In precision manufacturing, the SPDT single-point diamond turning process is a key technology for the manufacture of ultra-fine components used in many industries, including optics, aerospace, medical devices, and defense. Due to its exceptional precision and surface quality, this technique is crucial for producing high-performance parts required by advanced industries.
Materials can be created with great precision by using the diamond turning tool as a cutting tool with diamond tips. Natural or synthetic diamond tool bits are used in mechanical machining on lathes or other machine tools like turn-mills and rotary transfers. While the SPDT is a common name for diamond plating, the term “single-point” can be misleading. Different tool configurations, such as radiused tips or specially contoured forms, can be achieved for specific tasks in practice.

The diamond turning process is particularly adept at producing top-notch aspheric optical components from substances such as metals, crystals, and acrylics. This material facilitates the creation of mold inserts for plastic optics, which are then used to produce optical parts with great accuracy in mass production. Various applications use these diamond-turned optical elements, including telescopes, video projectors and missile guidance systems, laser devices, or scientific research instruments.
Most of the current SPDT operations are performed on advanced instruments such as Computer Numerical Control (CNC) machines. These CNC machines provide the necessary accuracy and repeatability to achieve ultra-high precision in the process. Apart from turning, diamonds have a bearing in other machining techniques such as milling and grinding; they also provide uniform performance across these applications.
Diamond turning is particularly advantageous due to its exceptional surface smoothness and brightness. In contrast to conventional machining methods, the finished components are often made in mirror-like condition, with no further buffing or polishing required.
The single-point diamond turning process is a game-changer for how precisely high-quality optical components are made within the captivating domain of precision machining. It has also revolutionized the production of high-quality optics and prototypes. With the aid of a diamond-tipped cutting instrument, this technique provides extremely smooth finishes on varying materials, making it essential in industries that demand high levels of precision and superior surface quality.
Explore the features and functionalities of the SPDT method and the technology that enables its implementation, and explore the potential of this approach to advanced manufacturing. We’ll explore the reasons why this approach has become the gold standard for producing high-quality, precision components. This article provides a comprehensive overview of SPDT, including its functioning, examples, and the significance of this technology in contemporary manufacturing.
The Single Point Diamond Turning Process: What Is It?
The fundamental concept of the single-point diamond turning process, “SPDT,” must be comprehended before we can understand its functioning. In the single points of machining, to create a shape for an element, which is typically made from non-ferrous materials like copper, aluminum, or polymers (also known as the “single point”), essentially any natural diamond cutting tool is used to produce the component. Cutting the material with a diamond tool produces surfaces in sub-micron dimensions that are smooth at the nanoscale.
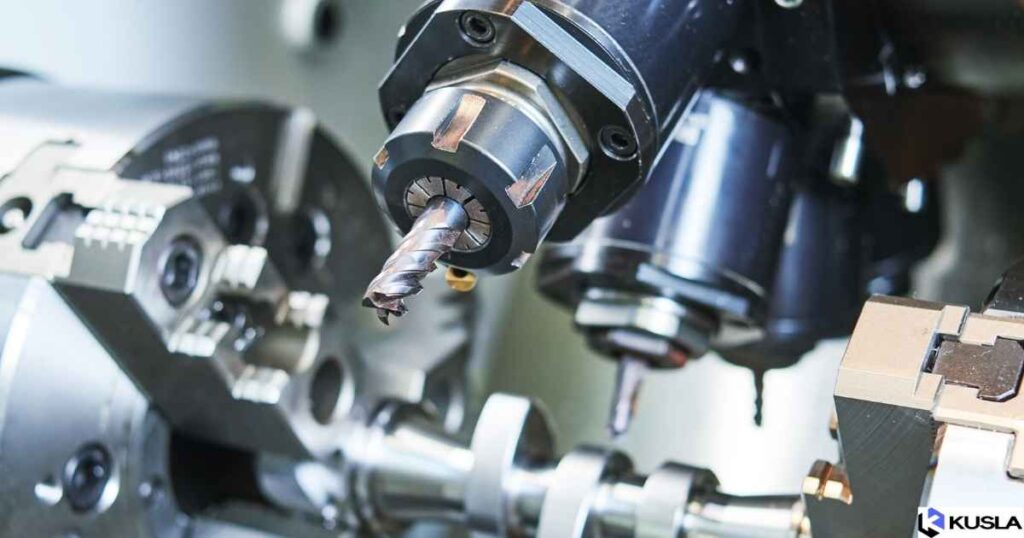
Precision optics and intricate geometry machining are the primary outcomes of this technique, which cannot be achieved through traditional methods. SPDT can produce free-form surfaces and fine details for applications such as telescope mirrors and aspheric lenses.
How the Single Point Diamond Turning Process Works
The single-point diamond turning process is utilized to produce the desired shape. Here, we will examine the process step by step in detail.
1. Setup Preparation
Here, we will discuss how the single-point diamond turning process has established its first setup. The machine and workpiece object is an important stage that is utilized to supply and shape the desired form. Dedicated diamond turning machines with extremely stiff frames are utilized to ensure accuracy and minimize vibrations. Also, the machine’s temperature is managed to prevent thermal growth from affecting its accuracy. Deciding the workpiece material consisting of non-ferrous metals, polymers, or a few crystalline materials is typically used because of their malleability and responsiveness in diamond reduction. SPDT calls for unique system calibration. A small misalignment can cause parts to end up defective, necessitating the machine’s calibration to the nanoscale stage. Considering its required geometry and surface end, which diamond device is the most pleasant and acceptable for the slicing-edge activity?
2. The Process of Machining
The machining method can start as soon as the setup is prepared. Tool route programming is critical first. The diamond tool’s movement is accurately controlled by CNC programming. The device’s path is described by using sophisticated algorithms that ensure the preferred form and brilliant surface are satisfactory. The diamond tool gradually removes material layer by layer as it passes over the workpiece in a single-point movement all through the reducing or cutting process. By applying minimum heat and stress to the workpiece, this approach facilitates holding the quality of the material object and guarantees superior dimensional accuracy. Additionally, to prolong or extend the tool’s life and improve the surface finish polish, a unique coolant or lubricant is often utilized. Additionally, using coolant lowers the possibility of heat deformation, preserving the workpiece’s integrity.
3. Tracking Monitoring and Modification
SPDT needs real-time monitoring systems to detect errors or deviations. Advanced sensors and feedback mechanisms are utilized to maintain the process’s momentum. Engineers can make slight modifications during the process to ensure that the quality of the work is maintained to the fullest extent possible.
Essential Tools and Types of Equipment for Turning Single Point Diamonds
Highly specialized and complex equipment is wanted for the single-point diamond turning process. The essential tools are furnished below.
1. Machine for Diamond Turning
The highest stage of precision is used to create that system and machines. They regularly use air bearings for frictionless motion and have granite bases for stability. For best consequences, sub-micron accuracy is used to control the spindle and tool slide movements.
2. Tools for Diamond Cutting
The center of the SPDT process is the diamond tool. Its slicing quality and fine, cutting-edge facets are shaped to offer top-notch surface quality via interaction with the workpiece. Diamonds are chosen because of their toughness, which allows them to reduce with little wear.
3. Equipment for Metrology
Following machining, components are tested with state-of-the-art metrology devices, including profilometers and interferometers. These units can check the final product’s exceptional universality, profile correctness, and floor surface roughness.
Making and Application of Single-Point Diamond Turning in Different Sectors of Industries
There are many industry sectors, like high-tech fields, manufacturing industries, and finishing and molding industries, and different technology departments consider the single-point diamond-turning process approaches to be of great significance. The primary applications in these sectors consist of the following:
1. Manufacturing of Optics
Because of this, the accuracy of SPDT makes it perfect for making lenses, mirrors, and optical molds. This method is critical to industries that need perfect optics, which includes telescopic structures and digital camera lenses, to achieve the best.
2. Parts of Aerospace
SPDT is capable of offering and delivering the tremendous accuracy required for high-overall-performance aerospace components and parts. This process is normally used to make parts such as missile steerage structures and gyroscope housings.
3. Health Care Equipment
The technique is used to produce accurate surgical instruments and diagnostic devices. For instance, laser-based clinical approaches require extraordinarily specific surfaces.
4. Military and Defense Uses
The SPDT process is used in the defense industry to supply parts like sensors and focuses on structures requiring excessive accuracy and dependability.
Advantages of the Single-point diamond Turning Process
One advantage of the single-point diamond turning process is its remarkable accuracy and precision.
1. Unmatched Accuracy
SPDT furnishes unmatched accuracy, with tolerances as small as some nanometers. This degree of accuracy is vital in superior packages like optics.
2. Superior Surface Quality
SPDT-produced additives often have surface qualities that are reflect-like, obviating the need for similarly sprucing. In the manufacturing manner, this saves money and time.
3. Adaptability
Because of the manner’s versatility, intricate shapes, freeform surfaces, and micro-dependent elements can be machined. Additionally, it can be implemented in multiple ranges of materials.
4. Economical for Prototypes
SPDT is affordable and cost-effective for developing high-precision prototypes, although it is typically pricey because of the specialized gadgets needed. For short testing and prototyping, producers can depend on single-point diamond-turning services and offers.
Challenges and Difficulties with the Single Point Diamond Turning Process
Although SPDT is a powerful era, it has challenges and drawbacks of its own.
1. Material Restrictions
The approach works well with softer, non-ferrous materials. The type of materials that may be employed is confined by the diamond tool’s vulnerability to harm from more difficult metals and alloys.
2. The Rate and Intricacy
Diamond tools and SPDT machines are costly. Furthermore, the requirement for genuine environmental control raises the setup’s average cost and complexity.
3. Wear of Tools
Despite being the hardest recognized material, diamonds are at risk of being put on, specifically while reducing tough materials. To achieve excellent results, frequent device inspections and replacements can be necessary.
The Future of Single Point Diamond Turning Changes
Technological advances are increasing opportunities for SPDT. Better diamond tools, advanced CNC systems, and hybrid machining processes—which combine SPDT with other processes for versatility—are examples of emerging successes. Advances in metrology that enable the delivery of real-time micromanipulation capabilities make the process even more reliable. Turn to a road.
Conclusion
Manufacturing continues to be revolutionized with the aid of the single-point diamond turning services process approach, which makes it viable to create components with an amazing stage of precision. SPDT stands out as an essential technology for producing complicated optics, excessive-overall-performance aerospace additives, and rapid manufacturing for prototypes. It is predicted that this technique’s uses and benefits will boom even more as tendencies continue to enhance and refine it, influencing production as we know it now.