Acrylic is a clear plastic used in many different applications, such as signs, displays, and other commercial products. It’s a popular substitute for glass because it’s lighter, stronger, and more durable. Acrylic fabrication involves various methods to shape acrylic plastic into products used in our daily lives. However, do you know why acrylic is so widely used and how it can be fabricated into products? In this article, we’ll explain everything you need to know about acrylic and acrylic fabrication, including its methods and applications. Let’s get started.
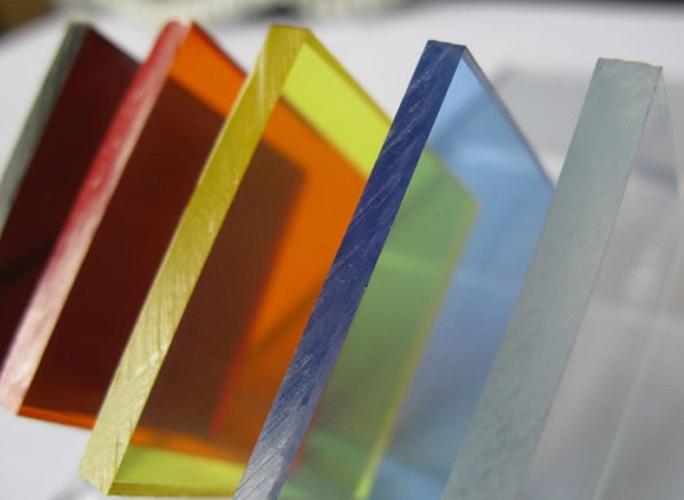
Introduction to Acrylic plastic Material
Acrylic plastic was first made in 1928 and sold by the Rohm and Haas Company around 1933. It is also called Plexiglass and is a flexible plastic material used for many different things. Acrylic comes in many colors and levels of transparency. Its chemical name is Poly (methyl methacrylate), and it is a clear, lightweight plastic that is stronger and more durable than glass.
Today, acrylic is mainly sold in plastic particles and sheets of different thicknesses. Acrylic sheets are easy to shape, stick well with adhesives and solvents, and can be heated to form new shapes. No matter what you need it for, acrylic is an affordable and long-lasting material. It is also better at handling weathering than many other clear plastics.
What is Acrylic Fabrication?
Acrylic fabrication is the process of shaping acrylic sheets or pellets to create various products. The process includes methods such as cutting, bending, machining, forming, and finishing, using different tools and techniques. It’s a versatile process where a wide variety of acrylic products are made.
Benefits of Using Acrylic in Fabrication
Acrylic’s unique combination of durability, clarity, weather resistance, and ease of fabrication makes it an excellent choice for many plastic fabrication projects. Whether you need strength, transparency, or customization, acrylic is a material that can meet a wide range of needs across various industries. Let’s take a look at the top reasons why acrylic is so popular in plastic fabrication:
High Transparency
Acrylic is very clear, allowing up to 92% of light to pass through. Due to this outstanding property, acrylic is widely used for display cases, battery covers, and pipes that need regular checks. Its transparency helps you see the components clearly and keep them in good condition.
Exceptional Durability
Acrylic is strong and tough. It is more resistant to impact and pressure than glass, so it won’t break easily. Therefore, for products like storage tanks, machine guards, and air ducts, acrylic is a good choice.
Lightweight
Acrylic is lightweight, which makes it easy to carry, move, and install. This is especially helpful when weight is a concern, such as in displays or signs.
Resistance to UV
Acrylic is highly resistant to UV rays. It does not turn yellow or cloudy when exposed to sunlight and can stand up to harsh weather, like rain and hail.
Easy to Fabricate
Acrylic is simple to work with, which is why manufacturers like using it. It can be cut, shaped, and molded into many different forms with special tools.
Cost-Effectiveness
Acrylic is cheaper than other materials like glass or polycarbonate, providing a more affordable option for many uses. It is also easy to replace if damaged, saving money on repairs.
Recyclability
Acrylic is recyclable, making it an environmentally friendly choice. It can be reused to create new products, helping to reduce waste and support a circular economy.
Methods of Acrylic Fabrication
Acrylic fabrication involves the methods used to shape and form unprocessed acrylic into desired products. Let’s take a look at the processes used in acrylic fabrication.
Extrusion
Acrylic extrusion is a process where acrylic particles are pushed through a mold or die with a specific shape. The extruded acrylic sheets can then be further machined to create the final parts. The extrusion process can also produce acrylic products with a fixed cross-sectional profile, such as acrylic tubes, rods, films, and profiles.
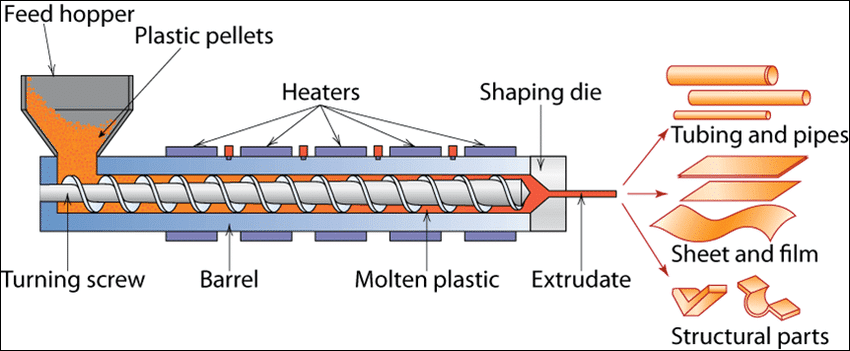
Casting
Acrylic sheets can also be made by casting. This process involves pouring molten acrylic pellets into a mold, allowing it to cure for a few hours until it becomes semi-solid, and then removing it from the mold. Heat and pressure are used to force air bubbles out of the acrylic sheet. These cast acrylic sheets can then be further machined to create the final parts. Generally, cast acrylic sheets are easier to machine than extruded acrylic.
Injection molding
Injection molding acrylic is a very common method to create large-scale acrylic products when the product shape is complex. this process uses an injection machine to inject molten acrylic pellet material into a mold with high pressure, and then the acrylic material cools and cures in the mold to form the final product. it creates acrylic products directly from the acrylic particles.
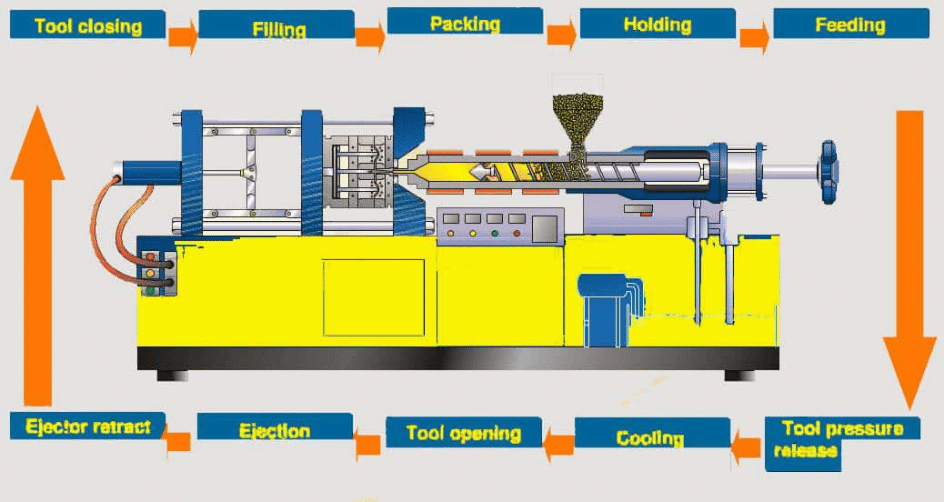
Cutting
Acrylic sheets can be cut to create products like acrylic displays, signs, and more. One common method for cutting acrylic sheets is laser cutting. The advantage of this method is its ability to handle acrylic slabs of any size. The laser cuts the material quickly and precisely, shaping it to the exact dimensions and design specified by the customer.
Bending
Some products, such as signage, displays, and stands, are made by bending acrylic sheets. Acrylic can be bent by heating it to around 160 degrees Celsius, which softens the material without causing any discoloration. There are several methods for bending acrylic sheets, each suited to different applications. One common method is using a line bender, which allows for controlled bending along a specific line, ensuring a consistent angle.
CNC machining
CNC machining acrylic is commonly used for prototyping, allowing manufacturers to create high-quality acrylic prototypes with excellent precision. Acrylic CNC machining offers a level of accuracy comparable to injection molding, while also taking advantage of the material’s unique properties, such as its optical clarity, UV stability, and impact resistance. Several CNC machining processes can be applied to acrylic sheets, including CNC milling, turning, and drilling.
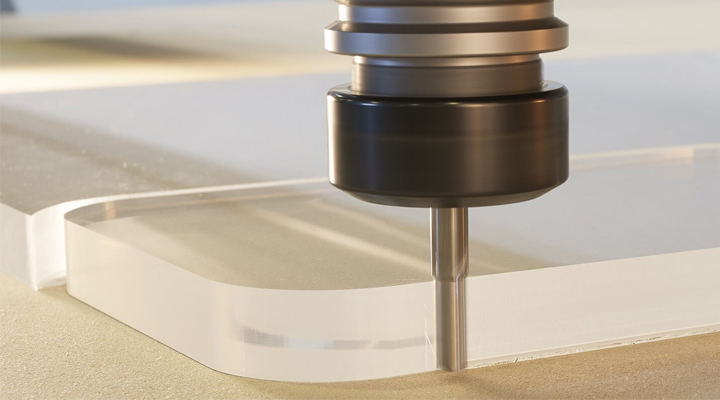
Thermoforming
Thermoforming acrylic is commonly used for packaging consumer goods and creating large, customized products such as acrylic trays and acrylic boxes. This process involves heating a thin acrylic sheet until it becomes soft and pliable, then molding it into a specific shape by pressing or vacuuming the material into a mold. There are three main types of thermoforming acrylic processes: Drape Forming, Pressure Forming, and Vacuum Forming. Each method is designed to meet different application needs, depending on the complexity of the shape, the level of detail required, and the desired finish of the final product.

Common Applications of Acrylic Fabrication
Acrylic fabrication creates acrylic products that are ideal for many home, industrial, and commercial applications due to their clarity, strength, and resistance to impact, sunlight, and extreme temperatures. Here are some common uses:
- Signage and Displays
- Architectural products
- Clear Fixtures
- Furniture product
- Automotive lenses
- Windows
- Acrylic architectural glazing
- Exhibition and display solutions
- Acrylic transparent barriers
Conclusion
Acrylic has many benefits that make it a better choice than other plastics. Knowing why acrylic is used in both industries and homes, as well as acrylic fabrication process, can help you choose the right acrylic products. If you’re planning an acrylic project, contact KUSLA today. Our team is ready to help you design and create high-quality acrylic product.
FAQs
Can I cut acrylic myself?
Yes, you can cut acrylic yourself with the right tools and techniques. For thin acrylic sheets, a scoring blade or utility knife can be used. To cut, score along the desired line, then snap the sheet along the score. For thicker acrylic sheets, a table saw, jigsaw, or circular saw with a fine-toothed blade is recommended. Make sure to set the saw to a slow speed and use a blade specifically designed for plastic to avoid cracking or chipping. Additionally, always wear protective gear such as safety goggles and a dust mask to ensure safety while cutting acrylic.
What machine do you use to cut acrylic?
To cut acrylic, you can use a few different machines, including a laser cutter, CNC router, table saw, jigsaw, or circular saw. The choice depends on the thickness of the acrylic and the precision needed. For clean and precise cuts, a laser cutter or CNC router is often the best option..
Is Acrylic Easy to Machine?
Yes, acrylic is easy to machine and can be machined with different methods and tools such as cutting, bending, milling, turning, and more. Cast acrylic is generally easier to machined than extruded acrylic because Casting creates less internal stresses, so cast acrylic is less brittle than extruded acrylic.