Aluminum is a non-ferrous metal widely used in various industries in the world, its perfect property makes it the most popular material in the market. CNC Aluminum Machining, As a high-precision machining method, is preferred by manufacturers both for prototypes and products. However, to get high-quality aluminum parts, it’s important to understand how aluminum CNC machining works. In this article, we will share with you a basic guide about CNC Aluminum including the common types of aluminum used, machines, and best practices.
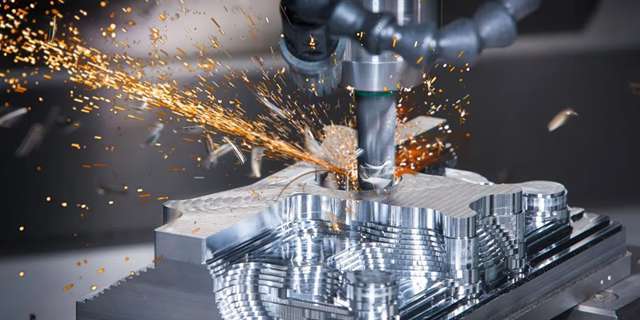
What Is Aluminum Machining?
Aluminum machining is the process of using aluminum alloys to manufacture products with CNC machining, which relies on computer-controlled software and specialized equipment to guide tools across the surface of aluminum materials.
This method produces highly accurate and precise parts. The wide variety of aluminum grades and its excellent machinability make it a popular choice for machining applications. Additionally, its affordability makes aluminum ideal for prototyping and creating custom tools.
Benefits of Aluminum for CNC machining
When considering metal materials for CNC machining, aluminum stands out for its remarkable properties that enhance the efficiency, durability, and cost-effectiveness of manufacturing processes. Here is why:
Easy to Machine
Aluminum is very easy to machine because it is a soft metal that cuts and shapes easily. CNC milling and CNC turning tools can cut it without much effort. This reduces machining time, lowers costs, and minimizes the risk of deformation. As a result, aluminum parts are more precise and consistent.
Lightweight and Strong
Aluminum is about one-third as dense as steel, making it very lightweight. Despite being light, it is also very strong. This balance of strength and lightness is called the strength-to-weight ratio. Aluminum’s high strength-to-weight ratio makes it ideal for parts used in industries like automotive and aerospace, where both strength and reduced weight are important.
Diversity
There are hundreds of Aluminum alloys in the market with different properties for different applications. you can easily find the best type of aluminum alloy for your CNC-machined aluminum part.
Cost-Effective
Thanks to the easy-to-machine property of aluminum, CNC machining aluminum can make it in a short lead time which saves manufacturing costs. and meanwhile, Aluminum is an abundant and low-cost material that could save material costs for you. its lightweight property also contributes a lot to the transportation cost.
Scratch and Corrosion Resistant
Aluminum is resistant to scratches and corrosion in most marine and atmospheric conditions. These properties can be further improved by anodizing. However, the level of corrosion resistance depends on the aluminum grade. The most commonly CNC-machined grades usually offer the best corrosion resistance.
Electrical Conductivity
Pure aluminum has a high electrical conductivity of about 37.7 million Siemens per meter at room temperature. Aluminum alloys also conduct electricity, making them useful for electrical components. However, their conductivity is lower than that of pure aluminum. If electrical conductivity is not a key requirement for your part, aluminum alloys might not be the best choice.
Custom Finish
Aluminum machined parts can be finished in many ways to achieve the look you want. Common options include chromate conversion coating, anodizing, and powder coating These finishes allow for a custom appearance to suit your project needs.
Recyclable
Aluminum is highly recyclable, which is perfect for CNC machining because CNC machining is a subtractive manufacturing method which means there is a relatively large amount of waste material in the form of chips from the cutting tool. In this way, CNC machining applications can use recyclable materials to reduce the cost of machined parts.
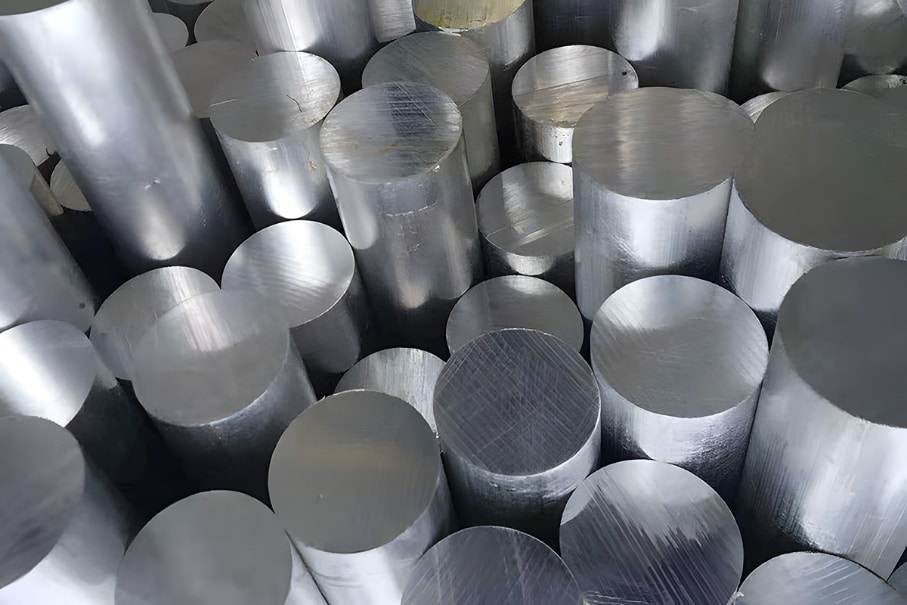
Aluminum Alloys for Machining
Aluminum alloys are created by adding small amounts of other elements like zinc, magnesium, silicon, manganese, and copper to pure aluminum, which is 99–99.6% aluminum. Here’s an overview of common aluminum alloy series based on their main alloying elements:
1000 Series
These alloys are almost pure aluminum, with 99% or more aluminum content. They are soft but can be strengthened through work hardening. For example, aluminum 1199, with 99.99% aluminum, is ideal for making foil.
2000 Series
Copper is the main alloying element, making these alloys very strong through heat treatment (precipitation hardening). However, they have lower corrosion resistance. Aluminum 2024, which also contains manganese and magnesium, is widely used in aerospace applications due to its improved corrosion resistance.
3000 Series
Manganese is the key alloying element. These alloys cannot be heat-treated but can be work-hardened for added strength. Aluminum 3003 is a versatile, general-purpose alloy, while 3004, containing magnesium, is commonly used for beverage cans.
4000 Series
These alloys contain silicon, which lowers their melting point. Aluminum 4047 is used in cladding and construction, while 4043 is often used as a filler material for welding 6000 series alloys.
5000 Series
Magnesium is the primary alloying element, providing excellent corrosion resistance. These alloys are ideal for marine applications and extreme environments. Aluminum 5083 is a popular choice for marine use.
6000 Series
Silicon and magnesium are the main alloying elements. These alloys are easy to machine and can be precipitation-hardened. Aluminum 6061 is widely used in structural and aerospace applications due to its good corrosion resistance and versatility.
7000 Series
Zinc is the primary alloying element, often combined with magnesium, copper, or chromium. These alloys achieve maximum strength through heat treatment and are commonly used in aerospace applications. Aluminum 7075, though less corrosion-resistant than other series, is highly durable and has universal applications, especially in aerospace parts machining.
Best Aluminum Grades For CNC Machining
Among the above aluminum alloys for machining, here we introduced the most three common grades below:
Aluminum 6061
Aluminum alloy 6061 is the most widely used in CNC machining because of the good balance between strength and machinability. it is used across various applications including chassis manufacturing, bicycle frames, valves, and computer components.
Aluminum 7075
Aluminum alloy 7075 is also popular even though not like the 6061. it is known for its high strength and corrosion resistance, which is good for components in aerospace and military industries such as aircraft fittings, missile parts, and fuses.
Aluminum 2024
Aluminum alloy 2024-T4 is primarily used in the aerospace industry. This is because of its mechanical properties, like great weariness resistance, and high strength.
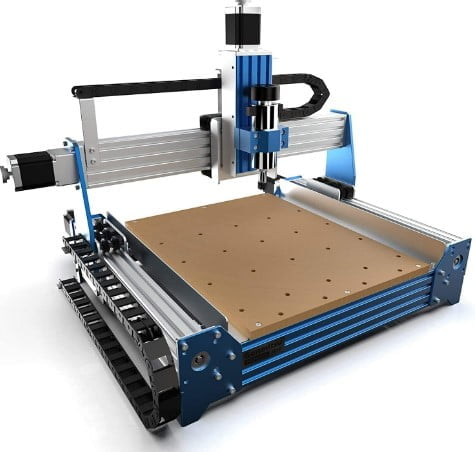
Machines for aluminum CNC machining processes
Some Common machines are used for Aluminum CNC machining according to the product requirement to fulfill such as shapes, and precisions. these machines can apply different machining processes for the aluminum parts, let us check what they are:
CNC Router
CNC Router is designed to cut soft materials such as wood, plastics, and foam. it is also ideal for cutting aluminum because aluminum is a soft metal compared with others. CNC router cutting aluminum provides a very good solution for aluminum parts for low cost and fast turnaround. However, for some complex aluminum parts with high precision requirements, a CNC router will not be the best solution.
CNC Milling Centers
CNC milling is one of the most widely used methods for machining aluminum parts. It involves rotating a multi-point cutting tool while the workpiece remains stationary. Material removal happens through the feed motion of the workpiece, the cutting tool, or both, and this motion can occur along multiple axes.
CNC milling machines are more powerful and precise than CNC routers, making them ideal for creating high-precision aluminum parts. While these machines are designed to cut hard materials like steel and titanium, they are also highly effective for machining aluminum.
A 5-axis CNC milling machine is especially suited for machining complex aluminum geometries in a single operation—something CNC routers cannot achieve. These machines offer unmatched versatility and precision, making them the go-to choice for producing detailed and intricate aluminum components.
CNC Lathes (CNC Turning Centers)
CNC lathes, also known as CNC turning centers, hold and rotate a workpiece securely while a tool head positions a cutting tool or drill against it. This allows for precise material removal, making these machines essential across many industries.
Common operations performed on CNC lathes include drilling, shaping, slot-making, tapping, threading, and tapering. They are rapidly replacing older manual lathes due to their ease of setup, efficient operation, high repeatability, and superior accuracy.
CNC Laser Machines
CNC laser machines use a high-power laser beam to melt, burn, or vaporize material, creating precise cut edges. Like plasma cutters, they hold sheet material flat on a cutting table, with the laser beam path controlled by a computer.
Laser cutters are more precise and energy-efficient than plasma cutters, especially for cutting thin sheets. However, only the most powerful and costly laser machines can effectively cut through thick or dense materials.
How to make Aluminum parts by CNC machining?
As a beginner, Here is the step-by-step guide for you to learn how to make aluminum parts on a CNC machine and get the perfect CNC-machined Aluminum part. let us walk through the process step by step:
Step 1: Prepare the CAD model
Begin by creating a 3D model of the Aluminum part using CAD (Computer-Aided Design) software such as AutoCAD, CATIA, and SolidWorks.
Step 2: Material Selection
Select the right grade of aluminum for your application according to the property required to fit your part’s requirements. Popular aluminum alloys for CNC machining include 6061, 7075, and 2024, you may start with a check with these aluminum alloys.
Step 3: Programming
Convert the 3D CAD model into machine-readable instructions using CAM (Computer-Aided Manufacturing) software. Define machining operations such as milling, drilling, turning, and threading, along with tool paths and cutting parameters.
Step 4: Set Up the Machine
Select the appropriate cutting tools (such as end mills or drills) based on the material, part geometry, and complexity. Consider factors like tool diameter, flute type, coating (e.g., TiN, TiCN, TiAlN), and cutting speeds/feed rates to optimize machining efficiency. Ensure the aluminum workpiece is securely positioned on the machine using the correct fixture.
Step 5: Machining
Load the CAM program into the CNC machine and, if necessary, run simulations to verify toolpaths and avoid collisions. Once everything is set, start the machining process. The CNC machine will use cutting tools to remove material from the aluminum block, following the programmed path until the final part is created according to the design specifications. Let the machine run until the program is complete.
Step 6: Post Surface Finishing
After machining, remove any milling marks and burrs from the aluminum parts. Apply surface finishing processes as specified in the design, such as anodizing, deburring, sanding, or coating. These secondary operations improve the part’s appearance, durability, and functionality.
Step 7: Check the quality
Inspect the CNC machined Aluminum part using measurement tools such as calipers, micrometers, and CMM (Coordinate Measuring Machine). Check critical dimensions, surface finish, and overall quality to ensure they meet the required standards and tolerances.
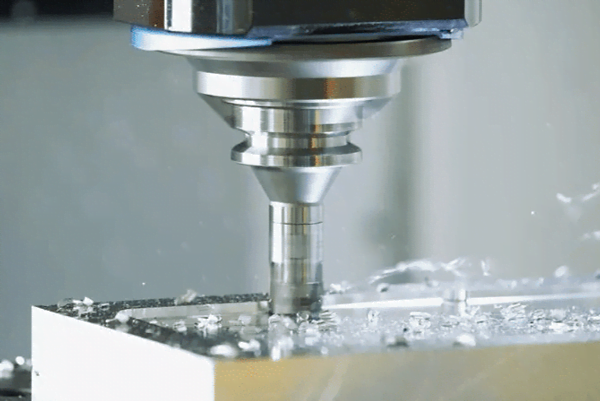
Finishing for CNC machined Aluminum Parts
After CNC machining an aluminum part, various post-processing methods can be applied to improve its physical, mechanical, and aesthetic qualities. Some of the most common finishing processes include:
Anodizing
Anodizing is an electrochemical process where an aluminum part is submerged in a diluted sulfuric acid solution, and an electric current is passed between the cathode and anode. This process transforms the exposed surfaces into a hard, non-reactive aluminum oxide coating. The thickness and density of the coating depend on factors like the consistency of the solution, anodizing time, and applied current. Anodizing can also be used to add color to the part, providing both enhanced durability and aesthetic appeal.
Bead and Sand Blasting
Bead blasting is used mainly for aesthetic purposes. In this process, the CNC-machined aluminum part is blasted with tiny glass beads using a high-pressure air gun. This removes material and creates a smooth surface, giving the aluminum a satin or matte finish. The key parameters for bead blasting are the size of the glass beads and the air pressure used. This method is best used when dimensional tolerances are not critical for the part.
Powder Coating
Powder coating is a process where an aluminum part is coated with colored polymer powder using an electrostatic spray gun. After coating, the part is heated and cured at around 200°C. This process enhances the part’s strength and increases its resistance to wear, corrosion, and impact, providing a durable and attractive finish.
Coating
Coating involves applying a layer of another material, such as zinc, nickel, or chrome, onto an aluminum part. This is done to improve the part’s properties, such as corrosion resistance or wear resistance. Coating is typically achieved through electrochemical processes.
Key Challenges in CNC Machining Aluminum
While aluminum offers many benefits, there are several challenges to keep in mind when machining aluminum parts, and being prepared to handle these challenges is needed to get the good parts. let’s check:
Material Welding
Aluminum is known for being “sticky” during machining, meaning it can weld onto the cutting tool, particularly at high speeds. To prevent this, use tools with proper coatings and apply suitable coolants to manage heat and minimize material buildup.
Tool Wear
The adhesive nature of aluminum can accelerate tool wear, which affects precision over long machining runs. To avoid this, use carbide or diamond-tipped tools, which have longer lifespans and help maintain accuracy.
Deformation
While aluminum’s softness makes it easier to machine, it also makes the material easy to deform if not handled properly. Ensure proper work-holding fixtures are used to secure the material, and avoid applying excessive force that could cause deformation.
Best Practices for CNC Machining Aluminum
Understanding the proper technique and preparation is key to achieving high-quality results. Here we summarize some best practices of CNC machining operations for you to follow to get high-quality, precise, and cost-effective aluminum parts. Let’s check:
Choose The Right bits
The carbide tool is a great choice for CNC aluminum, However, A specialized CNC aluminum router bits is your best Choice.
Optimize Cutting Speeds And Feeds
Use higher cutting speed above 18000rpm and reduced feed rates of around 300-600 meters per minute for milling your aluminum products. This is because Too slow feed and speed may impair the tool’s cutting action and would just cause rubbing between the part and the tool.
Use Coolant And Lubrication
Aluminum generates high temperatures during the CNC milling process, so to control the temperature, lubricating aluminum and cooling aluminum is very important, especially for extremely precise operations. Use a high-quality cooling lubricant solution to dissipate the heat and increase part surface quality.
Watch Tool Wear
A dull cutting tool may cause a bad surface finish because it does not cut the material with the desired quality, and also it will increase heat generation and machining times. Replace the end mill in time to achieve the best results.
Secure Clamping Rigidly
aluminum workpieces need to be clamped rigidly. because if not, this will cause undesired shifts in the workpiece while milling. The rigid clamping of the workpiece will result in a high precision and good surface finish.
Keep Saftey
Always wear safety glasses and hearing protection during aluminum processing for your safety. Aluminum chips can fly around when milling aluminum, so you need to well protect yourself.
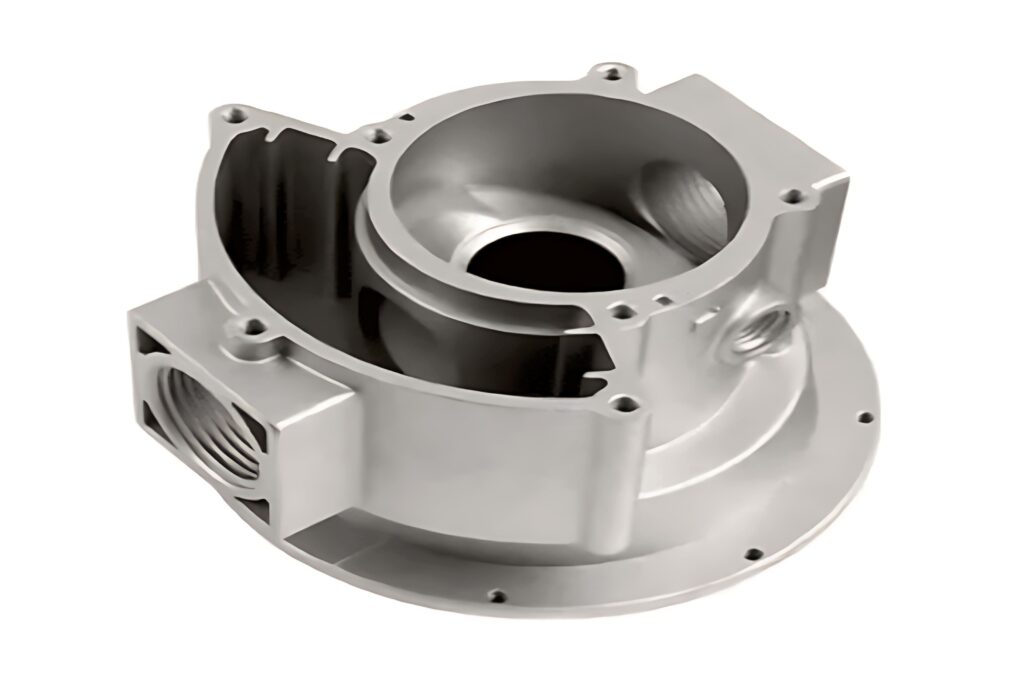
Applications Of Aluminum CNC Machined Parts
Aluminum’s excellent strength-to-weight ratio, durability, and machinability make it a top choice for industries requiring precision, lightweight materials, and high-performance components. Here are some Common applications where aluminum parts are widely used due to their advantages:
Aerospace
Aluminum CNC machined parts are widely used in aerospace for structural components such as engine parts, airframes, and landing gear. Aluminum alloys are chosen for their excellent strength-to-weight ratio and lightweight, making them ideal for reducing the overall weight of aircraft. CNC machining ensures precision and reliability, essential for producing aero-structures like wing panels and fuselage sections that meet the strict quality standards of the aerospace industry.
Automotive
In the automotive industry, aluminum CNC machined parts play a critical role in producing parts like engine components, transmission housings, and electric vehicle components. The lightweight, strength, and durability of aluminum alloys help reduce vehicle weight and enhance durability, making them a popular choice in automotive engineering.
Consumer Electronics
Aluminum CNC machined parts are commonly used in the production of consumer electronics such as laptops, smartphones, and audio equipment. Aluminum’s lightweight makes it ideal for casing electronic devices, offering protection for internal components. High-end audio equipment, like amplifiers, headphones, and speaker enclosures, also benefits from aluminum’s precision and ability to dissipate heat, which is why Aluminum CNC machined parts are used for many consumer electronics applications.
Conclusion
This guide almost shares everything about aluminum CNC machining, and it’s important to follow the best practices for your project to make High-quality aluminum parts. At KUSLA, we offer professional Aluminum CNC machining services with years of experience in producing fantastic aluminum parts and prototypes Contact us today to start your project!
FAQ
What is the most common type of aluminum used for CNC Milling?
Aluminum 6061 is generally the most common aluminum alloy used for CNC milling. It offers a good balance between strength, machinability, and corrosion resistance, making it a versatile choice for a wide range of applications. This alloy is easy to machine and is often used for both structural and functional parts in industries such as aerospace, automotive, and general manufacturing.
Can a CNC Router Cut Aluminum?
Yes, a CNC router can cut aluminum. Many standard CNC routers are equipped with a T-Slot table, and when paired with solid carbide router bits, they are capable of machining aluminum effectively. However, to achieve the best results, it’s important to adjust the settings properly, including feed rates, spindle speed, and cutting depth, in order to find the optimal parameters for aluminum.