Polyurethane manufacturing started to grow in the 1950s because urethane can be used in many ways. Manufactures mix it with nylon to make it stretchy, used polyurethane foam for insulation, and figured out how to make urethanes work as adhesives. Today, urethanes are used in many different products and industries. They come in different forms and can be customized to fit specific needs. In this article, we will explain what urethane is and how it can be used in various industries.
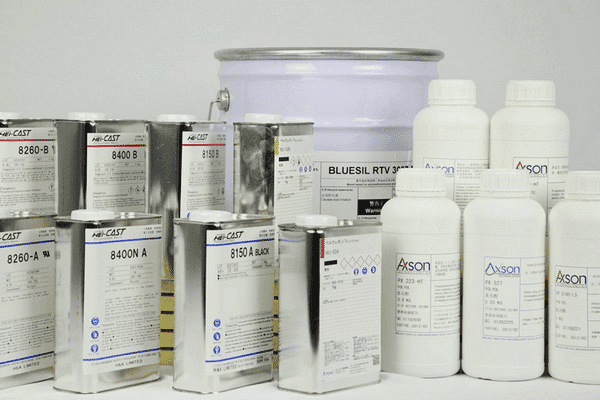
What is Urethane?
Urethane is an organic compound. Depending on the production process and the degree of cross-linking, urethane can exhibit the properties of either plastic or rubber. It is commonly used in solid foam or liquid form and can be processed to make plastics, rubber, foam, fibers, coatings, adhesives, and functional polymers.
What is the difference between Polyurethane and urethane?
The answer is that urethane and polyurethane are the same thing. Polyurethane is a polymer made up of repeating units chemically linked in a specific pattern, some of which are urethane groups. The term polyurethane refers to a polymer that contains multiple urethane groups.
Properties of Urethane
The chemical formula for urethane is C₃H₇NO₂. Below, we explain some of the main properties that make urethane an excellent choice for many industries:
Hardness
The hardness of urethane is measured on the Shore scale, which can range from 20 Shore A (as soft as rubber) up to 85 Shore D (as hard as typical thermoplastics like polycarbonate). This wide range of hardness allows urethane to be used in applications ranging from soft rubber to hard plastic. Below is a hardness scale chart for better understanding.
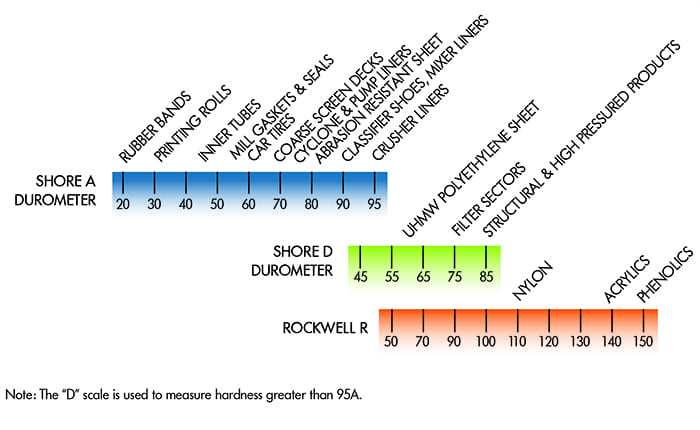
Abrasion resistance
Urethane is well known for its exceptional resistance to abrasive and erosive damage, making it an excellent choice for applications where severe wear is a concern. For example, urethane rubber has ten times higher abrasion resistance than other elastomers.
Chemical resistance
Another important property of urethane is its chemical resistance. It is resistant to many chemicals, including oils, solvents, fuels, and aggressive substances. This makes it widely used in industries that require chemical resistance and can withstand harsh environments.
Compression set
Urethane has high load-bearing capabilities. Products made of urethane can handle more stress without failing than most other materials, making it ideal for applications requiring compressive resistance, such as fall-arrest dampers in elevators and railway line stops.
Tear Strength
Urethanes have excellent tear strength and can resist tears or punctures that occur when removing urethane parts from molds, due to the pulling force required to break the tension between the mold and the cast part. Higher tear strength helps prevent the mold from tearing, allowing for easier part removal and a longer-lasting mold. This makes urethane casting a cost-effective solution for producing multiple parts using silicone molds.
Tensile Strength
Tensile strength is the maximum stress that a material can withstand while being stretched or pulled before failing. While urethane elastomer is not typically used in tensile applications due to its high elongation and creep, it still offers good tensile strength.
Types of Urethane
There are two main types of urethane: polyester urethane and polyether urethane. Within the polyester and polyether groups, the most common types include TDI (toluene diisocyanate) polyester, MDI (methylene diisocyanate) polyester, MDI polyether, TDI polyether, NDI (naphthalene diisocyanate) polyester, and TDI polycaprolactone.
- TDI Polyester: Excellent abrasion and chemical resistance, commonly with hardness ranging from 70A to 70D.
- MDI Polyester: FDA grade for use with food, commonly with hardness ranging from 85A to 95A.
- TDI PTMEG Polyether: Good low-temperature flexibility and resistance to microbial growth, commonly with hardness ranging from 90A to 70D.
- MDI PTMEG Polyether: Outstanding dynamic properties and high resilience, commonly with hardness ranging from 60A to 95A.
- NDI Polyester: An advanced urethane type offering some of the best load-bearing capacity, commonly with hardness ranging from 65A to 60D.
- TDI Polycaprolactone: Good dynamic properties and better hydrolysis resistance, commonly with hardness ranging from 60A to 55D.
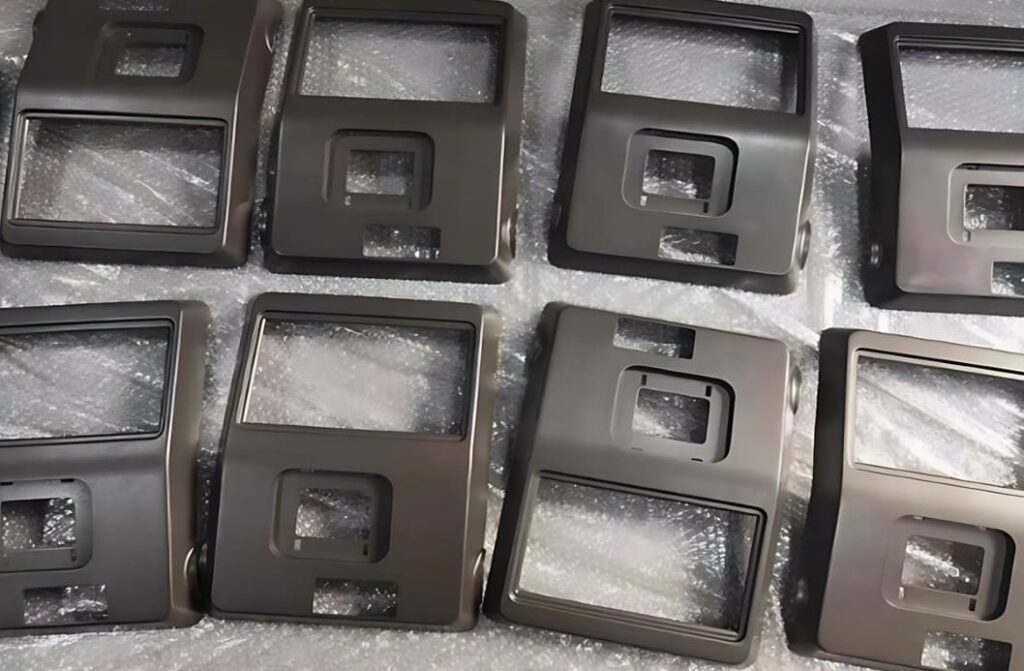
Advantage of Urethane
Urethane has many advantages compared to other plastics, making it widely used in various industries. Below, we explain the key benefits of urethane:
Durability
Due to its excellent chemical and abrasion resistance, urethane parts are durable when used in harsh environments and under heavy load conditions. This makes it ideal for applications such as automotive parts, flooring, and heavy machinery.
Flexibility
Urethane elastomers can be bent, stretched, and return to their original shape without losing integrity. This makes it a perfect choice for products that require both elasticity and strength, such as watch straps.
Cost-effective
Urethane is a relatively low-cost material compared to other plastics and rubbers. This means urethane parts can be produced in large quantities at a low cost.
Customizable
Urethane can be easily customized to meet the material property needs of different applications. This is because urethane can be manufactured in a wide range of colors, hardness levels, and forms with additives. Additionally, you can mix ingredients to achieve the properties you need.
Manufacturing Processes using Urethane
There are different methods for creating your product in the urethane manufacturing process, including open-cast molding, spin casting, extrusion, injection molding, and compression molding.
Open cast molding
Open-cast molding is widely used for urethane casting parts in the market. It starts with liquid polyurethane, which is poured into an open silicone mold. The mold and urethane liquid are then heated to cure and finalize the product.
Spin casting
Spin casting is a process that involves using a spinning mold to cure liquid polyurethane into a solid part. As the mold rotates at high speed, the centrifugal force forces the liquid polyurethane to spread evenly, and the air inside the mold is removed, ensuring a smooth and uniform casting.
Extrusion
Urethanes can be melted and formed into different shapes through the extrusion process. This method is commonly used for making tubes, films, and other products from urethane materials
Injection molding
Liquid urethane can be injected into a mold using the low-pressure injection molding process, where it is carefully introduced to form the final product. The mold is designed with small openings that allow air to escape gradually, preventing air pockets and ensuring a smooth, high-quality casting
Compression molding
Compression molding uses both heat and pressure to cure the liquid urethane material, which is poured into a compression mold. This process allows the material to take the shape of the mold, resulting in a solid, durable part.
What is Urethane Used for?
Urethane is a highly versatile compound with a wide range of applications. It is most commonly used in liquid form as a coating, adhesive, sealant, pesticide, fungicide, and more. Here, we will look at its uses in more detail:
- Coating: Urethane can provide a protective layer as a coating, enhancing the durability and appearance of surfaces. It helps protect parts from scratches, dents, and weather damage.
- Adhesive: Urethane is an excellent material for making adhesives with strong bonding properties. Urethane adhesives are used in various applications to bond materials like wood, metal, and plastic.
- Sealant: Urethane is resistant to water, oil, and oxidation, making it ideal for creating sealants that provide durable, flexible seals.
- Pesticides and Fungicides: Urethane compounds are used as pesticides and fungicides to help protect crops from pests and diseases.
- Plastics: Urethane can be used to produce plastics through processes like tube extrusion and cast molding. It offers flexibility, durability, and resistance to wear and tear.
- Textiles: Urethane is used to make synthetic fibers and coatings in the textile industry. These fabrics are lightweight, breathable, and easy to maintain.
- Dyes: Urethane is used in the dye industry to help the dye adhere to fabric, ensuring that the colors remain vibrant and long-lasting.
- Solvent: Urethane can act as a solvent in various chemical processes, helping dissolve other substances and making it easier to mix and apply different chemical formulations.
- Insulation: Urethane is commonly used as insulation, helping to reduce energy consumption by keeping interiors warm in winter and cool in summer. It is a popular choice for insulating homes and buildings.
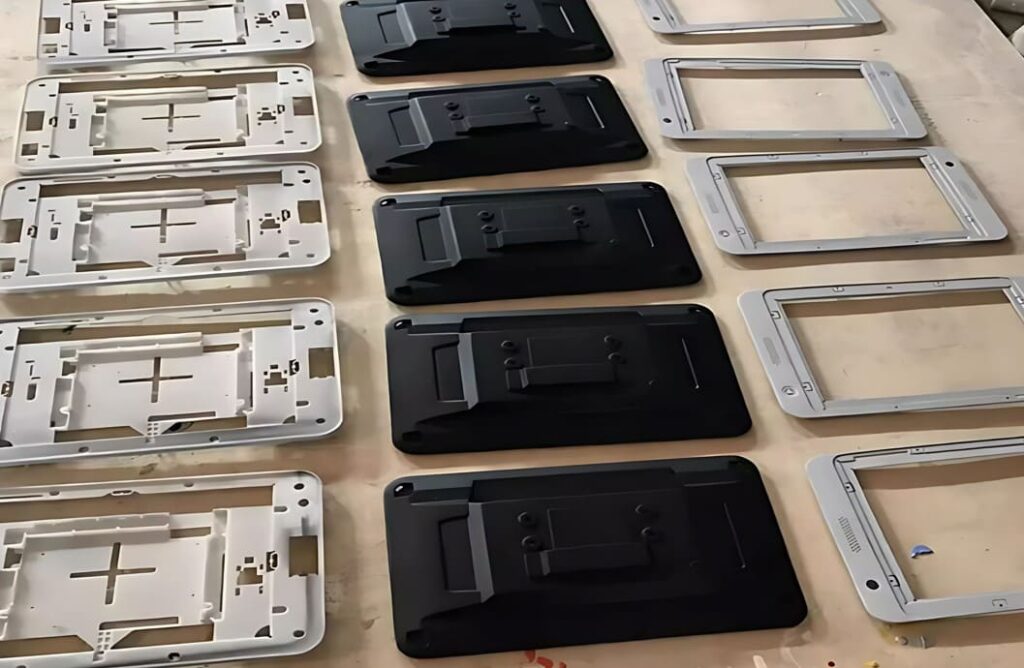
Industry Applications of Urethane Materials
Urethane materials are widely used in many industries. Here, we list some of the main applications that benefit from their use.
Automotive industry
Urethane is widely used in the automotive industry for a variety of applications, including foam and plastic components in car parts. It plays a crucial role in the production of seats, car bodies, headlights, bumpers, spoilers, doors, and windows, offering benefits such as enhanced durability, flexibility, and impact resistance
Furniture
Urethane is commonly used in the furniture industry, especially for cushioning in sofas, chairs, and mattresses. Flexible urethane foam provides both comfort and support, offering a balance of softness and durability. It is lightweight, resilient, and long-lasting, making it an ideal material for furniture that requires both comfort and structural integrity.
Packaging
Urethane foam is widely used in the packaging industry to protect delicate items during shipping. Its excellent shock-absorbing properties, combined with its ability to be custom-molded, make it an ideal solution for packaging fragile goods such as electronics, medical devices, and other sensitive products. Urethane foam ensures that items remain secure and undamaged, even under the rigors of transportation.
Electronics
Urethane is used in the electrical and electronics industries for encapsulating, sealing, and insulating fragile components such as printed circuit boards (PCBs), underwater cables, and microelectronic devices. Its excellent electrical insulating properties, combined with its resistance to moisture and chemicals, make urethane an ideal material for protecting sensitive components from environmental damage and ensuring reliable performance in demanding conditions.
Appliances
Urethane plays a key role in many household appliances, particularly in the form of rigid foams. These foams provide excellent thermal insulation, making them ideal for refrigerators, freezers, and other appliances that require temperature control. Urethane’s insulating properties help improve energy efficiency by keeping the interior temperature stable, reducing energy consumption and enhancing appliance performance.
Buildings and Construction
Modern homes demand materials that are strong yet lightweight, high-performing yet easy to install, and durable yet versatile. Urethane meets these needs while also helping to conserve natural resources and reduce energy consumption, benefiting the environment.
Apparel
With advancements in polyurethane manufacturing techniques, a wide range of urethane-based clothing can now be produced. This includes synthetic leather and man-made skins, which are used in garments, sportswear, and various accessories.
Flooring
Urethane is also a key material in flooring solutions. It is used as a protective coating for wood, vinyl, and concrete floors, offering durability, abrasion resistance, and ease of maintenance. Urethane-based floors are particularly popular in high-traffic areas such as schools, hospitals, and commercial spaces.
Top 9 Urethane Material Manufacturers
Here, we list the top 9 urethane material manufacturers’ websites to help you find the proper grades of urethane you need for your projects. Check them out below:
- Filoform
- Dow Corporate
- Polycast Industries, Inc.
- Smooth-On, Inc.
- AGC Inc.
- Asia Industry Co.,Ltd.
- DIC CORPORATION
- Pelnox
- Arakawa Chemical Industries,Ltd.
Conclusion
In conclusion, urethane is a highly versatile material with applications across many industries. As the material continues to evolve through advancements in manufacturing techniques, urethane-based products are becoming more widely accessible and efficient, offering both environmental benefits and high performance.
At KUSLA, we have extensive experience in identifying the ideal urethane grade for specific applications and can help you find the perfect match for your project. Contact a KUSLA expert or request an instant quote for urethane casting today.
FAQ
Is Urethane a Rubber or Plastic?
Urethane is neither strictly a plastic nor rubber, but it shares similar properties with both, depending on the grade. It can be used to create parts that function like either plastic or rubber, offering versatility in various applications.
Is urethane toxic?
It depends on the stage of its use. Before curing, urethane can be toxic and should be handled with care, as it may release harmful fumes. However, once it is fully cured or transformed into an end-use product, it is generally considered safe and non-toxic for most applications. Proper handling during the curing process ensures safety for both users and the environment.