Prototype tooling are widely used in product development, especially in Automotive, Consumer products, and medical industries. it can make plastic or rubber prototype parts rapidly, significantly reducing costs and lead times. Using prototype tooling early in the design phase allows for faster iterations, quicker refinements, and early detection of design flaws, ensuring products move from concept to market efficiently and with less risk.
To get high-quality products made by prototype tooling, you need to understand clearly how the prototype tooling works. In this article, we will explore what is prototype tooling and its advantages, materials, applications, and more.
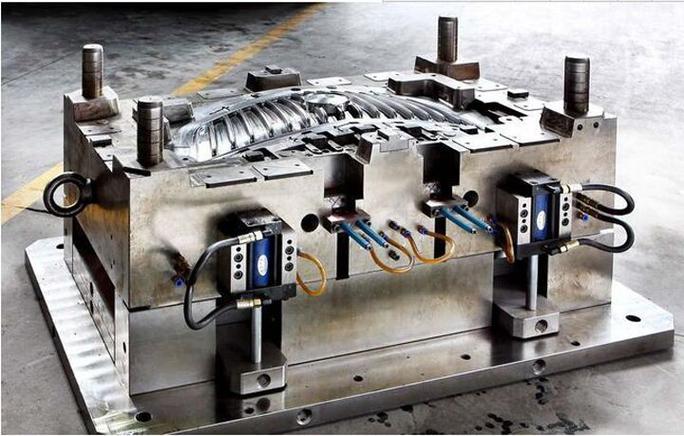
What is prototype tooling?
Prototype tooling, also referred to as soft tooling or rapid tooling, is a manufacturing process used to create temporary molds that allow for the quick and cost-efficient production of prototype parts. It enables the production of parts through low-volume injection molding that functions as production tools.
There is a slight difference when Prototype tooling defined as soft or rapid tooling. Rapid Tooling, As the name suggests, rapid tooling focuses on speed. It uses advanced manufacturing techniques, such as 3D printing or casting, to produce molds quickly. Soft Tooling involves fabricating molds from softer, less durable materials than those used in final production. Softer metals like aluminum and soft steel can be machined faster than harder, production-grade metals.
Benefits of Prototype Tooling
Prototype tooling are highly valued by engineers during the product development process because they provide several key benefits. Here’s why:
Reduced Cost
The cost of prototype tooling is significantly lower compared to production tooling, making it a highly affordable and practical option for producing plastic parts used in testing, design validation, and early-stage development iterations.
Fast to Market
Generally, prototype tooling can be manufactured within a short lead time of just 3 days to 3 weeks. This rapid turnaround allows users to obtain the product quickly, enabling faster testing, earlier market entry, and the opportunity to gain a competitive edge and secure more business.
Various Materials
Similar to production tooling, prototype soft tooling is capable of working with a wide range of materials. This versatility allows engineers to experiment with different materials and determine the most suitable options to meet production needs effectively.
Design Validation
Prototype tooling can work with the same plastic materials as production tooling, allowing engineers to test parts before mass production. The test results can be used for design validation, enabling changes to be made if any test failures occur. This process helps eliminate risks before making significant investments.
Prototype tooling materials
When building prototype tooling, there are primarily three types of materials commonly used, each offering distinct advantages. Let’s take a look at these options and how they contribute to the prototyping process:
Silicone
Silicone tooling, or silicone molds, are commonly used for casting urethane prototypes. These molds are made from soft materials known for their excellent flexibility, stability, and durability. Various grades of silicone can be selected based on the specific requirements of different products. However, because of their softness, silicone molds typically have a lifespan of around 25 copies before they begin to wear down.
Aluminum
Aluminum is an excellent material for prototype tooling due to its machinability, which helps save time during the manufacturing process. Aluminum tooling is typically used for producing parts in quantities of less than 1,000 pieces, as the material is not strong enough to withstand the repeated impact of injection molding over larger production run
Soft Steel
Soft steels such as P20 and NAK80 are commonly used to create prototype tooling for low-volume injection molding. These materials are harder than aluminum, offering a better lifespan and allowing for the production of more parts—typically up to 10,000 piece.
How to make prototype tooling?
Generally, there are two common methods to make a prototype tooling in a short time. Direct Method and Indirect Method.
Direct Approach
The direct approach involves creating the molding core and cavity inserts using rapid prototyping techniques, such as CNC machining on aluminum or soft steel blocks, and metal 3D printing, all directly based on the 3D model of the tooling.
Indirect Approach
The indirect approach uses master patterns as a base to create prototype soft tooling, such as silicone molds. These soft toolings can produce a certain number of replicas of the master patterns. This means the quality of the products made with these toolings depends on the quality of the master patterns.
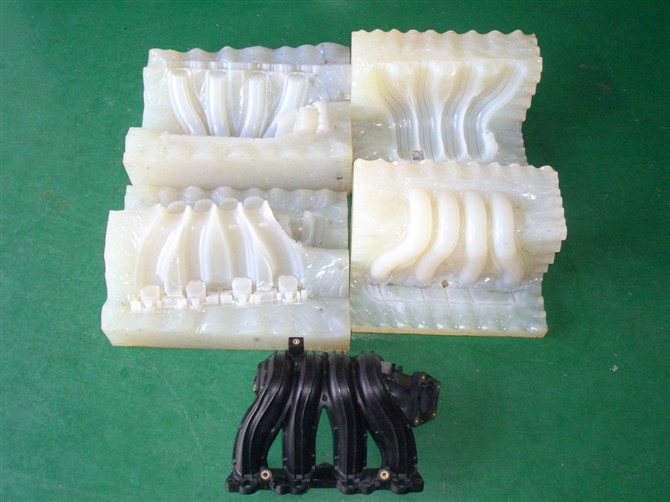
Tips for making a prototype tooling
Even creating prototype tooling is much easier than creating mass-production hard tooling. However, there are also many techniques during the manufacturing process to save costs and improve tooling quality. some of the tips for making Prototype tooling are below:
- Use standard mold bases and only produce inserts to save cost.
- if allowed, use aluminum or soft steels that can be machined more quickly.
- Avoid using additional processes like EDM (Electrical Discharge Machining).
- Incorporate manual inserts where applicable.
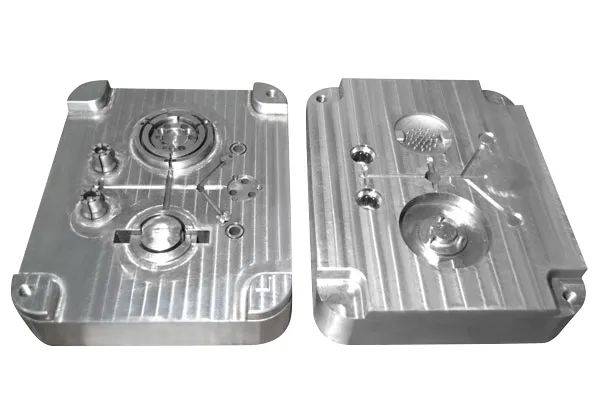
Applications of prototype tooling
Prototype tooling is widely used in various industries. Here, we list some of the main applications across key sectors:
Automotive Industry
The automotive industry traditionally faces long lead times when producing hard tooling for cars and car components. Prototype tooling plays a crucial role by enabling engineers to obtain parts ahead of schedule for testing. This helps identify design issues early and accelerates the process of bringing new cars to market. Prototype tooling is particularly valuable for innovation projects that require extensive testing before the product is ready for commercial use.
Medical Industry
In the medical industry, prototype tooling helps produce medical device parts quickly and accurately, expediting the regulatory approval process and enabling innovative treatments and diagnostic tools to reach the market faster. It is widely used for the rapid creation of various medical products, including custom implants, surgical instruments, and diagnostic devices.
Consumer product
Prototype tooling used in the consumer product industry can effectively support on-demand manufacturing when production volumes are small. This is especially important as the market evolves quickly, with frequent demand for a wide variety of similar products to meet changing consumer preferences and trends.
Prototype tooling vs production tooling
To better understand prototype tooling, let’s compare it with production tooling. This will help you see why prototyping is such an effective approach.
Tooling materials
Prototype tooling uses soft materials such as silicone and soft steels, while production tooling typically uses hard steels. Common soft steels used for prototype tooling include P20 and NAK80, while hard steels like S416 are used for production tooling.
Production volume
Production tooling made from hard steel can produce hundreds of thousands to millions of parts. However, prototype tooling made from soft steel materials can typically produce fewer than 10,000 parts before it begins to degrade.
Cost
Prototype tooling requires a lower investment to produce compared to hard tooling, due to lower material and machining costs. Additionally, it is more cost-effective when modifications are needed. For example, soft steel tooling typically costs only 40% to 60% of the cost of production tooling.
Lead Time
Making prototype tooling typically takes from 1 week to 4 weeks, depending on the complexity and materials used. In contrast, producing production tooling usually takes much longer, ranging from 2 months to 4 months. This difference in lead time highlights the quicker turnaround and flexibility that prototype tooling offers, especially for early-stage testing and development.
Quality
In terms of quality, parts produced by production tooling are generally superior to those made with prototype tooling. This is because production tooling is designed with more advanced cooling and injection systems, ensuring more consistent results and higher precision during mass production.
Applicable Project Stage
Prototype tooling is typically used during the design validation stage, allowing for testing and refinement of the product. In contrast, production tooling is used during the mass production stage, where the focus shifts to high-volume manufacturing and consistent quality.
Alternatives to soft tooling for rapid prototypes
Although prototype tooling offers many benefits compared to production tooling, when making plastic prototypes, there are other manufacturing processes that should also be considered, as they offer different advantages. Let’s take a look:
Prototype CNC machining
Prototype CNC machining creates plastic parts using a computer-controlled process that employs a precise cutter to remove material from a block, shaping the part according to the 3D data. It is ideal for producing high-precision prototypes with a short lead time and low cost.
Prototype 3D printing
Prototype 3D printing can create parts with more complex geometries than CNC machining, offering faster lead times and lower costs. However, the strength of 3D printed parts is generally not as high as those produced through CNC machining or prototype injection molding, as 3D printing uses a layer-by-layer method to build the part.
Conclusion
As this article has explained everything about prototype tooling, KUSLA, a low-volume manufacturing supplier in China, specializes in producing prototype tooling quickly and injecting high-quality standard plastic parts using prototype injection molding services. Contact us if you want to learn more about prototype tooling or any low-volume production projects.
FAQ
What are the different types of tooling?
There are three basic types of tooling in manufacturing, each serving a different stage of the process, from product development to the beginning of mass production runs: prototype tooling, bridge tooling, and production tooling. As their names suggest, each type has its own set of benefits and drawbacks, making it more suitable for specific stages of a project.
How to choose the right prototype tooling?
To choose the right prototype tooling, the key factors to consider are the quality and volume of the parts produced, as well as the cost of your project. For example, silicone tooling can produce visually appealing parts but is not suitable for material testing. Aluminum tooling can create more parts, but it typically cannot produce more than 1,000 pieces. Soft steel tooling offers better part quality and can handle higher volumes, but it costs more than the other two options.