CNC machining is commonly used in many industries because it provides high precision. In this process, CNC machines play a big role in ensuring the accuracy of the product. There are different types of CNC tools used for tasks like turning, milling, drilling, and grinding. Each type of tool has specific features that make it best for certain jobs, and they help reduce the need for workers to make adjustments manually. This article will explain the different types of CNC tools and their functions, helping you learn more about how each one works.
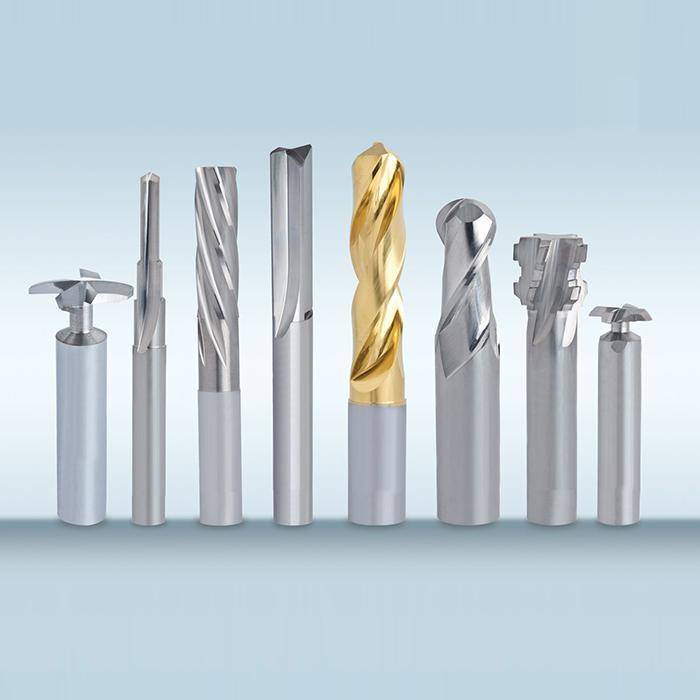
What is a CNC machine tool?
A CNC machine tool is a specialized cutting device used in CNC (Computer Numerical Control) machines to remove material from a solid block of material, such as metal, plastic, or wood. The tool works by rotating or moving along with the machine’s spindle to shape or cut the workpiece into the desired form. These tools are essential for performing various machining operations with high precision. CNC machine tools are typically classified into different types, including turning tools, milling tools, drilling tools, and grinding tools, each designed for specific tasks. By using these tools, CNC machines can produce complex and accurate parts with minimal human intervention.
Structure of CNC machine tools
The structure of various tools consists of two parts: the clamping part and the working part. In tools with an integral structure, both the clamping part and the working part are made as part of the tool body. For tools with an inserted-tooth structure, the working part (teeth or blades) is inserted into the tool body.
There are two types of clamping parts for tools: those with holes and those with shanks. Tools with holes are mounted on the main or sub-spindles of the machine tool through internal holes, transmitting torsional torque via axial or end keys. Examples include cylindrical milling cutters, modular face milling cutters, and others.
Tools with shanks typically come in three types: rectangular shank, cylindrical shank, and taper shank. Turning tools, planers, and similar tools generally have a rectangular shank. A taper shank relies on its taper to withstand axial thrust and transmits torque through frictional force. A cylindrical shank is usually found in smaller tools like twist drills and end mills, where torque is transmitted through the frictional force generated during clamping. The shank of many shank-type tools is made of low-alloy steel, while the working part is made of high-speed steel and is welded to the shank.
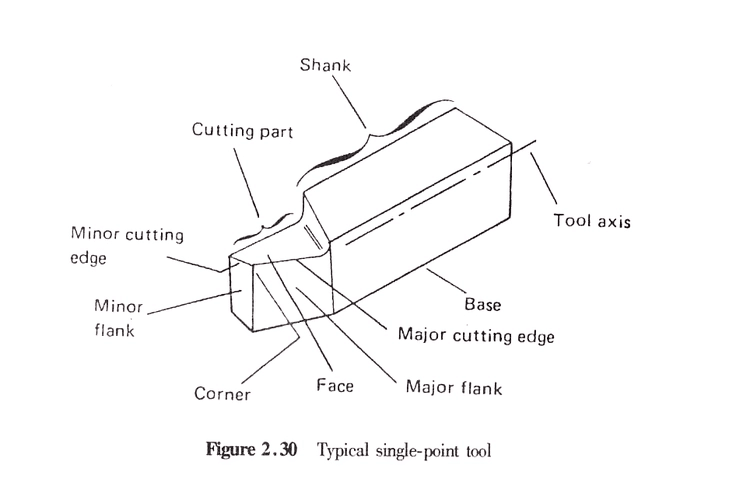
CNC Milling Tools
CNC milling tools are some of the most commonly used tools in the CNC industry. Sometimes, people refer to CNC cutting tools, and in most cases, they are talking about CNC milling tools. These tools are known for their accuracy, thanks to the wide range of tools used in milling. Let’s take a look at the different types of CNC milling tools:
End Mills
End mills have cutting edges on both sides, which makes them very versatile for different milling tasks. The term “end mill” is commonly used for flat-bottomed cutters. The main difference between drills and end mills is that drills can only cut straight down (axially), while end mills can cut in multiple directions. End mills can have one or more flutes, and they are used in various milling operations, such as roughing ends mills.
There are different types of end mills, which vary by the number of flutes and the shape of their nose. When classifying them by nose shape, there are three main types: bull nose, ball nose, and flat end mills. As for the number of flutes, the minimum number any end mill can have is 2, not 8.
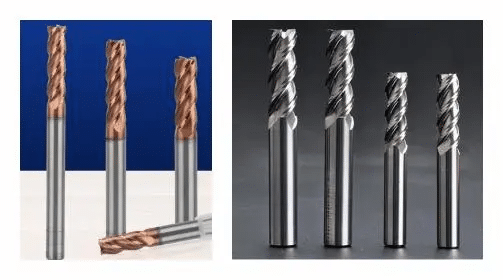
Face Mills
Face mills are CNC tools with flat faces and replaceable carbide cutting edges on the side, designed to cut in the horizontal direction. They are mainly used to create flat surfaces on workpieces. The tool has a large body with interchangeable inserts, allowing for longer tool life since the inserts can be replaced when worn out. Face mills remove material using radial depth and narrow axial cuts, providing precise and rigid cutting. The surface finish depends on factors like feed rate and the number of teeth. Face mills are commonly used to prepare workpieces by creating flat surfaces before more detailed milling operations.
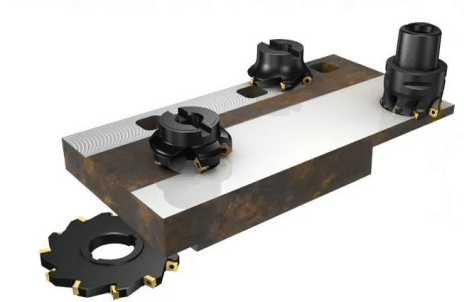
Slab Mills
Slab mills, also known as slab cutters or plain mills, are CNC cutting tools designed for milling flat surfaces, particularly in heavy-duty operations. These tools typically have teeth only on their periphery, making them ideal for creating both wide and narrow cuts quickly. To use slab mills, the workpiece surface must be placed parallel to the CNC mill table. They are especially efficient for heavy material removal and are commonly used to achieve flat surfaces on workpieces.
Fly Cutters
Fly cutters are CNC tools made of a tool body and cutting bits, used for making shallow or wide cuts on workpieces. They can have one or two cutting bits, and the two-bit version can cover a larger area. Fly cutters are similar to face mills but are less expensive. The cutting bits rotate to make both narrow and wide cuts, giving a smooth surface finish. Fly cutters are great for flat surface operations and provide a good finish at a lower cost than most face mills.
Hollow Mills
Hollow mills are CNC cutting tools with a pipe shape, resembling inverted end mills. They are used to create form radii and full points on workpieces. These tools have three or more cutting edges that enclose and revolve around a cylindrical workpiece. Hollow mills are especially useful for quickly and efficiently creating a consistent pre-thread diameter. They can also be used in drill press work for finishing projections that need to be in a specific position.
Thread mills
Thread milling cutters are CNC tools used to cut the teeth shapes of both external and internal threads on workpieces. They can produce single-pitch threads, ranging from M2 to a nominal diameter of 1 millimeter, or variable-pitch threads.
Thread mills work similarly to taps but with the advantage of cutting both internal and external threads, unlike taps, which only cut internal threads. They are especially useful for cutting threads in hard metals or on asymmetrical parts. If you need to work with tough materials or complex shapes, thread mills are a great choice.
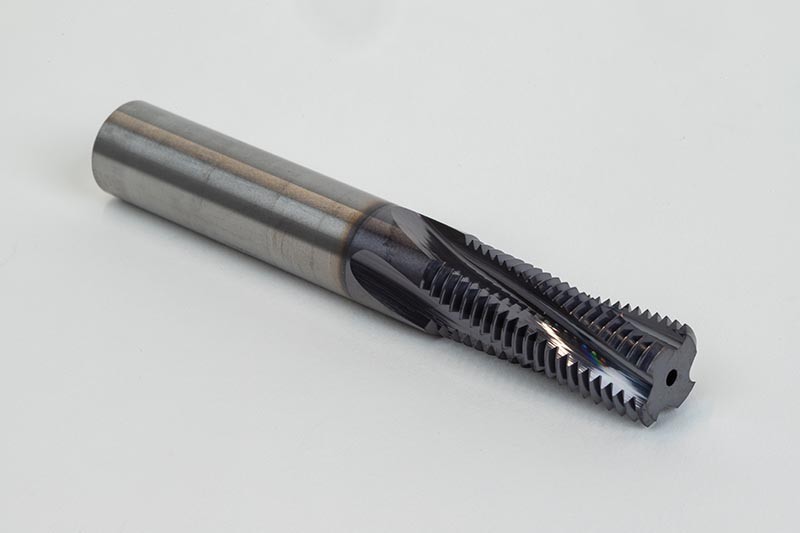
CNC Turning Tools
CNC turning tools work with a lathe (turning machine) that spins the workpiece at high speeds while the turning tool shapes it into the desired form. The final shape of the workpiece depends on the type of turning method and tool used. Some examples of different turning tools as below:
Boring Tools
Boring tools are used with a lathe to enlarge straight or tapered holes that have already been drilled or cast into the workpiece. They help to improve the size, shape, and finish of the hole, ensuring it meets precise specifications.
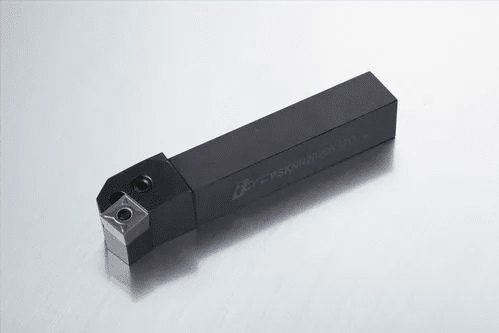
Grooving Tool
Grooving tools are used for turning axial grooves on parts such as slots and gears. Depending on the shape of the groove and its specific application, grooving tools come in different types, including saw-tooth grooving tools, cylindrical-tooth grooving tools, orthogonal grooving tools, and arc-shaped grooving tools. Each type is designed to create grooves with specific features and dimensions.

Knurling Tool
Knurling tools are CNC turning tools used to create various patterns, such as diagonal, straight, or diamond shapes, on the surface of workpieces. These patterns are designed to improve the grip and traction of the finished part, making it easier to handle or use, especially in applications where a secure hold is important, like on knobs, handles, or shafts.
Parting Tool
The parting tool is used during turning operations to cut through workpieces and is typically made from cemented carbide or high-speed steel. It has a blade-like edge that cuts material away from the workpiece. Parting tools are also used by machinists to separate the finished part from the rest of the workpiece, making them essential for completing the machining process.
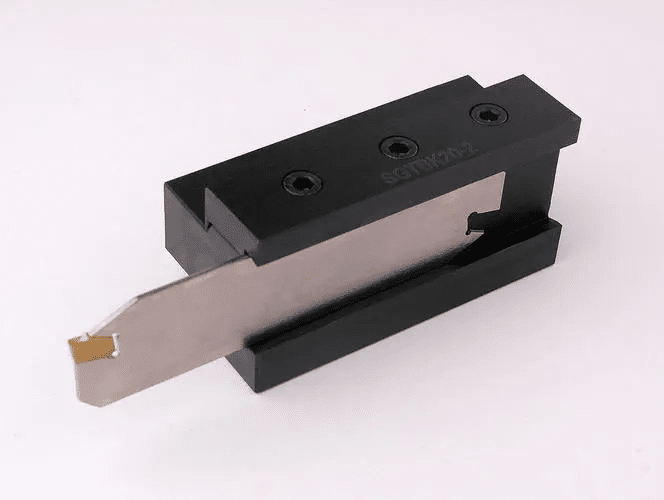
CNC Drilling Tools
Drilling tools, also known as drill bits, are used by machinists to create holes in workpieces. They work with twist drills or CNC mills, using their flutes and tapered cutting points to make precise holes. Drilling tools can also be used to enlarge existing holes. Depending on their design and purpose, drilling tools are categorized into different types, such as twist drills, flat drills, and center drills. Each type is suited for specific drilling tasks on solid materials.
Twist Drill
A twist drill is a tool used to cut round holes in a workpiece by rotating around its fixed axis. Its name comes from the helical shape of the chip flutes, which resemble a “twisted” appearance. This design helps to remove material efficiently while drilling.
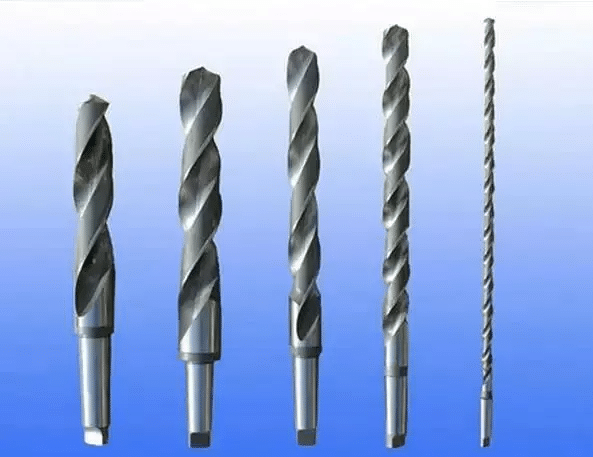
Center Drill
The center drill is a type of drill used for machining round holes, especially in harder materials like metal, ceramics, and glass. Machinists use center drills to create precise starter holes in the workpiece before using other drill bits to enlarge the hole.
Flat Drill
Flat drill is one of the earliest types of drills used for hole machining. It has a simple structure, is easy to manufacture, and cost-effective. Flat drills also have small axial dimensions and provide good rigidity, making them suitable for basic drilling tasks in a variety of materials.
Reaming Drill
Reaming drill is a tool used to enlarge the diameter of a hole and improve its machining quality. It helps achieve a more precise and smoother finish by refining the hole made by a previous drill bit.
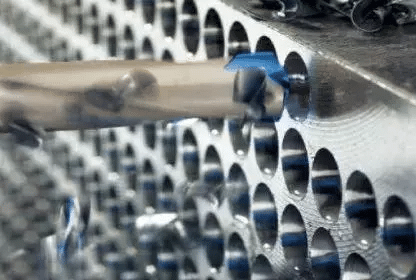
CNC Grinding Tools
Grinding tools work with grinding wheels to smooth the surface of a workpiece, typically achieving high accuracy. The primary grinding tool is the abrasive grinding wheel, which uses abrasive particles to remove material and create a fine surface finish.
CNC machine tool materials
CNC machine tool materials are important because they decide things like feed rate and cutting speed. A simple rule is that the tool material should be harder than the workpiece material. If it’s not, the tool won’t work well. Here are some common materials used to make machining tools:
Carbon Steel
Carbon steel is an alloy made of iron and carbon. Tools made from carbon steel have good wear resistance. They are used for machining soft metals like aluminum, copper, and magnesium.
High-Speed Steel (HSS)
High-speed steel has high strength, toughness, and a certain level of hardness and wear resistance, which meet various tool requirements. HSS tools are commonly used for machining iron risers, milling slots, and drilling oil holes in piston manufacturing.
Cemented Carbide (Hard Alloy)
Cemented carbide is produced by powder metallurgy using hard metal carbides (such as WC, TiC, TaC, NbC) and a metallic binder (such as Co, Ni). The hardness of cemented carbides is higher than that of HSS. Therefore, cemented carbide tools offer much higher cutting performance than HSS tools, with increased durability and 4-10 times higher cutting speeds.
Diamond
Diamond is the hardest mineral material, with excellent thermal conductivity. Its wear rate when paired with various metals or non-metal materials in friction is only 1/50 to 1/800 of that of cemented carbide. It is the ideal material for making cutting tools.
Polycrystalline Cubic Boron Nitride (PCBN)
PCBN is formed by sintering CBN micro-powder with a small amount of binding phase (Co, Ni, or TiC, TiN, Al2O3) using a catalyst at high temperature and pressure. It has high hardness (second only to diamond), heat resistance (1300-1500°C), excellent chemical stability, much higher thermal stability (up to 1400°C), and better thermal conductivity than diamond tools, with a low friction coefficient. However, its strength is lower.
Ceramics
The main advantages of ceramic cutting tool materials are their high hardness and wear resistance, with a room temperature hardness of 91-95 HRC. They also exhibit high heat resistance, maintaining a hardness of 80 HRC at 1200°C.
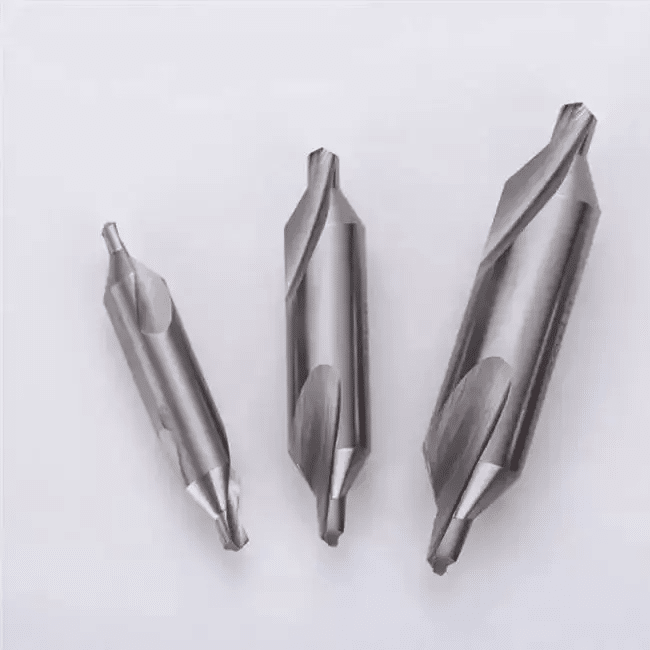
Properties of CNC machine tools
To do a good job in CNC machining, CNC machine tools have some important features, as listed below:
High Hardness
The hardness of tool materials must be higher than that of the workpiece material. If not, the tool edge may lose its shape at high temperatures. This is a key property of tool materials. Below is a hardness value table for different tool materials.
CNC Tool Material | Hardness (HV) |
Diamond | 8500-10000 |
Polycrystalline Cubic Boron Nitride (PCBN) | 4700-5000 |
Ceramics | 1900-2200 |
Cemented Carbide (Hard Alloy) | 1800-2000 |
High-Speed Steel (HSS) | 850-1100 |
Carbon Tool Steel | 600-700 |
High Strength
The material in the cutting part of the tool must be able to withstand significant cutting forces and impacts during machining. This means that tool materials must possess not only sufficient strength but also toughness, ensuring they do not crack or break under the stress of high-speed cutting operations. Stronger materials also help maintain the tool’s integrity over longer periods of use.
High Wear And Heat Resistance
Wear And Heat Resistance is crucial for tools that are subjected to constant friction and heat. A higher high-temperature hardness indicates better heat resistance, which prevents plastic deformation and wear at high temperatures.
Good Thermal Conductivity
Good thermal conductivity means the material can effectively conduct heat away from the cutting edge. This allows the heat generated during cutting to dissipate more easily, reducing the temperature in the cutting area. By lowering the temperature, thermal conductivity helps prevent excessive tool wear, thermal damage to the workpiece, and helps improve the overall efficiency of the machining process.
Good Processability And Economy
Tool materials should be easy to machine and shape, allowing manufacturers to create CNC machine tools without incurring high production costs. If the materials are difficult to process, the cost of producing the tools increases, making them less economical for business use. Using materials that balance performance with ease of processing can help keep the cost of CNC tools competitive and suitable for large-scale production.
Chemical Stability
Tool materials must be chemically stable, meaning they should not react with the surrounding environment or materials at high temperatures. This ensures that the tool remains effective in harsh cutting conditions and doesn’t degrade or corrode when exposed to chemicals, coolants, or high heat.

Coatings for CNC machine tools
A important factor that contributes to the properties of CNC machine tools is the coating applied to them. These coatings can enhance the tool’s durability, hardness, and resistance to wear. They also help the tools withstand higher temperatures and improve overall performance. Some common examples of tool coatings include:
Titanium Nitride Coating
Abbreviated as TiN coating, it is a hard and thin film applied to the surface of tools. The TiN coating is golden and is often used on milling and drilling tools. It improves the performance and durability of the tools.
Titanium Carbonitride Coating
Titanium carbonitride coating, abbreviated as TiCN, is used to enhance tool hardness and provide good surface lubrication. It is commonly applied to high-speed cutting tools.
Diamond Coating
Diamond coatings improve the wear resistance of tools used for cutting non-metallic materials. They are ideal for processing graphite, metal matrix composites (MMC), high-silicon aluminum alloys, and other highly abrasive materials.
General-Purpose PVD Coating
General-purpose PVD coatings enhance tool hardness and increase oxidation resistance at higher temperatures. These coatings are suitable for high-speed steel cutting tools and forming tools, resulting in improved machining performance.
Chromium Nitride Coating
Chromium nitride coating, abbreviated as CrN, has excellent anti-bonding properties, making it an ideal choice for applications where chip buildup is common. This coating enhances the performance of high-speed steel tools, cemented carbide tools, and forming tools.
Zirconium Nitride Coating
Zirconium nitride coating, abbreviated as ZrN, is an anti-adhesive coating that does not contain titanium or chromium. It is suitable for processing aluminum, copper, and titanium.
Titanium Aluminum Nitride / Aluminum Titanium Nitride Coating
Titanium aluminum nitride/aluminum titanium nitride (TiAlN/AlTiN) coatings can extend the life of high-temperature tools by incorporating an aluminum oxide layer. These coatings are particularly suitable for dry or semi-dry cutting of cemented carbide tools.
How to Choose the Right CNC Machine Tool
When choosing the right cutter for your machining project, it’s important to first identify the machining requirements. This includes understanding the materials of the workpieces and the types of operations you will perform. Here are some tips to help you choose the right CNC cutter:
The Material of the Tool
Refer to the information listed above when selecting tool material. High-speed steel (HSS) is one of the best options for many applications. However, if you need a tool that can withstand higher hardness or wear, you may want to consider cemented carbide tools.
Coating of the Tool
Coatings like titanium nitride (TiN) can significantly improve the tool’s lifespan and performance. However, it’s important to consider the added cost of these coatings and balance it with the benefits they offer for your specific project.
Machining Process
Choose the right type of tool based on the machining process you will be using. Whether it’s CNC turning, milling, or drilling, make sure the tool is suited for the specific task. Different tools are designed to perform better in specific types of operations, so selecting the appropriate one will ensure optimal results.
Number of Flutes
The number of flutes on a tool affects the speed at which the machine can cut. More flutes allow the cutter to move faster against the workpiece. However, too many flutes can cause small pieces of the workpiece to get stuck between them. So, it’s important to choose the right number of flutes for the job.
Work with CNC machining shop – KUSLA
CNC machine tools are essential for machining tasks. But to ensure everything goes smoothly, you need to pick the right tool. Instead of stressing over which one to choose, you can leave it to the experts. At KUSLA, we have a wide range of CNC machine tools in our shop. We can handle various machining needs for different parts. KUSLA is your one-stop shop for all CNC machining projects. We offer many services, including milling, turning, drilling, EDM, and more. Whether it’s prototype CNC machining or low-volume production, we guarantee high-quality parts for every project.
FAQ
What is the most common material used for CNC machine tools?
Carbon Steel and High-Speed Steel are the most common materials used for CNC machine tools because they have good wear resistance and are suitable for most of the commonly used metals such as aluminum, titanium, brass, stainless steel, and plastics.
What are the differences between CNC milling tools and CNC drilling tools?
The main difference between CNC milling tools and CNC drilling tools is that they are used for different functions. CNC milling tools are used for cutting the shapes of parts and CNC drilling tools are used to create holes on the parts. So these functions make them have different tool structures and materials.