CNC (Computer Numerical Control) machining and 3D printing are two leading technologies for rapid prototyping, but they use completely different methods to make the parts. before you start a rapid prototyping project, you need to understand well the difference between these two methods to choose the right one. In this article, We provides a detailed comparison of CNC machining and 3D printing to help you decide which is better for your rapid prototyping projects.
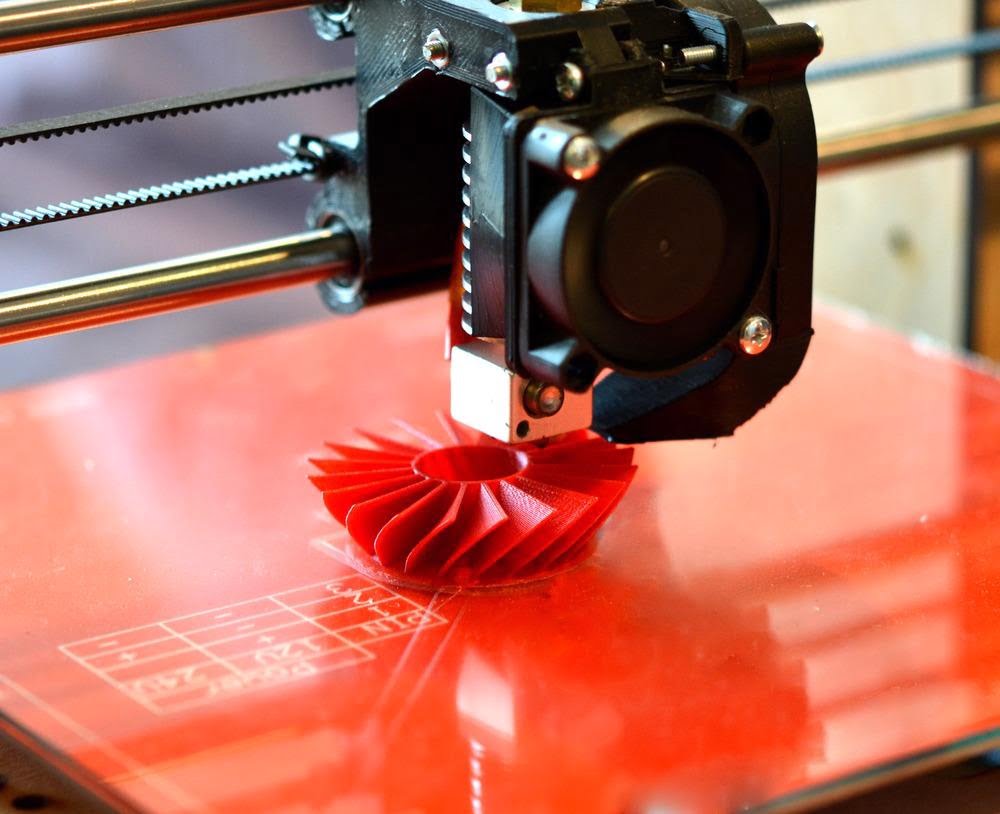
Subtractive vs Additive Manufacturing
The main difference between 3D printing and CNC machining is how they create parts. 3D printing is an additive manufacturing process, while CNC machining is subtractive manufacturing process.
Subtractive Manufacturing
Subtractive manufacturing creates a lot of waste because the removed material is discarded. However, it has the advantage of offering high precision when cutting and shaping parts.
As a Subtractive Manufacturing process, In CNC machining, the process starts with a solid block of material. The rotating cutter removes material from the block to shape the final part. CNC machining is very accurate and works well with many materials, like wood, metal, and plastic.
Additive Manufacturing
Additive manufacturing creates less waste compared to subtractive methods. It also provides more freedom and flexibility in designing and shaping parts.
As a Additive Manufacturing process, In 3D printing, parts are made by adding material layer by layer. Different materials can be used, including plastic filaments (FDM), resins (SLA/DLP), and metal or plastic powders (SLS/DMLS/SLM). A laser or heated extruder is used to harden or melt each layer. 3D printing offers great flexibility in design, quick production, and lower costs.
Advantages of CNC Machining Compared to 3D Printing
CNC machining offers several benefits compared to 3D printing, particularly in material strength, precision, and surface finish. Here’s a closer look at these advantages:
Material Strength
CNC machining works with actual engineering materials like metals and hard plastics, maintaining their full strength and original properties. On the other hand, 3D printing often uses alternative materials that may not be as strong or durable as traditional engineering materials.
Precision
CNC machining is highly precise and can achieve tighter tolerances than 3D printing. This makes it ideal for parts requiring exact measurements and high accuracy.
Surface Finish
CNC machining produces a smooth and uniform surface, and with the right settings, the finish can be very precise. 3D printing can sometimes leave rough surfaces, especially due to the way layers are built up which need additional labor to make the post processing treatment.
Advantages of 3D Printing Compared to CNC Machining
On the other hand, 3D printing also have some key advantages when compare with CNC machining, Let us explore what these advantages are:
Faster Production
3D printing makes parts quickly, while CNC machining needs extra time for setup, programming, and supervision.
Lower Costs
3D printing is usually cheaper for making complex shapes. It needs less setup and fewer steps during production. In many cases, CNC parts can cost up to 10 times more than 3D printed parts.
Ease of Use
3D printers are becoming more user-friendly and don’t require a lot of technical skill to set up or maintain. They are also able to meet most production needs. On the other hand, CNC machining is a more complex process that requires skilled operators and regular updates to their knowledge.
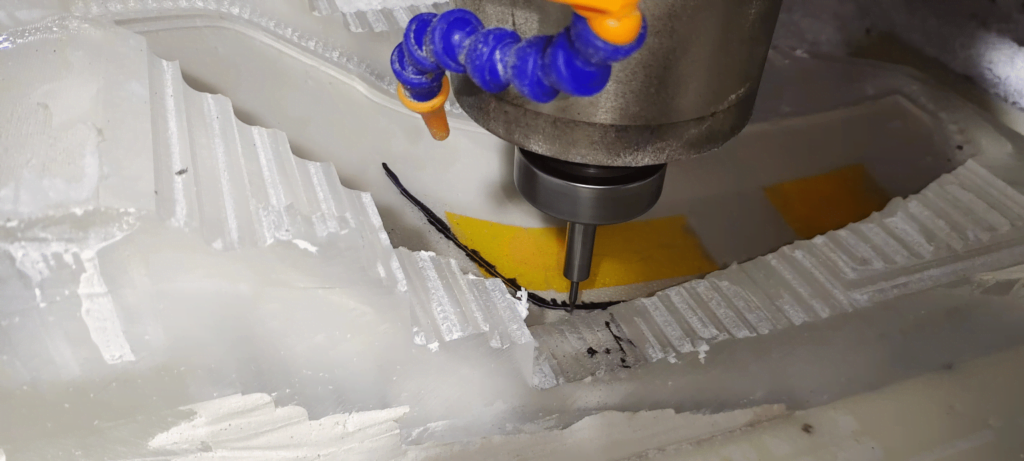
CNC machining vs 3D printing: Key Differences
To understand the differences between CNC machining and 3D printing, let’s compare them across several important aspects to help you undersand clearly:
Materials
Both CNC machining and 3D printing work with a wide variety of materials, including plastics and metals, but the type and application of materials differ between the two methods.
CNC machining uses high-quality engineering materials that retain their full strength and original properties. Common plastics used in CNC machining include ABS, Nylon (PA66), Polycarbonate (PC), Acrylic (PMMA), Polypropylene (PP), POM, and PEEK. Common metals used in CNC machining are stainless steel, magnesium alloy, zinc alloy, titanium, and brass.
In contrast, 3D printing supports a wide range of materials, but these alternatives may not be as strong as traditional engineering materials. For plastics, common options include ABS, PLA, and Nylon filaments, as well as resins with thermoplastic-like properties. When it comes to metals, 3D printing can work with materials like aluminum, stainless steel, and titanium. However, these are typically used in powder form, which is then fused together during the printing process.
Precision
CNC machining is more precise than all the 3D printing methods, including SLS (Selective Laser Sintering), industrial FDM (Fused Deposition Modeling), and DMLS (Direct Metal Laser Sintering). CNC has tighter tolerances, meaning it can achieve very exact measurements. DMLS 3D printing is also accurate but generally cannot match CNC’s precision. Here the a table to show exactly the figures they can reach.
Technology | Tolerance | Minimum wall thickness |
CNC machining | ± 0.025 – 0.125 mm | 0.75 mm |
SLA 3D Printing | ± 0.2 mm | 0.7 – 1.0 mm |
SLS 3D Printing | ± 0.3 mm | 0.7 – 1.0 mm |
FDM 3D Printing | Desktop: ± 0.500 mm Industrial: ± 0.200 mm | 0.8 – 1.0 mm |
SLM/DMLS 3D Printing | ± 0.100 mm | 0.40 mm |
Geometry
One of 3D printing’s biggest advantages is its ability to create highly complex geometries that traditional manufacturing, including CNC, cannot achieve. With 3D printing, parts can be designed with intricate details, internal structures, and unique shapes.
Cost
In general, 3D printing is cheaper, but the cost depends on the number of parts you need and how quickly you need them. For larger quantities (50 to 100 or more), CNC machining may be a better choice. For smaller quantities, 3D printing is usually the more affordable option.
However, comparing the two methods can be tricky due to additional factors. Material costs vary widely, ranging from cheaper options like ABS plastic to more expensive materials like PEEK. This kind of variability can significantly impact the final cost of these two methods.
Speed
3D printing requires minimal setup before starting, and most parts are finished within a few hours, ready for use. However, CNC machining requires skilled setup and precise machining, which can take more than a day to complete. This is because a programmer must select the right tools, create a tool path, and sometimes design custom fixtures to hold the part in place. This setup process can be time-consuming, especially if the part needs to be repositioned.
Surface Quality
In terms of surface quality, CNC is better than 3D printing. CNC machining can produce workpieces with a high surface quality with cutting tools. In opposite, the layer-by-layer printing process of 3D printers leaves a rough surface texture on the workpiece.
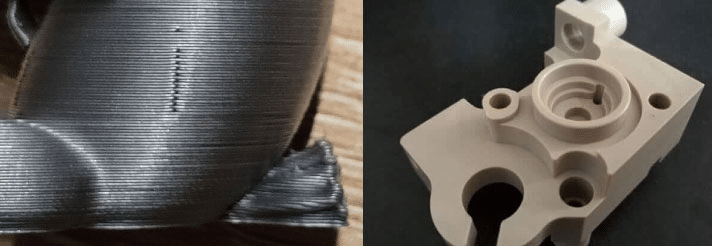
3D printed plastic part (left) and CNC machined plastic part (right)
Production Volume
For making many parts, CNC machining is often cheaper because the setup cost is shared across all the parts, making each part less expensive. On the other hand, 3D printing costs stay about the same for each part since every part uses the same amount of material and machine time, no matter how many are made.
Environmental Friendliness
CNC machining creates waste because it cuts parts out of a solid block, leaving leftover material that needs to be cleaned up and thrown away. In contrast, 3D printing builds parts layer by layer, using only the material needed. This means there is very little waste, except for support structures if they are used. Because of this, 3D printing is more eco-friendly since it produces less waste.
CNC machining vs 3D printing: Key Similarities
Even though there are many differences between these two processes, CNC machining and 3D printing are both popular methods for rapid prototyping and share some similarities. Let’s look at these similarities to help you better understand both processes.
Computer-Controlled Manufacturing Processes
Both CNC machining and 3D printing rely on computer control to operate. They use software to interpret designs and execute precise instructions, ensuring accuracy and consistency. This computer-controlled approach allows for highly detailed and complex parts to be created with minimal human error.
3D Model-Based Production
Both processes use 3D digital models as blueprints to create physical objects. These models are typically prepared in CAD software and saved in file types like STL or OBJ. The machines then follow the 3D model’s specifications to shape or build the part, ensuring that the final product matches the original design.
Wide Usage
CNC machining and 3D printing are both widely used across industries, from aerospace and automotive to healthcare and consumer goods. this is because they both can create custom parts quickly and accurately for rapid prototyping or small-batch production.
CNC machining vs 3D printing: When to choose?
After learning all the above differences between CNC machining and 3D printing, you may find many factors to consider when choosing between these two processes. However, to make things simple, here are some guidelines to help you decide:
- Choose CNC machining if you need to produce a medium to large number of parts (250-500) with simple shapes.
- Choose 3D printing for small quantities or single prototypes, especially if your designs are complex.
- For metal parts, CNC machining can still be cost-effective for small quantities, but there are some limits on design shapes.
- If you need more than 500 parts, you might want to consider other options like injection molding or combining 3D printing or CNC with a forming process.
Conclusion
Both CNC machining and 3D printing are great processes for making prototypes. This article clearly compares these two methods. However, to determine which is best for your specific needs, it’s a good idea to consult with a local or international service provider for advice. KUSLA Prototype is a leading prototype manufacturer in China, and we can provide both CNC machining and 3D printing services to help you get your prototypes done quickly and with high quality.
FAQ
Is CNC better than 3D printing?
There is no definitive answer, as the choice between CNC machining and 3D printing depends on the specific requirements of the project. CNC machining is ideal for creating parts with high precision, tight tolerances, and smoother surface finishes, making it the better choice when you need parts that require precise fitting and durability. On the other hand, 3D printing can also produce high-quality parts, but the finish and fit depend heavily on the type of 3D printer and the material used. For complex geometries or quick prototyping, 3D printing might be more advantages.
What’s the best 3D printing process for plastic parts?
For many prototyping and functional applications, we recommend using Stereolithography (SLA) when printing plastic parts. SLA is known for its high precision and smooth surface finishes, making it ideal for parts that require fine details and accuracy. It uses a laser to cure liquid resin layer by layer, producing parts with excellent resolution and a high-quality finish.
Will 3D printing make CNC machining obsolete?
The answer is no, 3D printing hasn’t replaced CNC machining, traditional methods, or injection molding yet, but it’s improving quickly. Now, you can 3D print parts using more materials, including some metals. However, for many uses, CNC machining is still the better choice.