome alloys are very durable and maintain their appearance even in tough conditions.
Key Considerations For Metal Rapid Prototyping
Before starting your metal prototyping project, there are several factors to consider. These factors will affect how the metal prototype is made, as well as the cost and time required. let us explore these factors below, then you can think about them for your own project.
Part Complexity
The design and features of your prototype will influence the best method for making it. For example, metal 3D printing is great for creating complex shapes and intricate details, while the other methods need to take huge cost for that. Anyway, the more complex the part, the higher the cost may be, so keep that in mind when deciding on the method.
Precision
Think about how precise the prototype needs to be. If your prototype requires very fine details or tight tolerances, CNC machining is a good choice. On the other hand, if precision is not as critical, 3D printing can be a faster and more affordable option.
Material
Prototype material sometimes is not the same as the final product, this depends on the purpose of your requirement, if the purpose of the metal prototype is to have a function test that could be impacted by the material, then you need to use the same metal materials as the final product. if not for function test and just for visual check, you can use the materials more easy to machine, such as Aluminum.
Surface finish
Different prototyping methods can produce different surface finishes. For example, metal 3D printing tends to leave a rougher surface, while CNC machining typically results in a smoother finish. Consider what kind of surface finish you need for your prototype.
Volume
The volume of the metal prototype is also important to be considered before starting. this is because Some methods are best suited to few numbers, but some work for higher volumes. for example, methods like 3D printing, are great for small numbers of prototypes, while others, like casting, are better suited for larger production runs.
Cost budget
Some metal prototyping methods such as casting and extrusion may have high initial costs for making toolings, if you do not have enough cost budget, you may only use CNC machining or 3D printing and reduce the volume to cover the cost budget.
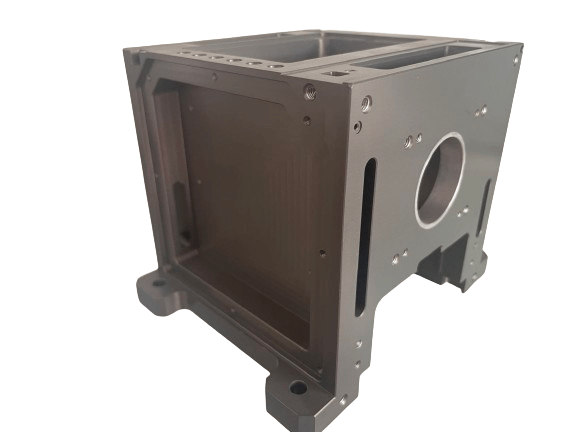
Conclusion
Metal prototypes can help you to test and refine your ideas before full production. they helps save both time and money by identifying potential problems early on. Understanding the different methods for making metal prototypes can make your development process more efficient.
However, to ensure high-quality metal prototypes, it’s important to work with a professional rapid prototyping factory. With advanced equipment and a skilled team, KUSLA is always ready to support you with your projects and help bring your ideas to life.
FAQ
What is the lead time to create a metal prototype?
Generally, it takes less than 5 days to create a metal prototype with CNC machining, 3D metal printing, and sheet metal prototyping. For casting metal prototypes, it will take less than 10 days to make.
How much does a metal prototype cost?
the metal prototype cost depends on the materials and prototyping methods. Generally, one simple metal prototype will take $50 to $1000 to make.