Aluminum alloys are some of the most widely used materials in various industries due to their lightweight, durability, and resistance to corrosion. There are many different types of aluminum alloys with different names in the market. how do you know which one is suitable for your project? where are the differences between each type? how they are named? in this article, we will give you answers to these questions.
What Is Aluminum Alloy?
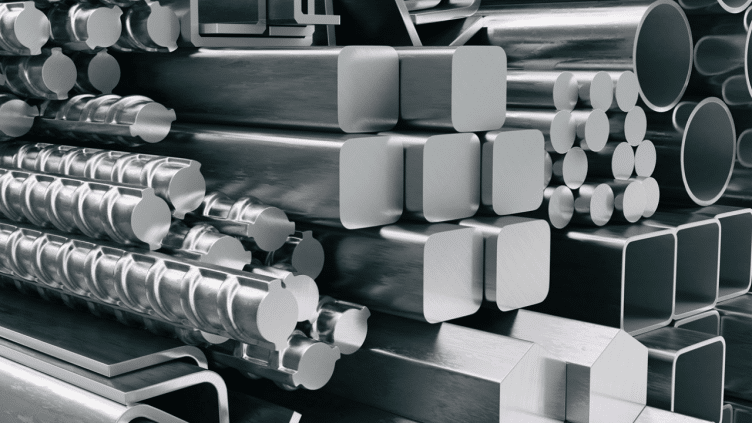
Aluminum alloys are mainly composed of pure aluminum, combined with other elements such as copper, silicon, magnesium, and zinc to improve their properties. With these elements, aluminum alloys can possess higher strength, excellent corrosion resistance, and good electrical and thermal conductivity.
Types Of Aluminum alloy
There are two main types of aluminum alloys: wrought and cast. These alloys are formed in different ways which greatly affects their properties. let’s check the details about these two types:
Wrought Aluminum Alloy
Wrought aluminum alloys have a big portion of all kinds of aluminum alloys. they are divided into heat-treatable and non-heat-treatable alloys. they contain Copper, magnesium, and zinc which provide their initial strength. Corresponding to series 2xxx, 6xxx, and 7xxx, Heat-treatable wrought aluminum alloys can be strengthened further through heat treatment. Non-heat treatable Aluminum Alloy corresponds to the 1xx, 3xx, and 5xx series of wrought alloys, it can be strengthened further through strain hardening or cold working.
Cast Aluminum Alloy
Aluminum alloys for die casting have several types like aluminum-silicon, aluminum-copper, aluminum-magnesium, aluminum-zinc, and more. The common grades for die-casting aluminum alloys are defined by the standards of Japan’s JIS and ANSI. The table below shows common die-casting grade series under various standards.
Casting aluminum alloy type | ANSI | SAE J452 | JIS | DIN | GB |
AI-Si-Mg | 360 | 309 | n/a | n/a | YL104 |
A360 | 309 | ADC3 | AlSi10Mg (Fe) | YL101 | |
AI-Si-Cu | A380 | 306 | ADC10 | AlSi8Cu3Fe | YL112 |
A383 | 383 | ADC12 | AlSi12(Cu) | YL113 | |
A384 | 303 | ADC14 | AlSi12 | YL116 | |
AI-Si | A413 | 305 | ADC6 | AlSi10Mg | YL102 |
C443 | 304 | ADC7 | n/a | n/a | |
AI-Mg | 518 | n/a | ADC5 | AIMg9 | YL302 |
How Aluminum Alloy is Named
When we see the name of aluminum alloys. You may wonder what number and letters means, such as 6061, 6061-T6, and 7075-T651. As below, we take an example of 6061-T6 to explain to you.
The first number “6″ represents the aluminum alloy group, and its detailed meaning as below:
Group Number | Meaning | Characteristic |
---|---|---|
1 | Industrial pure aluminum | Easy to form and highly machinable |
2 | Aluminum-copper series alloy | excellent machinability, less corrosion resistance |
3 | Aluminum-manganese series alloy | moderate strength and excellent workability |
4 | Aluminum-silicon series alloy | suitable for casting applications |
5 | Aluminum-magnesium series alloy | good strength and corrosion resistance |
6 | Aluminum-magnesium-silicon series alloy | moderate strength and excellent workability |
7 | Aluminum-zinc-magnesium-copper series alloy | high strength, but low machinability |
8 | Other alloys | |
9 | Reserved or for future use |
the second number “0” Indicates the control of alloying elements or impurities’ maximum content as below:
Second Digit | Meaning |
---|---|
0 | Original alloy, no special control over impurity max content |
1-9 | Modified alloy, special control over one or more individual impurities or alloying element max-content |
the number “61″ represents a kind of alloy within the same group.
The rest letters’ meanings are as below:
Temper Designation | Meaning |
---|---|
F | As-fabricated condition, suitable for products not requiring special hardening or heat treatment during the forming process |
O | Annealed condition, results in a material that is easier to machine, tougher, and more ductile; can be followed by a single-digit numeral except 0 |
H | Strain-hardened condition, for non-heat-treatable alloys where strength is increased by strain hardening |
W | Solution heat-treated condition, unstable and only applicable to alloys naturally aged at room temperature after solution heat treatment |
T | Heat-treated condition to a stable state, for heat-treatable alloys where the product reaches a stable state after heat treatment |
For example, “6061-T6” indicates an alloy from the aluminum-magnesium-silicon series that has undergone solution heat treatment and artificial aging to achieve a stable temper.
Key Benefits of Aluminum Alloys
There are many benefits of Aluminum Alloys when compare with other metals such as easy to machine, lightweight and many more. let us check all these key Benefits of aluminum:
Easy to machine
Aluminum alloys are relatively soft compared with other metals such as steel. This means aluminum is easy to cut with CNC bits and mold, resulting in aluminum parts with high precision and consistency.
Lightweight
Aluminum alloy’s density is 2.7 g/cm³, which is one-third the density of steel. This means it will be much lighter than steel. This is why aluminum alloy is widely used in applications that require lower weight, such as the automotive industry.
Corrosion Resistance
Aluminum can form a thin protective oxide layer on its surface naturally, This protective aluminium oxide layer helps protect the surface of the aluminum part from corrosion.
Electrical and Thermal Conductivity
Aluminum alloy is an excellent conductor of heat and electricity. Its conductivity is much better than steel and other metals, but not as good as copper. Aluminum alloys are commonly used as heatsinks in a variety of applications to conduct heat.
Strength-To-Weight Ratio
Even though aluminum alloy is lightweight, it still provides excellent strength and structural integrity. In applications where strength and weight need to be balanced, aluminum alloy is a perfect choice.
Recyclability
Aluminum is 100% recyclable, and it can retain all of its original properties after recycling. In this case, aluminum is a much more cost-effective source material for production with the use of recycled aluminum.
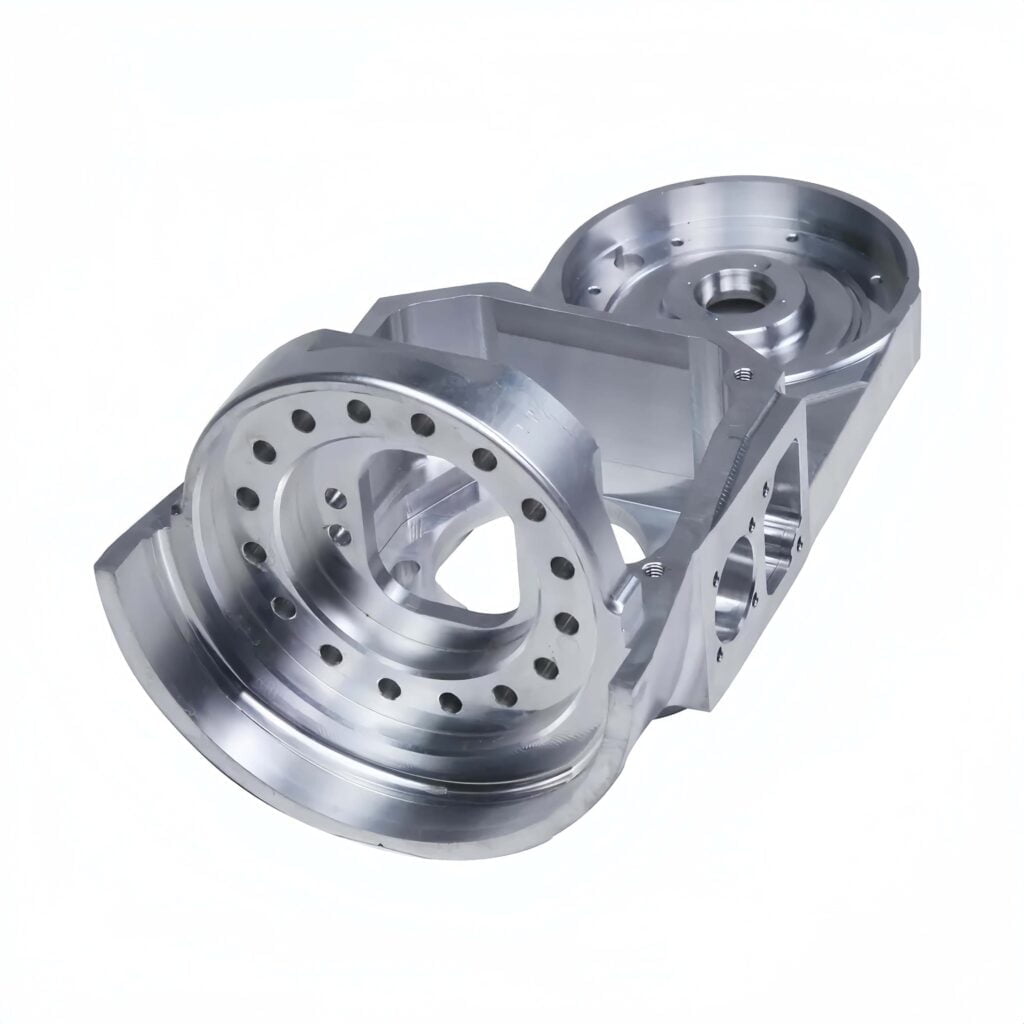
Different Grades Of Aluminum Alloys
Seven different series aluminum alloys are available for industrial use, ranging from 1xxx to 7xxx. Each alloy has a unique digit combination with varying proportions of alloying elements. here we go through these series one by one:
1xxx Series
The 1xxx series is made of 99% pure aluminum, with small amounts of silicon and iron. This type of aluminum is very flexible and easy to shape, making it useful in electrical and chemical industries. It has great resistance to corrosion and is also easy to work with, though it isn’t as strong as other aluminum types. Due to the high heat and electrical conductivity, this series is widely used in electrical products like aluminum bus bars and heat sinks.
2xxx Series
This series mainly uses copper as the alloying element, so it’s often called “copper alloy.” This series is known for excellent machinability and, when heat-treated, can be as strong or stronger than mild steel. Although it has high strength and good workability, it lacks in corrosion resistance, weldability, and brazing ability. Because of this, cladding is sometimes added to improve durability. The 2xxx series, especially the 2024-T351 alloy, is popular in the aerospace industry, commonly used for home-built aircraft parts.
3xxx Series
The 3xxx series uses manganese as the main alloying element, giving it excellent formability. These alloys are typically not heat-treated and are commonly used for general purposes where good workability and moderate strength are needed.
4xxx Series
The 4xxx series uses silicon as the main alloying element, which lowers the melting point without making the material brittle. This makes them ideal for welding wire. These alloys also turn dark grey when anodized, which makes them popular in various architectural applications.
5xxx Series
The 5xxx series is mainly made of magnesium and manganese. These alloys are known for being strong, easy to shape, and highly resistant to corrosion. They are commonly used in bridges, transportation projects, and the marine industry.
6xxx Series
The 6xxx series is one of the most versatile aluminum alloys. It mainly includes silicon and magnesium as alloying elements. These heat-treated alloys offer good formability, corrosion resistance, and medium strength. One of the most popular alloys in this series is 6061, which comes in sheet, plate, and extrusion forms. Due to its versatility, 6061 and other 6000 series alloys are used in a wide range of applications, including architectural products, piping, electrical components, and consumer goods.
7xxx Series
Strength is the key feature of the 7xxx series. The main alloying elements are zinc, copper, chromium, and magnesium, which give these alloys very high strength but make them harder to machine. Due to its strength, the 7xxx series is often used for making molds and CNC machined parts used in a wide range of industries, including automotive, aerospace, marine, and machinery manufacturing.
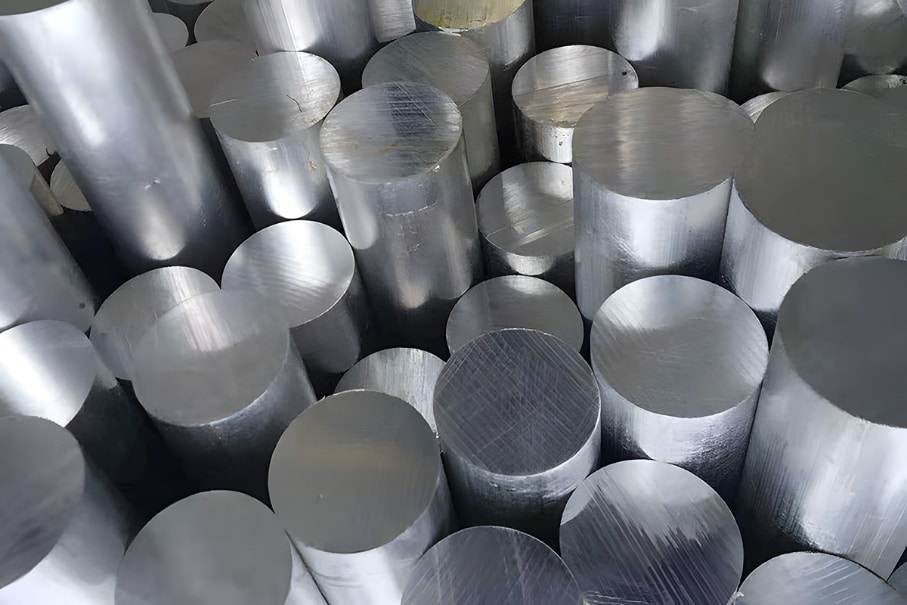
Best aluminum alloy for machining
Based on our extensive experience, this section provides a introduction of the best types of aluminum alloys to consider when machining your products.
6061: This aluminum alloy is widely used for its excellent machinability, corrosion resistance, and weldability. It’s a heat-treatable alloy that is relatively flexible and easy to work with. With strong durability and the ability to handle high temperatures, 6061 is perfect for components exposed to heat.
2024: Known for its great machinability and strength, 2024 is another popular aluminum alloy. Commonly used in aerospace, especially for airplane wings, 2024 offers high strength and excellent resistance to corrosion.
7075: This is the strongest of the three alloys and is used for applications requiring a high strength-to-weight ratio. It’s commonly found in aerospace, military, and recreational products. However, 7075 is harder to machine than 6061 and 2024 due to its superior strength and toughness.
Properties of Aluminum Alloys
Depending on the alloying element and specific composition, aluminum alloys have different physical and chemical properties. Here we summarize a table below to show the physical properties of common aluminum alloys, so then you can understand the performance of each aluminum alloy. you can find more complete properties on https://www.matweb.com/
Alloy | Yield Strength (MPa) | Elongation at Break (%) | Hardness (Brinell) | Density (g/cm³) | Maximum Temp (°C) |
---|---|---|---|---|---|
Aluminum 1110 | 25-30 | 35-40 | 23 | 2.71 | 250 |
Aluminum 2011 | 290 | 10 | 95 | 2.82 | 120 |
Aluminum 2024 | 325-470 | 10-25 | 120-130 | 2.78 | 150 |
Aluminum 3003 | 110-130 | 20-25 | 40 | 2.73 | 260 |
Aluminum 5052 | 170-215 | 12-20 | 60 | 2.68 | 200 |
Aluminum 6061 | 240-310 | 12-25 | 95 | 2.70 | 250-300 |
Aluminum 6063 | 110-180 | 12-20 | 60 | 2.69 | 200 |
Aluminum 7050 | 460-510 | 10-14 | 150 | 2.81 | 150 |
Choose the right Aluminum alloy type: Key considerations
Before you choose aluminum, you will need to consider your machined parts requirement and the machining process you will use. some of the general considerations are as below:
Strength
From the overview of each aluminum alloy mentioned above, you can see the varying strength properties of each. Among them, aluminum 7075 stands out as the strongest, offering exceptional tensile strength and resistance to stress. So, When strength is a top priority in your project, 7075 is often the go-to choice.
Corrosion Resistance
Corrosion resistance is a critical factor to consider based on the environment in which your aluminum components will be exposed. Different aluminum alloys offer varying levels of resistance to corrosion, which can impact their longevity and performance. For example, alloys like 5052 and 6061 are known for their excellent corrosion resistance, making them widely used in marine or coastal areas with harsh environments.
Weldability
Not all aluminum alloys are well-suited for welding, as their composition and properties can impact weldability. If your project involves welding, it’s crucial to choose an aluminum grade specifically designed to handle the process effectively. For instance, aluminum 6061 is a popular choice due to its excellent weldability and balanced mechanical properties.
Machinability
The machinability of an aluminum alloy indicates how well the material performs in CNC machining processes. Notably, alloys such as 6061-T6, 2011 aluminum, and 7075 aluminum are good options with excellent machinability and are widely used for creating complex parts with intricate designs and requirements.
Tips for machining aluminum alloys
Here, at Kusla, we share some tips to help you optimize your machining operations when working with aluminum alloys. let us explore these tips:
Use Sharp Tools: Aluminum can be tough to process, so it’s important to use sharp, precise cutting tools. Dull tools can cause the aluminum to stick to the tool, which leads to poor surface finish and quicker tool wear.
Set the Right Speeds and Feeds: Aluminum requires higher cutting speeds and slower feed rates than other materials. Make sure to follow the recommended speeds and feeds for the specific aluminum alloy you’re working with.
Use Coolant: Using coolant while machining aluminum helps prevent heat buildup and improves the surface finish. Choose a water-soluble lubricant that’s suitable for aluminum.
Avoid Work Hardening: Aluminum can harden during CNC machining, making it harder to cut. To prevent this, use light cuts and take breaks to let the material cool and settle.
Conclusion
Aluminum is a commonly used metallic material with versatile properties depending on the element composition. Several types of aluminum alloys have varying properties, making them well-suited for different applications. Thus, it is essential to fully comprehend the differences in these aluminum alloys to choose the ideal material for your projects. KUSLA has rich experiences in aluminum machining services that can help you with your projects. contact us today to get an instant quotation.
FAQ
What is the most common aluminum alloy sheet?
Generally, 3003 aluminum is the well-known and most widely used of the common alloys in the market.
Which aluminum alloy has better machinability between 6061 and 7075?
Generally speaking, in most applications, 6061 aluminum alloy is better than 7075 aluminum when considering their fabrication process. This is because 6061 has lower hardness and tensile strength, and more easier to machine than 7075.