In our daily lives, ABS plastic material is all around us, even if we don’t always notice it. It’s used in products like phone cases, car bumpers, kitchen appliances, power tool housings, and even bathroom plumbing. In the world of manufacturing and prototyping, ABS is a go-to material. This article will explore what ABS is and the rapid prototyping processes that work well with it.
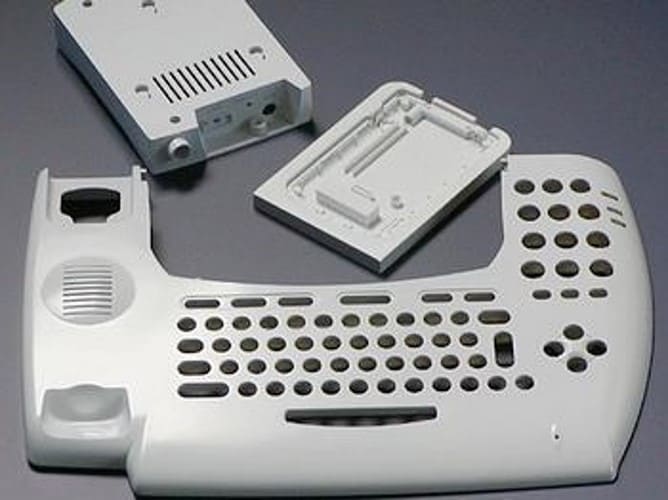
What Is ABS Plastic Material?
ABS stands for Acrylonitrile Butadiene Styrene. It’s a type of thermoplastic, known for its durability and impact resistance. It’s made from three main ingredients as below which give ABS its strength, impact resistance, and versatility:
- Acrylonitrile: Made from propylene and ammonia, it makes ABS strong and heat-resistant.
- Butadiene: A by-product of making ethylene, this ingredient adds toughness and flexibility to ABS.
- Styrene: Made from ethylbenzene, styrene gives ABS its rigid structure and makes it easy to shape into different forms.
Properties of ABS Material
ABS plastic is widely used in many industries and works well with various manufacturing and rapid prototyping processes because of its strong properties. Let’s explore why:
Strength and Impact Resistance
ABS plastic is known for its strong impact resistance, meaning it can handle sudden and intense force without breaking. Compared to other materials like acrylic, ABS is less likely to crack or break during daily use.
Abrasion Resistance
ABS plastic has excellent abrasion resistance, meaning it can endure wear and tear from friction without getting damaged easily. It maintains its appearance and durability even with repeated use.
Easy to Machine
ABS plastic is easy to machine, meaning it can be easily cut, milled, and injected into different shapes. Compared to other materials, ABS is simpler to work with and allows for high-quality products to be made with less effort. The lower scrap rate means less material waste, which results in cost savings. This is one of the reasons why ABS is commonly used in many manufacturing processes.
Excellent Insulator
Like most plastics, ABS is an excellent insulator and a poor conductor of heat. Combined with its impact and abrasion resistance, this makes ABS widely used in electronic housings, where durability, heat control, and protection from impact are crucial.
Chemical Resistance
ABS is highly resistant to chemicals, making it suitable for use in environments that contain alcohols, hydrocarbons, and other chemicals. This property gives ABS greater durability compared to many other materials in everyday life. For example, it is commonly used in products like shampoo bottles, bathroom accessories, and other items that may come into contact with various chemicals.
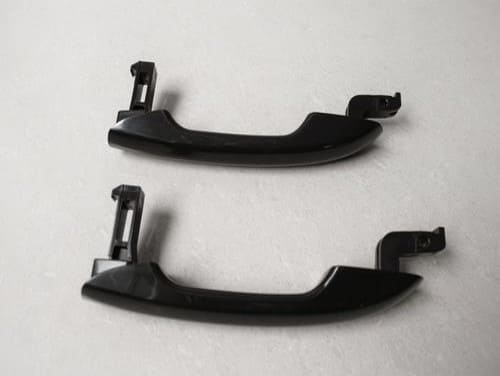
What is an ABS Prototype?
An ABS prototype is an early model of a product made from ABS material before mass production begins. It is created using rapid prototyping techniques such as CNC machining, 3D printing, and others. These prototypes are used for display, testing, and validating the design concept. Compared to other materials, ABS prototypes are easier to make and more affordable due to their high machinability.
ABS material grades for rapid prototyping
There are different grades of ABS materials used in plastic prototyping and part manufacturing. Here are some common grades:
ABS Extrusion Grade
This is a common type of ABS, known for its flexibility and strength. It works well for plastic prototyping because it’s strong and elastic. This grade is manufactured through an extrusion process or CNC machining on the ABS extruded sheet.
ABS Injection Molding Grade
This grade is designed for products made by injection molding. It has high impact resistance, making it suitable for use in plastic prototyping processes such as prototype injection molding.
ABS Flame Retardant Grade
Flame Retardant ABS is used where heat and flame resistance are important, such as in the cases of electronic devices. It’s made by adding flame-resistant materials to standard ABS. This grade can be used in both molding and extrusion processes.
ABS High Impact Grade
This grade of ABS is stronger and tougher than standard ABS. It’s commonly used in products that need high-impact resistance, like toys and car parts.
Other ABS Grades
There are also special ABS grades mixed with other materials to enhance their strength. Examples include ABS combined with glass fiber or stainless-steel fiber for added durability.
Types of ABS Rapid Prototyping Processes
There are several methods to create ABS prototypes. Let’s explore these processes:
CNC machining
CNC machining works by using a computer-controlled machine to remove material from extruded sheets to shape it. Common CNC machining techniques include milling and turning. ABS prototypes made through this method offer high precision compared to other processes.
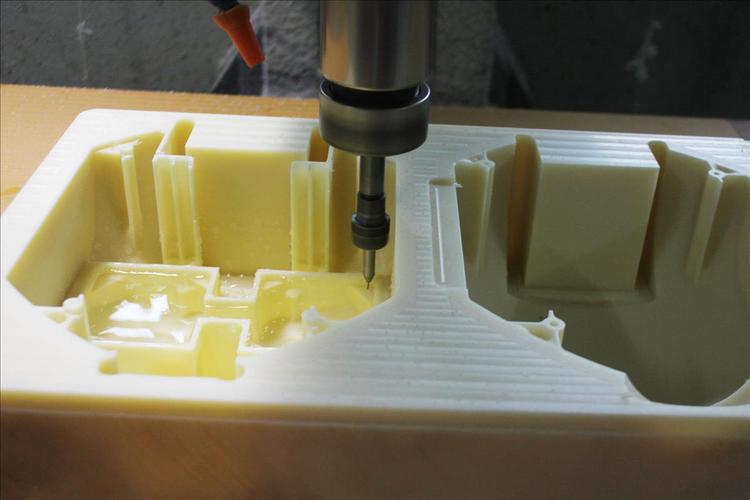
3D Printing
3D printing is a process that builds 3D parts layer by layer using a 3D printer and a CAD (Computer-Aided Design) model. The most common method for printing ABS plastic is Fused Deposition Modeling (FDM), which is often followed by additional steps to improve the part’s appearance and functionality.
Prototype injection molding
Injection molding is a popular method for making ABS prototypes. It works by melting ABS plastic and injecting it into a mold. Once cooled, the plastic hardens into the mold’s shape. Molds are usually made from CNC-machined aluminum or steel, but 3D-printed molds can also be used depending on the part’s complexity and quantity needed.
Urethane casting
ABS-like urethane is one of the most widely used materials for creating ABS prototypes through the urethane casting process. In this process, a master model is made, and then a flexible mold is created to cast parts from urethane that closely resemble ABS. This method is perfect for low-volume production and is more cost-effective than prototype injection molding. However, it typically offers slightly less accuracy compared to other methods like CNC machining or 3D printing.
Why ABS is Ideal for Rapid Prototyping?
Rapid prototyping requires materials that are easy to work with, fast to produce, and low in cost. Since there is often a lot of manual work involved in the prototyping process, ABS material is an excellent choice. Let’s look at the key benefits of using ABS for rapid prototyping:
Easy for Prototyping
Prototypes often require several manual steps, such as sanding, polishing, filing, drilling, painting, and bonding, to achieve a smooth, clean finish. ABS is well-suited for these tasks due to its ease of machining.
Low Cost
ABS prototypes are cost-effective, making them a popular choice among engineers for plastic prototypes. This is because ABS is widely used in mass production, which drives down the cost compared to other materials.
Surface Finish
Compared to other materials, ABS prototypes can achieve a smooth surface finish. This gives the prototype a clean and polished look, which is closer to the final product that will be produced in mass manufacturing.
Impact and Abrasion Resistance
As mentioned, ABS has good impact resistance, which makes it durable during the manual work involved in rapid prototyping. This is particularly important for parts that will be handled or touched frequently during the prototyping process.
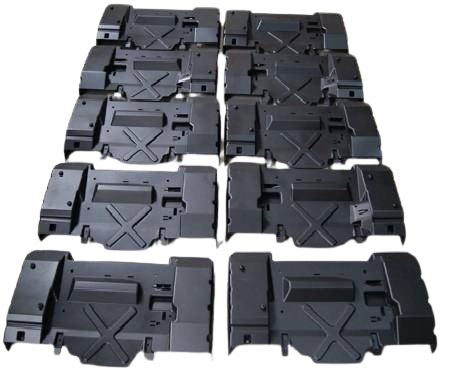
Applications of ABS prototypes
Various industries rely on ABS prototypes to validate designs or for low-volume production. Here are some common industries that use ABS materials for prototyping:
Automotive parts
ABS materials can be used for hand-panel prototypes of automotive parts, such as dashboards, doorknobs, and more. These prototypes help engineers assess the feasibility of a design before actual production
Electronic product housing
The housings of mobile phones, tablets, and laptops commonly use ABS materials for prototyping. This is because ABS prototypes offer good dimensional stability and impact resistance.
Medical devices
ABS prototypes play an important role in the design verification of medical devices, such as surgical tools, diagnostic equipment, ventilators, and more.
Toys
The toughness of ABS material makes it an ideal choice for making toy prototypes, such as remote-controlled cars, robot models, etc.,
How to Choose the right ABS Material for prototyping
To choose the right material for your project needs, you must understand the prototyping process you want to use and the properties of the ABS material.
Prototyping Process
There are many prototyping processes you can use with ABS material. The most common ones include 3D printing and Injection molding. Different rapid prototyping process requires a particular grade of ABS material. Therefore, you have to know the different grades available before choosing the right one.
Machinability
Another important factor to consider is the machinability of ABS. Each grade of ABS plastic has its own machinability coefficient, which determines how well it performs in different manufacturing processes. Using the wrong grade of ABS can cause issues during production. For instance, choosing the wrong ABS type for 3D printing may result in warping problems, impacting the quality of the final prototype.
Conclusion
After reading this article, you will understand the ABS material’s properties, grades, advantages, and applications, and also the processes of creating ABS prototypes. KUSLA is a rapid prototyping factory that is capable of making high-quality ABS prototypes with all these processes and helps you find a low-cost way to meet your project requirements. contact us now if you have any ABS prototypes projects.
FAQ
What is the best way to make an ABS prototype?
The most popular way to create ABS prototypes is through 3D printing. This method offers a low cost and fast lead time, making it ideal for rapid prototyping and iterative design processes.
Which is better ABS or PLA?
ABS is generally stronger and more durable than PLA, making it the preferred choice for engineers when ductility and impact resistance are important. PLA, on the other hand, is easier to print and more environmentally friendly but is less suited for applications requiring strength and flexibility.
What Is ABS Material Used For?
ABS (Acrylonitrile Butadiene Styrene) material is a type of plastic often used in rapid prototyping methods like 3D printing and injection molding. It’s popular because it’s affordable and easy for manufacturers to work with.