CNC machining and urethane casting are two widely used processes in the plastic parts manufacturing and rapid prototyping industries. While both serve similar purposes, they operate differently and offer unique advantages. Understanding their differences helps engineers choose the right process, especially when deciding between them. This article explores the differences between CNC machining and urethane casting and provides guidance on when to use each method. let us check the details.
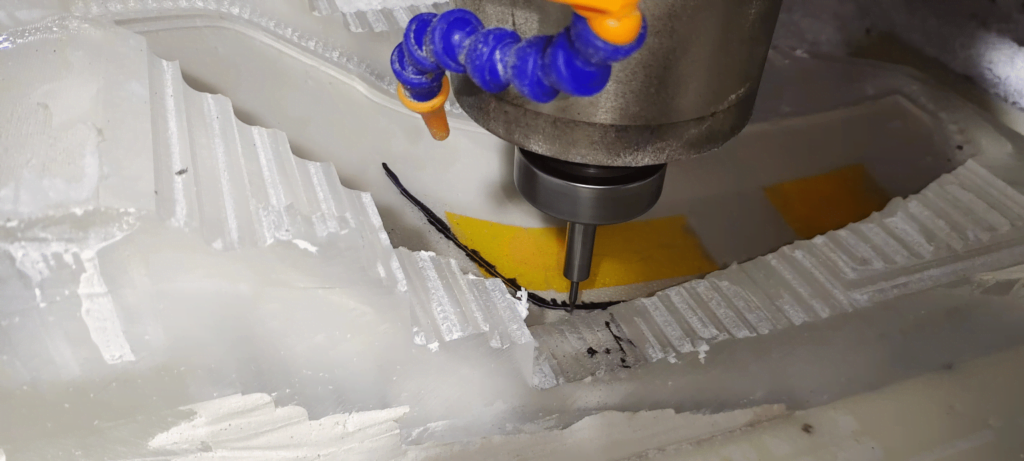
Overview of CNC machining
CNC machining is a subtractive manufacturing process that cuts away material from a solid block to create parts. It uses a CAD model as a guide, and computer software controls the cutting tools and machines to shape the material.
CNC machining is known for:
The reason why CNC machining is widely used is that it offers several key benefits. Let us explore what CNC machining is known for in the market:
- High Precision: CNC machining can achieve extremely tight tolerances, as precise as 0.1mm for plastic parts and 0.01mm for metal parts. This level of accuracy is critical for high-end parts.
- Material Versatility: This process works with a wide range of materials, including metals like aluminum, steel, and titanium, as well as plastics such as ABS, nylon, and acrylic. This versatility allows flexibility for different projects.
- Quick Prototyping: CNC machining does not require molds or tooling, significantly reducing setup time, making it an excellent choice for creating prototypes.
- Cost-Effective for Prototypes: Without the need for molds, tooling costs are eliminated, saving money for small-volume prototypes, especially one-off prototypes.
Overview of Urethane Casting
Urethane casting, also known as vacuum casting, is a manufacturing process that creates parts by using a master pattern to produce a silicone mold. The mold is formed in a vacuum, and polyurethane (PU) materials are poured into it to replicate the master pattern. This method produces accurate replicas with excellent detail.
Urethane casting is known for:
Urethane casting has several key benefits that are well-known in the market. Let us check these benefits:
- Ideal for Small Production Runs: Urethane casting is perfect for low-volume production, as each silicone mold can produce up to 25 identical copies. This makes it a cost-effective option for creating small batches of parts.
- Material Versatility: The process supports a variety of materials, allowing for the production of both rigid and soft rubber parts. Custom materials can also be used to meet specific requirements, such as milky finishes, vibrant colors, or unique textures.
- Low Cost: Urethane casting is affordable, as both the materials and the silicone molds are inexpensive compared to other manufacturing methods. This keeps production costs low, especially for prototypes and short runs.
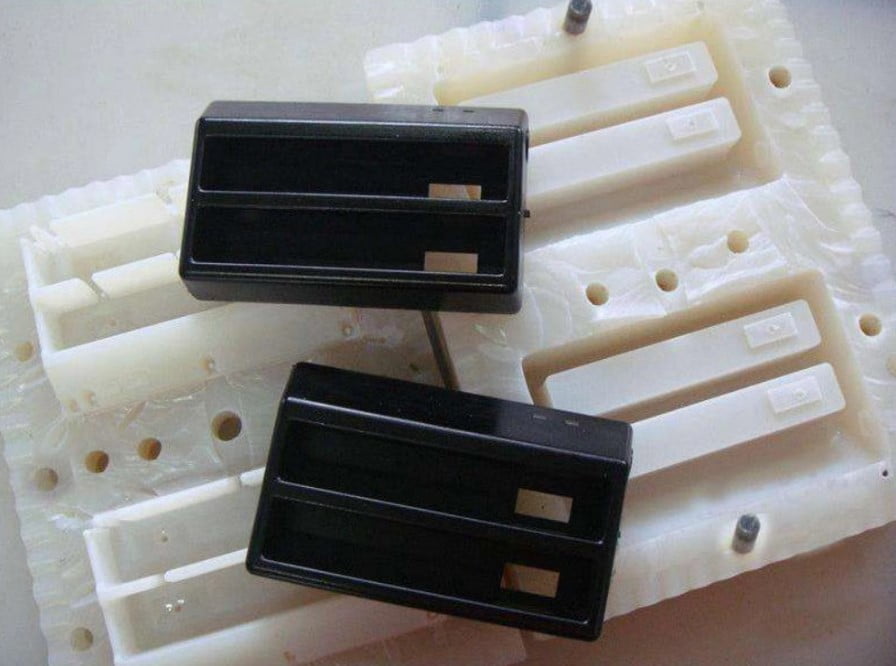
CNC Machining vs Urethane Casting: Key Differences
Although both processes have their benefits, to understand the differences between them, let us compare them based on the factors below:
Machines
CNC machining uses a CNC center, which operates with high precision to cut materials directly. Urethane casting, on the other hand, relies on a vacuum casting machine to create molds and cast parts in a vacuum environment.
Materials
Both methods can work with plastics, but CNC machining uses solid engineering plastics like ABS, nylon, or POM, offering high strength and durability. Urethane casting uses resin materials that mimic engineering plastics, such as ABS-like or PMMA-like resins, making it ideal for simulating finished products.
Precision
CNC machining is far more precise, achieving tolerances mininum 0.01mm. Urethane casting typically has a precision of around 0.2mm due to the thermal expansion and contraction of the silicone mold. As a result, CNC machining is better for parts requiring tight tolerances, while urethane casting works well for less stringent precision needs.
Volume
CNC machining is most suitable for producing one or two prototypes. Urethane casting, however, excels at creating small batches, typically producing 5 to 25 parts per silicone mold. For runs of more than five parts, urethane casting is the preferred option.
Lead Time
For small quantities of more than five parts, urethane casting is faster since it only involves pouring and curing materials in the mold. CNC machining, by contrast, requires each part to be machined individually, increasing lead time. However, for just one or two prototypes, CNC machining is quicker because it eliminates the need for mold preparation.
Cost
CNC machining is generally more expensive for small-volume production. For instance, a simple plastic part might cost $50 with CNC machining, whereas the same part could cost only $10 using urethane casting.
Part Geometry
Urethane casting supports more complex geometries. With a 3D-printed master pattern, it can handle undercuts and hollow sections. CNC machining, however, struggles with such shapes and may require splitting the part and gluing it back together, which can reduce part strength.

CNC Machining vs Urethane Casting: Similarities
After reviewing the differences between these two processes, understanding their similarities can help in using them more effectively. Here are some key similarities:
Use in Diverse Industries for Prototypes
Both CNC machining and urethane casting are extensively used across industries for creating high-quality prototypes. Their can make precise and functional prototypes for testing, validating, and refining designs before moving to mass production.
Fast Lead Time
Both processes are known for their ability to deliver parts quickly compared to other manufacturing methods. CNC machining can produce parts in as little as a few days, especially for simple designs. Urethane casting, while slightly longer due to mold preparation, still offers lead times of around 1 to 2 weeks. This speed is ideal for projects that need quick prototyping or low-volume production runs.
Material Variety
Both methods offer great flexibility when it comes to materials. CNC machining can work with a wide range of engineering plastics and metals, allowing parts to meet specific strength, durability, or weight requirements. Urethane casting can simulate various plastic properties, including rigid and flexible materials, making it suitable for applications requiring customized material characteristics such as transparency, elasticity, or specific color.
Design Iterations
CNC machining’s lack of tooling allows for easy adjustments and modifications to the design at any stage. Urethane casting, on the other hand, uses silicone molds that are quick and inexpensive to remake. This flexibility ensures that changes in design can be implemented without significant cost or delay, allowing teams to perfect their prototypes efficiently.
Conclusion
In summary, CNC machining is ideal for one-off prototypes that require high precision, while urethane casting is best suited for small-volume production at a lower cost, with the ability to mimic engineering plastic properties. At KUSLA, we offer a range of rapid prototyping services, including CNC machining and urethane casting prototyping service, and are here to help guide your choice. We ensure the production of high-quality prototypes and small-volume products tailored to your specific needs.
FAQ
Is CNC machining better than Urethane casting?
The answer depends on the specific requirements of your project. If you need parts with high precision and tight tolerances, CNC machining is the better option, as it can achieve very detailed and accurate results, particularly for complex or intricate designs. On the other hand, for small-volume production runs, urethane casting is often more cost-effective. Urethane casting allows you to produce multiple copies of parts at a lower cost, especially when compared to the higher setup costs of CNC machining. Therefore, the choice between CNC machining and urethane casting depends on factors like precision, volume, lead time, and budget.
What is the lead time of CNC machining and urethane casting?
Generally, the lead time for CNC machining is around 5 to 7 days for producing a single part, depending on the complexity of the design and material used. For urethane casting, the lead time is typically 7 to 10 days for producing a small batch of around 10 parts, as the process involves creating a silicone mold before casting the parts. The lead time for both processes can vary depending on the specific project requirements, but both are relatively fast compared to other manufacturing methods.