Surface finishing is an important final step in making metal parts, like those created through CNC machining or sheet metal fabrication. This step improves both how the metal looks and how it performs. One popular option is the brushed finish, which creates a smooth, consistent surface and makes uneven metals look clean and uniform. But what exactly is a brushed finish, and how does it work? This article will explain the brushing process, the tools used, the types of brushed metals, and their common uses. Let’s read more!
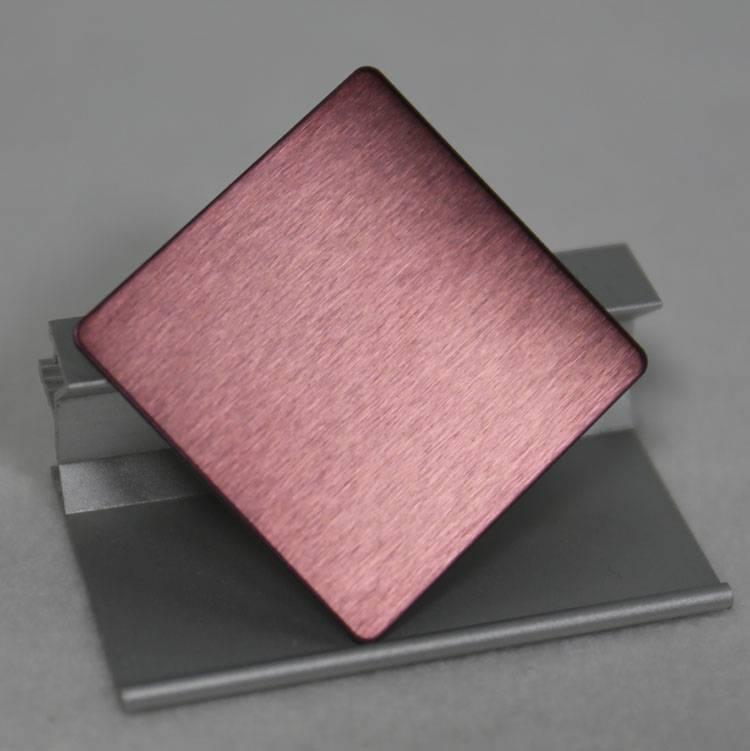
What is a Brushing finish?
A brushing finish is a simple technique used to give metal surfaces a unique, textured look. This process uses a wire brush or abrasive pad to create fine lines, called “grain,” on the metal surface. The result is a smooth, satin-like finish that isn’t shiny like a mirror but still has a decorative and elegant look. It’s great for adding a touch of style to metal parts while also making them resistant to scratches and fingerprints.
You’ve probably seen brushed finishes on everyday items, like kitchen appliances, watch bands, or even furniture. These products have a sophisticated and classy appearance that stands out. A brushed finish is an excellent choice for CNC-machined parts or injection-molded products when you want a balance of style and durability.
Types of Brushed Finishes
There are two main types of brushed finishes: linear brushed and circular brushed. Let’s take a closer look at each:
Linear Brushed
This finish features straight, parallel lines or strokes that run in a single direction. The lines are applied evenly to create a consistent pattern. Linear brushing gives the metal a sleek, modern look, making it ideal for appliances, furniture, and other contemporary designs.
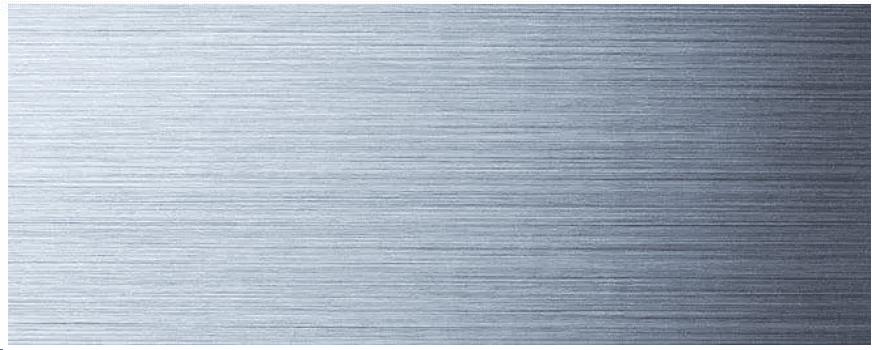
Circular Brushed
Also called radial brushing, this finish creates patterns of concentric circles that spread out from a central point. It is achieved by rotating a cylindrical brush or polishing wheel, often with a polishing paste and kerosene. Circular brushing is commonly used for decorative purposes on items like signs, small dials, or surfaces that need a unique, artistic touch.
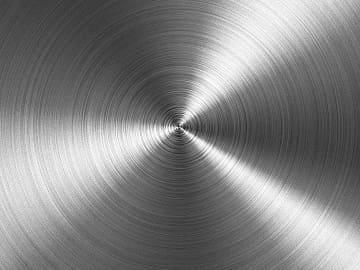
Benefits of a Brushed Finish
A brushed finish offers two key advantages:
Improved Durability
Brushing helps protect metal surfaces from wear and tear caused by handling and transportation. It also enhances the surface’s resistance to corrosion, making metal parts more durable and long-lasting.
Enhanced Appearance
The brushed finish creates a unique, textured look that stands out compared to other finishes. It gives metal parts a sleek, refined appearance while helping to hide scratches, dents, and marks left from machining. This makes it a popular choice for those who want their parts to look stylish and professional.
What material can be brushed?
Brushed finishes are commonly applied to various metals to achieve a textured, stylish appearance. The most frequently brushed metals include stainless steel, aluminum, brass, and bronze.
Stainless Steel
Stainless steel is a popular choice for brushing because of its strength, corrosion resistance, and attractive look. Brushed stainless steel is often used in appliances, kitchenware, architectural designs, and automotive parts.
Aluminum
Brushing aluminum involves using abrasive tools or brushes to create smooth, consistent patterns, either linear or circular. Brushed aluminum is widely used in furniture, signs, and electronic casings due to its sleek and modern appearance.
Brass
Brushed brass has a matte, textured look that reduces its reflectiveness while enhancing its natural beauty. It’s commonly used in decorative items, architectural features, and musical instruments for its elegant, distinctive style.
Bronze
Brushing bronze gives it a textured, aged appearance, adding character to the metal. Brushed bronze is often used in art, sculptures, architectural elements, and decorative hardware to achieve a timeless, classic look.
Standard Brushes for Brushed Finishes
When creating brushed finishes in precision machining, various brushes can be used to achieve the desired look and texture. These brushes are designed to meet different needs, and while they may work in unique ways, they all get the job done. Here are two main types of brushes commonly used:
Power Brushes
Power brushes are made from materials like carbon steel, synthetic fibers, and ferrous or non-ferrous wires. They are versatile tools used in manufacturing for tasks like edge blending, surface cleaning, and polishing. The effectiveness of power brushes depends on their horsepower—the pressure applied during the finishing process.
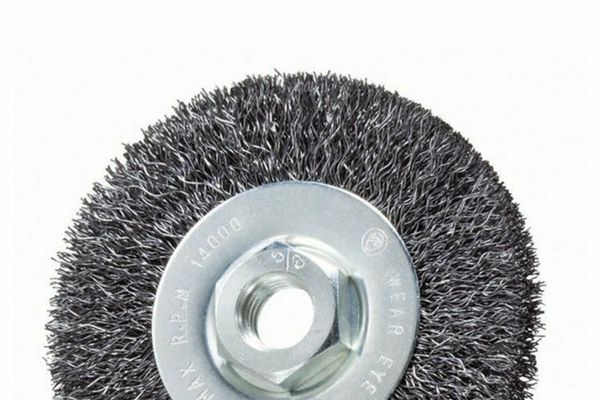
Steel Wire Brushes
Steel wire brushes are a go-to option for metal fabrication because they clean surfaces without damaging the base material or altering the part’s dimensions. Unlike sand particles, steel wire brushes use their hardened wire tips to polish the surface gently and efficiently.
These brushes work by combining high-speed motion with strong steel wires to remove contaminants while leaving the underlying metal intact. Steel wire brushes are available in various shapes and configurations, making them adaptable to different applications and ensuring precise results.
Brushing Finish Process
Creating a brushed finish requires precision, the right tools, and careful execution. The process can be divided into three main stages:
Step 1: Cleaning and Preparing
Before brushing, the metal surface must be clean and free of dirt, oil, or any imperfections. Start by thoroughly cleaning the surface with a degreaser or alcohol. This removes any grime, weld slag, or bumps that could interfere with the brushing process.
Once the surface is clean, sand it using fine-grit sandpaper. This step smooths out any scratches or rough areas, ensuring an even base for the brushing stage. Proper preparation is key to achieving a consistent and polished finish.
Step 2: Brushing- Creating the Texture
Now comes the fun part: brushing the surface. Using a steel wire brush or an abrasive pad, begin brushing the metal in a consistent direction to create the signature “grain” lines of a brushed finish. If you’re using a machine, it will help ensure uniformity, but manual brushing can work just as well with steady and controlled movements.
This process is also called mechanical polishing, where the brush removes surface defects while leaving a clean, textured appearance. Avoid over-brushing, as it can cause irregularities or damage to the surface.
Step 3: Cleaning and Finishing
Once brushing is complete, clean the surface to remove any remaining debris or metal particles. Rinse the metal in water or use a solution containing alkalis, acids, or surfactants to thoroughly clean the surface. Alternatively, electrochemical cleaning can be used for a more refined finish.
Dry the surface with a clean cloth to reveal the final brushed look. For extra protection, consider applying a coating to keep the brushed finish looking shiny and new.
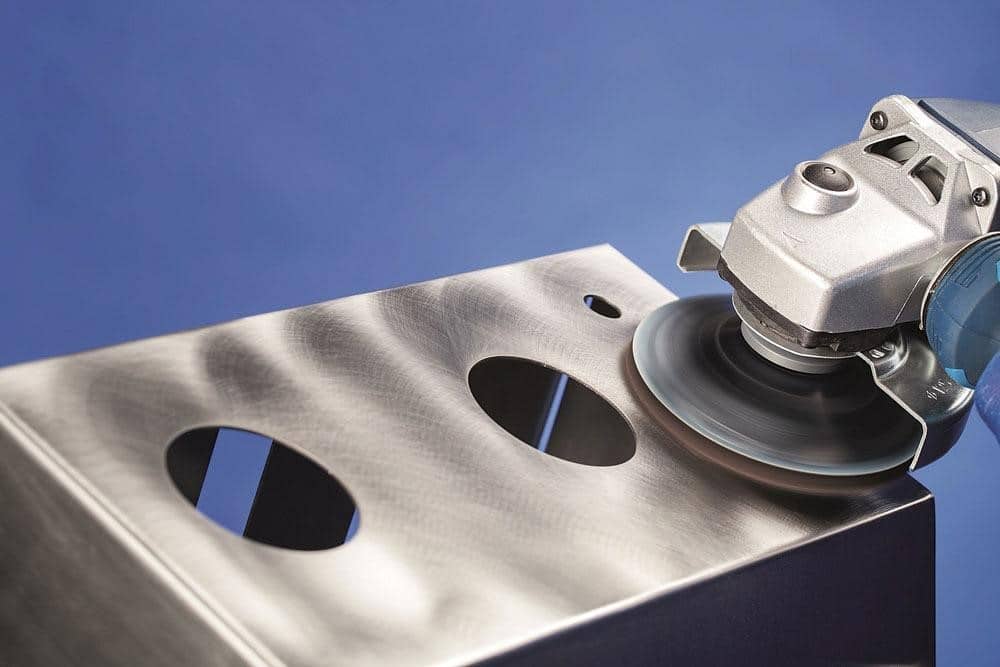
Tips of Brushing Finish
Achieving a flawless brushed finish is key to the success of custom-manufactured parts. Here are some tips to help you perfect the process:
Use the Right Brush
Different brushes are designed for specific materials and finishes. Wire brushes work best for metal surfaces, while nylon brushes are gentler and better suited for more delicate materials. It’s important to choose the right type of brush for metal parts and their specific applications to avoid using the wrong tool for the brushing process.
Keep the Brushing Direction Consistent
For a uniform and polished finish, it’s essential to maintain a consistent brushing direction. Whether you brush horizontally, vertically, or in circles, sticking to the same direction throughout the process ensures an even appearance across the entire surface.
Use the Highest Possible Safe Speed
To achieve the best brushing finish, use the highest speed possible for your brush, as this ensures efficient results. Combine this with light pressure to enhance brushing effectiveness and prolong the brush’s life. A fine-wire brush at high speed can deliver similar results to a coarse-wire brush at lower speed, reducing production costs. Avoid increasing pressure to make up for low speed, as this can cause filament breakage and shorten brush life.
Keep Brushes Clean
To get the most out of your brushes, keep the brushes clean at all times. After use, store them away from workbenches to avoid contamination from carbon steel particles. For critical operations, it’s important to degrease the wire brushes before starting to ensure optimal performance.
Clean the surface first
A clean and smooth surface is key to achieving a successful brushed finish. Remove any dirt, grease, or old coatings before you begin. Sand down any rough patches or defects to create a smooth, even base for the brushing process.
Common Applications of Brushed Finish
Brushed finishes are commonly used in several industries to enhance both the appearance and texture of various products:
Home decoration
Brushed finishes are frequently applied to decorative elements in homes, such as door handles, cabinet handles, and wall cabinets. This process not only improves the visual appeal but also adds a sophisticated, modern touch to these functional items, making them stand out in interior design.
Electronic product
In the electronics industry, products like mobile phone cases, laptop covers, and other consumer electronics often feature a brushed finish. This technique enhances the product’s aesthetic by giving it a sleek, refined look while also offering durability and resistance to fingerprints, making the items more appealing and practical for everyday use.
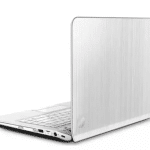
Automotive components
The brushed finish is widely used in automotive parts such as car wheels, door handles, windshield frames, and trim elements. The texture created by this finish gives these parts a high-quality, polished look while also providing resistance to wear and tear. It’s a popular choice for both functional and decorative elements in the automotive industry, helping to elevate the overall appearance of vehicles.
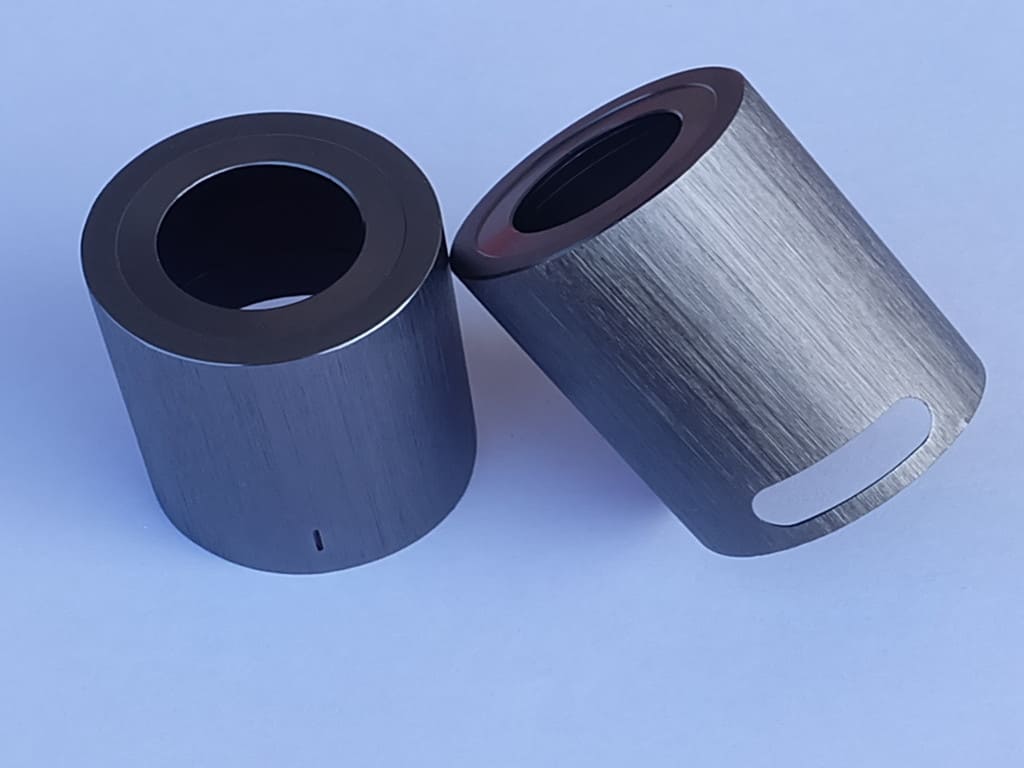
Conclusion
Brushing is a widely used surface finish for both metal and non-metal products. This unidirectional process uses abrasive brushes to create smooth, uniform metal surfaces. It is favored not only for its visual appeal but also for its practical benefits, such as improved durability and resistance to scratches.
As brushing requires precision, it’s recommended to consult with experts in the machining field to ensure the best results. At KUSLA , we specialize in custom plastic and metal parts and can assist with all your finishing needs. Contact us today for professional guidance and top-quality service!
FAQ
What is the difference between a brushed finish and a satin finish?
A satin finish features a smooth, low-sheen appearance, offering a soft, semi-reflective surface that is not too glossy. In contrast, a brushed finish involves creating visible linear or circular patterns by brushing or scrubbing the material with abrasive tools, resulting in a textured surface with more depth and visual interest. While both finishes are elegant, the brushed finish adds a distinctive texture, while the satin finish provides a more subtle, smooth look.
What type of machining process is most suitable for a brushing finish?
Brushing is most suitable for parts that have made by machining processes like milling, turning, or cutting, as it helps to remove surface imperfections and create a smooth, textured finish. However, it is not the best option for parts that need high corrosion resistance, as the brushing process can sometimes leave microabrasions that may make the material more vulnerable to corrosion over time.