Silicone molds are popular for their great flexibility. They are used by professionals, DIY enthusiasts, and even home cooks. From creating high-quality prototypes with vacuum casting to making small batches of wax for jewelry, and even for baking and candy-making at home, silicone molds are versatile. This article explains how to make a silicone mold in a simple way, covering its uses and benefits for both professionals and hobbyists.
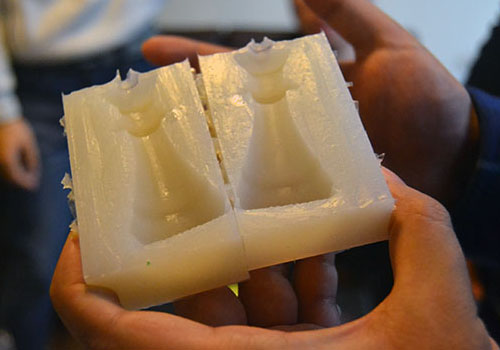
What is silicone mold?
Molds are typically made from metals like steel and aluminum. However, soft silicone can also be used to make molds. Silicone is a type of polymer made from siloxane and is commonly used to create flexible items such as protective casings, gaskets, and seals.
A silicone mold is a type of mold made from silicone material, used to create copies or replicas of an original object, known as the “master pattern”. Liquid materials, such as resin or other casting substances, are poured into the silicone mold and left to harden, forming parts as the shape of the mold’s cavity.
Silicone molds can be used for a wide range of applications, including making plastic parts, jewelry, or even food items like chocolates or cakes. Due to silicone’s soft, flexible nature, these molds are easy to create and can be bent or stretched without breaking. However, their flexibility also means they are less durable compared to metal molds, which are stronger but less flexible.
Advantages of silicone molds
Silicon molds have several benefits when you use it for create parts, here we conclude Some of the benefits of silicone molds as follows:
Versatility
Silicone materials have different grades for making molds to cast different products. Some grades can be used for urethane casting plastic parts, some grades can be used for casting wax, and Food-grade silicone can be used for chocolate. This versatility allows for innovation and creativity in product development.
Flexibility
Silicone is soft and flexible like rubber. the molds made of silicone carry on flexibility which means it can be made easily for any shape. and when you remove the parts from the silicone mold, it will not damage your part even if there are undercuts.
Stability
Silicone can withstand both cold and high temperatures from -60° to 250° degrees Celsius, this makes silicone mold stable when you put it into an oven or freezer to create objects such as cookies.
Durability
A silicone mold can be used not only once time but several times for casting products before it degrades. this is because silicone mold can withstand the pressure during casting for a certain time. the lifetime of silicone mold can vary based on the application it is used for, for homemade silicone mold for chocolate, it can be used for a long time with proper maintenance.
Low Cost
Silicone material is cheap and easy to get from the market, Silicone mold is also easy to make at a low cost, which makes it affordable for all the people who want to use it.
Types of silicone mold
Depending on the parts you need to create, there are two types of silicone molds you can make. These two types have differences in how they are made, so before you begin, it’s important to decide which one you need. Let’s take a look at the options:
One-Piece silicone mold
One-piece Silicone mold work for those parts has one flat side, and only one side needs to be shaped by the silicone mold. works like a tray, you only need to fill the material into the cavity and then let the material cure at a certain environment. It is commonly used for home-making cookies and chocolates, and also for DIY makers to make some craft which has one flat side.
Two-Piece Silicone Mold
A two-piece silicone mold means mold consists of two parts that form the master pattern shape cavity half and half. it can work for parts without a flat side. the liquid material is poured into the mold and cured, you need to open the mold to take the part out. it is perfect for creating custom-designed 3D parts.
How to make a silicone mold step-by-step
The processes of making a silicone mold are all the same no matter whether you are making silicone molds for DIY products or industry plastic products, the difference is the silicone material, you may need professional tools to handle it when you are working on industry products. here we take an example of marking a two-piece silicone mold at home to explain the process.
Prepare Tools And Materials
- silicone material
- Modeling clay
- Mold release agent
- Cutting blades
Step 1: Purchase or create the master pattern
you can buy the master pattern you want to duplicate directly from the market or you can create a custom master pattern by Sculpting clay, carving wood, or rapid prototyping techniques such as 3D printing or CNC machining. this depends on how accurately you want the replicas from the silicone mold to be.
Step 2: Lay out the master pattern in clay
Put the master pattern on the clay and Embed it into the clay with one-half of the pattern. this is to create one-half of your mold.
Step 3: Create a Mold Frame
Create a Mold Frame with a proper size to contain the Clay with the master pattern on it, You can use smooth materials like wooden boards, acrylic sheets, or building blocks as a mold frame. Apply mold release agent to the frame’s surface to prevent adhesion.
Step 4: Pour silicone
Pour the prepared liquid silicone into the mold frame space until the master pattern is entirely covered. and then let it cure to form one-half of your two-piece mold.

Step 5: Take out the half mold and master
You have to remove the mold frame, take out half of the mold and master, and then clean the side of the master with clay and also the mold.
Step 6: Place the mold and master back in the mold frame
Place the mater pattern into the half mold, then put them together back into the mold frame and face up instead of down. Apply mold release agent again to the frame’s surface.
Step 7: pour silicone again
Put the silicone into the mold frame and let it cure to create the other half of the mold.
Step 8: take out the master pattern
After the other half mold is cured, remove the frames, split the silicone mold with a blade into half and half, and then remove the master pattern. until now, you can get your two-piece silicone mold.
Use of silicone mold
Silicone molds can be used for many different purposes, both in industry and at home. Let’s explore the details of each:
Industry use
Silicone molds are widely used in the vacuum urethane casting process to create plastic parts for various industries. These parts are often used for prototypes or low-volume production, helping to test and validate designs before moving to mass production. In this process, silicone molds are filled with polyurethane resin in a vacuum environment to create copies of the master pattern.
Vacuum casting is ideal for small-batch production and is more cost-effective than injection molding for low quantities. With a CNC-machined master pattern, silicone molds can produce high-resolution parts that are almost same as those made with injection molding.
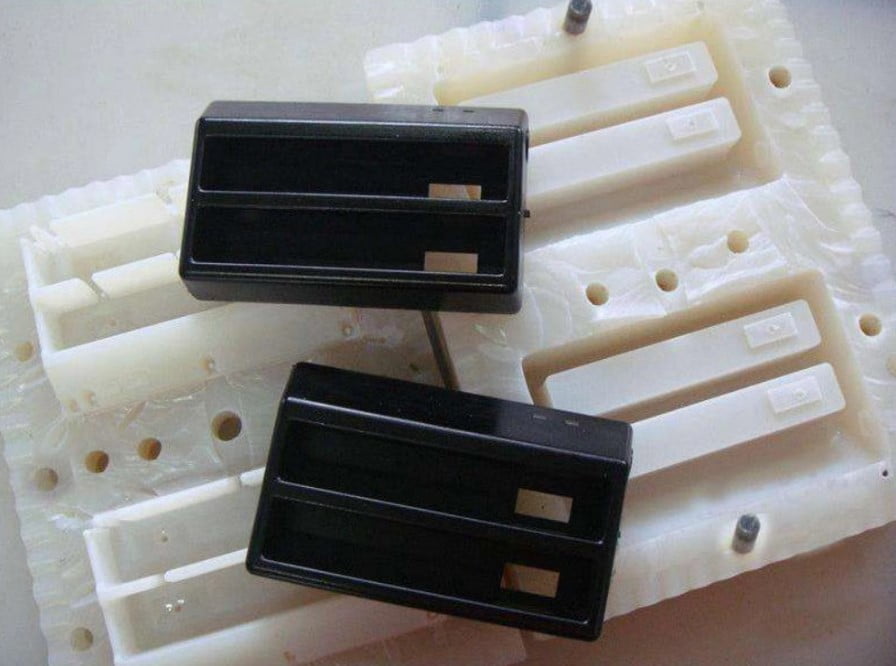
Home use
Silicone for mold making is easy to find, and by following simple instructions, you can create molds for a variety of at-home projects.
Crafting and Decoration: Silicone molds are perfect for making decorative items like artisanal figurines, plastic jewelry, soaps, candles, and more. You can use commercially available casting resins, which are safe for home use when instructions are followed correctly, to create these fun and creative objects.
Food and Drink: Silicone is a kitchen-friendly material that is safe for use in the fridge, freezer, microwave, and oven. This makes it ideal for food-related applications. Silicone molds are commonly used for making popsicles, ice cubes, cookies, cakes, and even decorative chocolates and candies.
Children’s Crafts: Silicone molds are also great for children’s activities. You can use them to make colorful crayons, chalks, erasers, and other fun crafts that kids will enjoy creating.
Conclusion
Understanding the techniques related to silicone mold making is valuable whether you’re creating small DIY projects at home or producing more complex plastic parts. At KUSLA, a leading rapid prototyping factory in China, we specialize in high-quality urethane casting services using silicone molds. Whether you need prototypes or low-volume production, we can help you bring your plastic products to life with precision and efficiency.
FAQ
What kind of silicone can I use for a silicone mold?
A two-part Silicone will be a good choice for you such as Smooth-On OOMOO 30 which is popular. Two parts, A and B, are combined and mixed to create a liquid, pourable molding material.
Can I use normal silicone to make a mold?
Yes, you can use regular silicone caulking to make molds. To improve the consistency and mold-making ability, you can mix it with liquid soap or cornstarch. This helps create a more flexible and workable silicone mold for various projects.