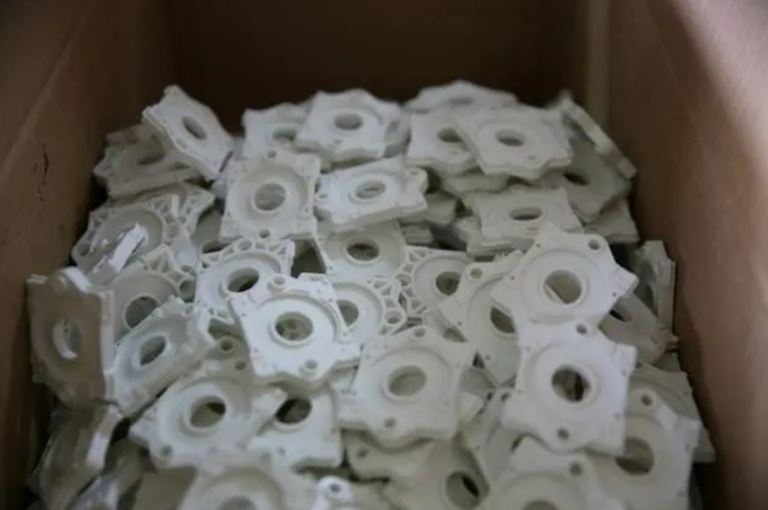

Prototype Injection Molding Service
Prototype injection molding helps you create production quality parts which can be used for testing part geometry, functionality and low-volume production. Get your injection molded prototypes with KUSLA in as few as 10 business days.
ISO 9001:2015 certified factory
T1 samples as fast as 2 weeks
From 1 to 10,000 units