People often ask us about the best plastic injection molding material for their projects. However, there isn’t a straightforward answer because product requirements vary for different applications. There are many plastic injection molding materials available, each with unique properties.
To choose the right material, it’s important to understand the common types of injection molding materials and their characteristics. In this article, we’ll provide an overview of the common plastic materials used for injection molding and a simple guide to help you consider the key factors for your decision.
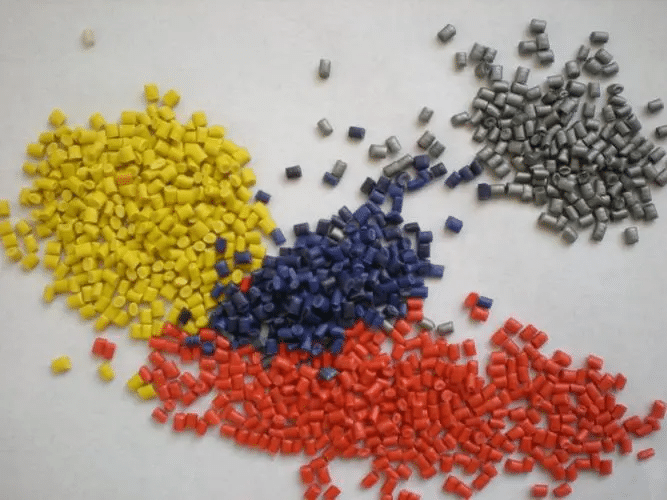
The Top 12 Plastic Injection Molding Materials
Here, we’ve listed the most common plastic materials used for injection molding. We’ll explain each material one by one. Let’s get started!
Acrylic (PMMA)
Acrylic, also known as PMMA (short for poly(methyl methacrylate)), is a strong and clear thermoplastic. It serves as a lightweight, shatter-resistant alternative to glass and provides excellent optical clarity, allowing a high percentage of light to pass through.
Key Properties of Acrylic:
- Exceptional Transparency
- Weather and Chemical Resistance
- Surface Hardness
- Dimensional Stability
Applications: Windows, greenhouses, solar panels, bathroom enclosures, and architectural, lighting, and outdoor components
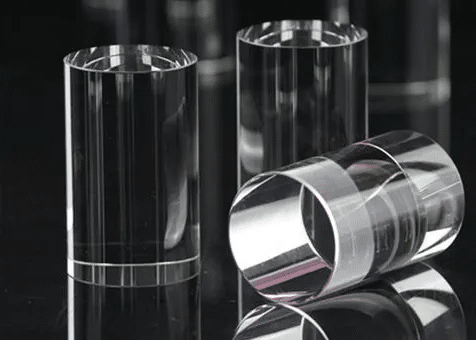
Polycarbonate (PC)
Polycarbonate is another clear injection molding material known for its excellent optical properties and exceptional durability. It allows for effective light transmission and maintains its color and strength even when pigmented. While it is not scratch-resistant, polycarbonate is much stronger than glass and highly durable, making it a reliable choice for various applications.
Key Properties of Polycarbonate:
- High Impact Resistance
- Temperature Resistance
- Transparency
- Chemical Resistance
- Rigidity
Applications: Machinery guards, clear and tinted windows, LED light diffusers, and clear molds for casting. Not recommended for food preparation or storage due to the presence of bisphenol A (BPA).

Acrylonitrile Butadiene Styrene (ABS)
ABS is a one of the most used thermoplastic in injection molding, known for its ease of use and versatility. With a low melting point, it is easy to mold into various shapes. As an opaque material, ABS works well with colorants, making it ideal for products that require vibrant colors. It also supports a variety of textures and surface finishes, allowing for customizable designs.
Key Properties of ABS:
- Impact Resistance
- Surface Hardness
- Chemical Resistance
- Uniform Shrinkage
- Wide Temperature Range
Applications: Keyboard keys, protective headgear, automotive parts, consumer goods, sports equipment, and industrial fittings.
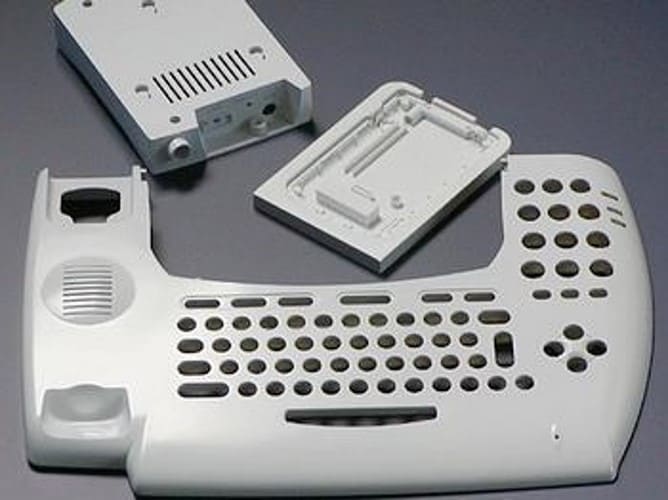
Polypropylene (PP)
Polypropylene (PP) is another one of the most commonly used plastic in injection molding, known for its excellent properties. It offers good chemical resistance, retains its shape even after bending or torsion, and has a high melting point, making it durable and reliable. PP has a naturally glossy surface when properly manufactured. Its chemical resistance and elastic properties make it especially useful for food-related applications, where durability and safety are crucial.
Key Properties of Polypropylene:
- Chemical Resistance
- Fatigue Resistance
- Electrical Resistance
- Elasticity
Applications: Toys, storage containers, sporting goods, packaging, appliances, and power tool bodies.
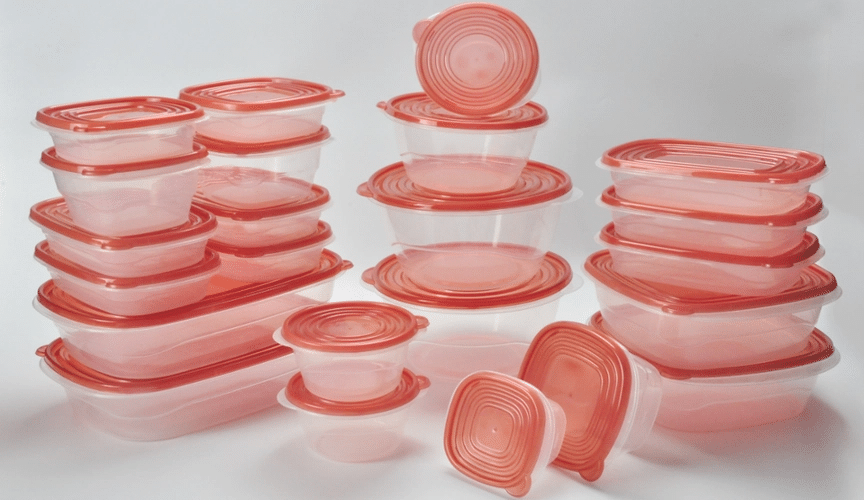
Nylon(PA)
Nylon is a synthetic polyamide (PA) known for its toughness, high heat resistance, and excellent abrasion resistance. It also offers good fatigue resistance and noise-dampening properties, making it a versatile material for many applications. However, its high-temperature resistance can lead to shrinkage and issues with mold filling. While nylon is prone to degradation from sunlight and has poor resistance to strong acids and bases, these limitations can be addressed by using additives and fillers to improve its performance in specific conditions.
Key Properties of Nylon:
- Low Friction
- Chemical Resistance
- Abrasion Resistance
- Adaptability
Applications: Mechanical parts, casings, threaded inserts, and high-friction applications.
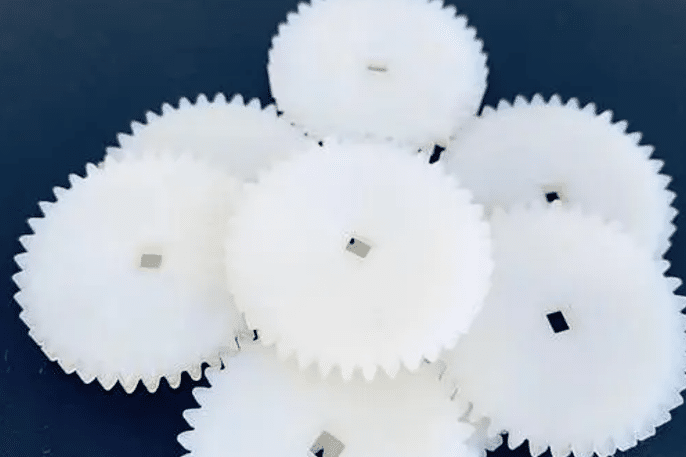
Polyethylene (PE)
Polyethylene is a cost-effective, consumer-grade polymer that is widely used around the world, this is because it has different types available based on density. The three main types of polyethylene are high-density polyethylene (HDPE), low-density polyethylene (LDPE), and polyethylene terephthalate (PET, PETE). Polyethylene is commonly used for injection molding larger items and blow molding films and bottles.
Key Properties of PE:
- Sustainability
- Chemical and Heat Resistance
- Food Grade
- low cost
Applications: milk bottles, medicine and detergent bottles, plastic bags, and trash cans.
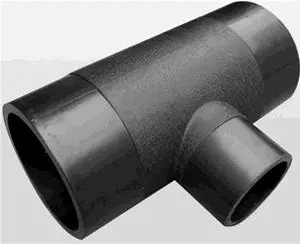
Polyoxymethylene (POM)
POM is also known as acetal, It can be injected into parts that require low friction, high stiffness, and excellent dimensional stability. Because they have a highly crystalline structure, POM plastics are naturally opaque and white.
Key Properties of Polyoxymethylene:
- Rigidity
- Impact Resistance
- Solvent Resistance
- Glossy Surface
Applications: Bearings, gears, conveyor belts, fasteners, eyeglass frames, and high-performance engineering components.
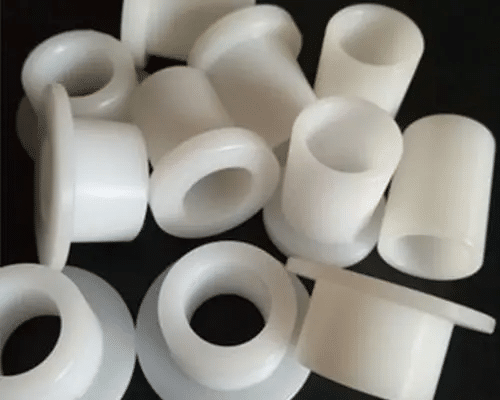
Polybutylene terephthalate (PBT)
PBT is one of the toughest engineering thermoplastic materials. It is a semi-crystalline material with very good mechanical strength and thermal stability. The melting point and high-temperature deformation temperature are lower than PEI materials and higher than polycarbonate.
Key Properties of Polybutylene terephthalate
- High mechanical strength
- High thermal resistance
- Dimension stability
- Electrical Resistance
Applications: electrical switches, motor housings, electric fans, radiator grilles.
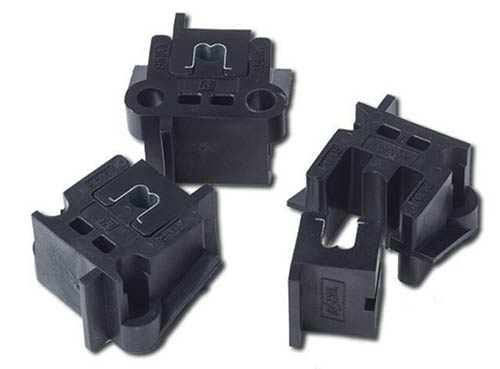
Polyetherimide (PEI)
Polyetherimide (PEI), also known as Ultem, is a high-performance plastic with outstanding heat resistance. It is a rigid material that maintains its strength and stability even at elevated temperatures. Because of these properties, PEI is widely used in industries such as automotive and electronics where heat resistance performance under extreme conditions is essential.
Key Properties of Polyetherimide:
● Rigid
● High Heat resistance
● High tensile strength
● Flame retardant
Applications: Engine Plastic parts, Electronic housings.
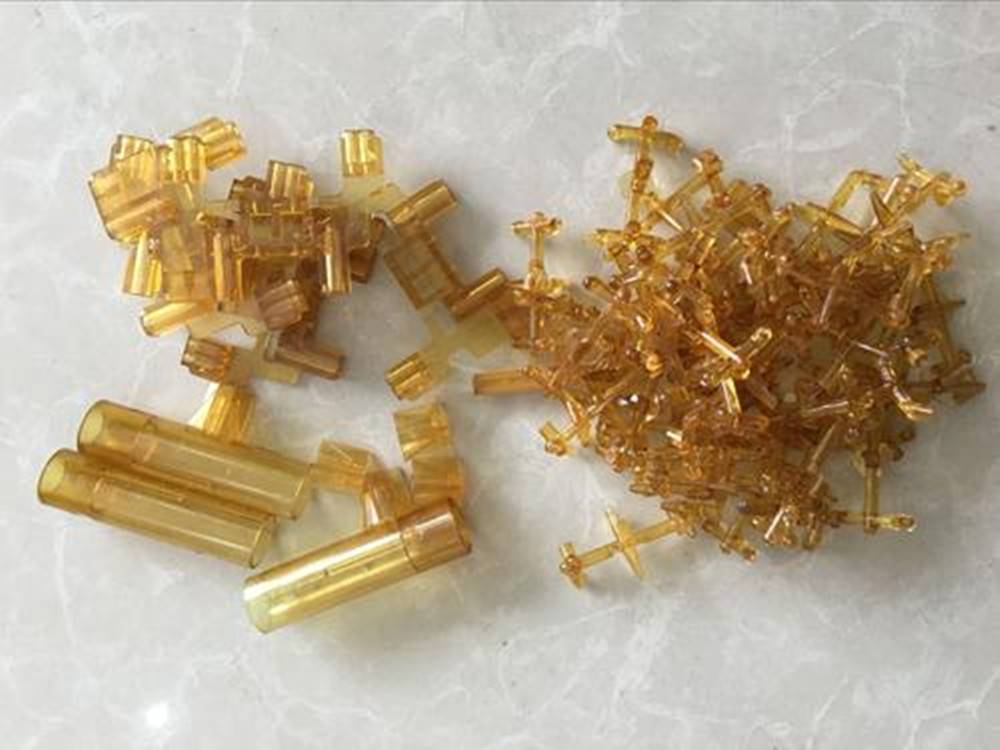
Polystyrene (PS)
There are two common types of polystyrene used in injection molding: High Impact Polystyrene (HIPS) and General Purpose Polystyrene (GPPS). GPPS is transparent, while HIPS is opaque. Polystyrene is often chosen for its flexibility and ability to bend without breaking, making it ideal for hinged applications like disposable food containers and bottles.
Key Properties of polystyrene:
- Optical clarity
- FDA grade
- Stability
- low cost
Applications: containers, caps, bottles for packaging and cutlery, trays for household products, and medical supplies.
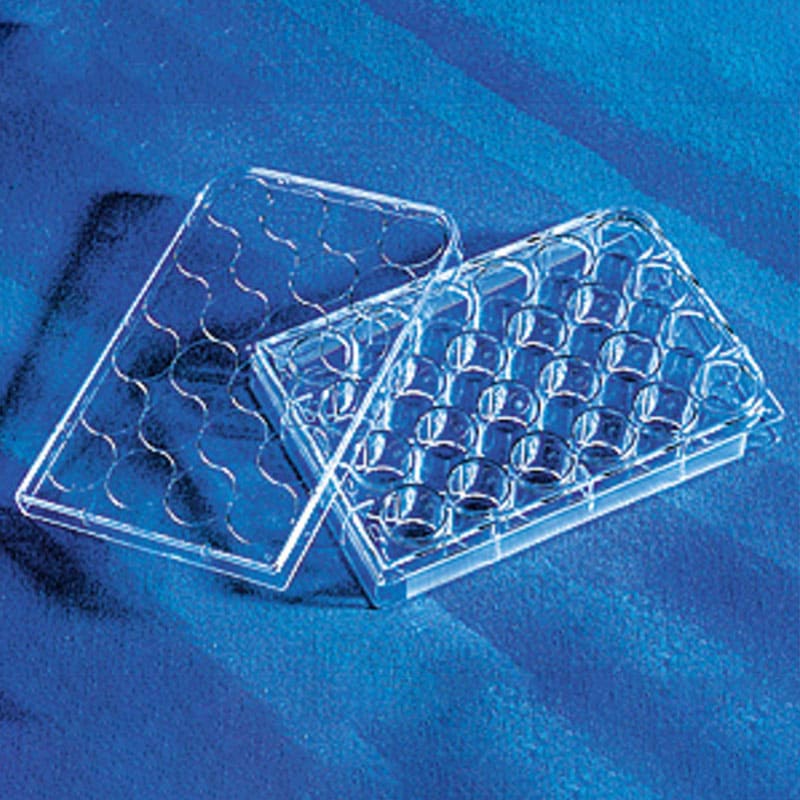
Thermoplastic Elastomer (TPE)
TPE, also known as thermoplastic rubber (TPR), is a material that combines the best properties of both plastic and rubber. It is processed like plastic but offers the flexibility and performance of rubber. TPE can be stretched to moderate elongations and, once the stress is removed, it returns to its original shape.
Key Properties of Thermoplastic Elastomer:
- Versatility
- Consistency
- Eco-friendly
- Safe for the medical and food & beverage industries
Applications: Footwear, medical devices, auto parts, and pet products, including weather seals and shock dust boots in automotive and medical applications.
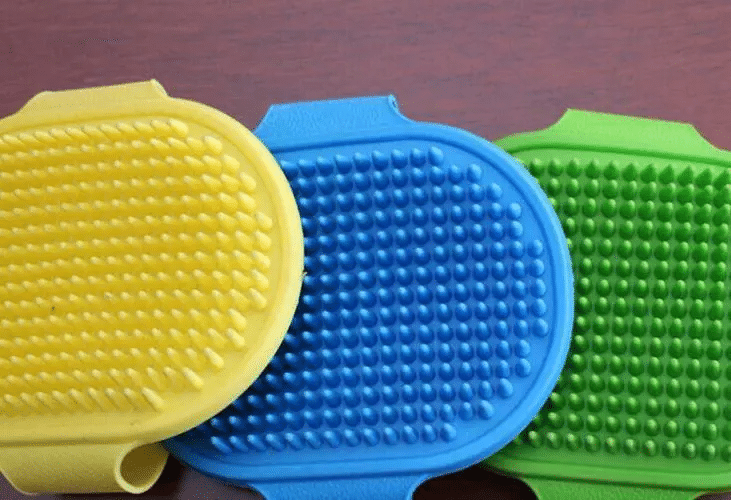
Thermoplastic Polyurethane (TPU)
Thermoplastic Polyurethane (TPU) is a type of TPE that can be injection molded into a harder rubber, because of its high durometer. TPU is soft, elastic, and offers excellent tensile and tear strength, making it ideal for parts that require rubber-like elasticity. Although TPU is more expensive than other resins, it is often chosen for applications like protective wire and cable sheaths.
Key Properties of Thermoplastic Polyurethane
- Elasticity
- Resistance to Impacts
- Dimensional Stability
- Resistance to Tears
- Resistance to Grease and Oil
Applications: Footwear, gaskets, caster wheels, electronics enclosures, and medical devices.
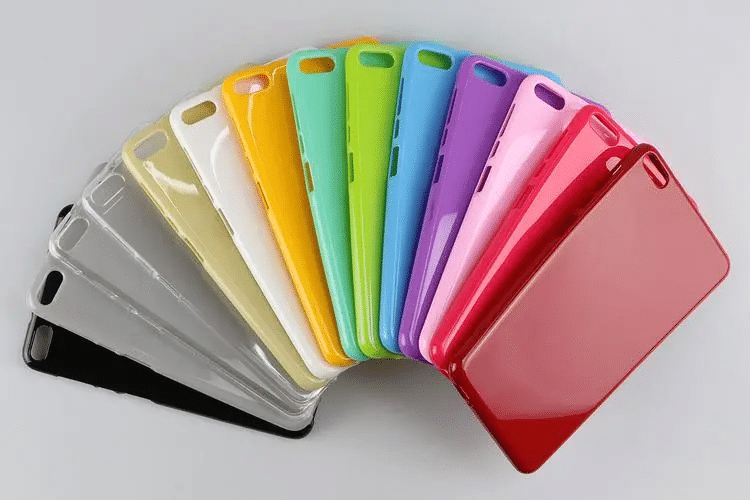
Key properties when choosing Injection Molding Materials
To choose the right material for your product through the injection molding process, there are several key properties you need to review on the material’s datasheet before starting manufacturing. Below, we explain some of the most important properties:
Maximum Temperature
Maximum temperature is one of the most critical factors when selecting injection molding materials. This is often represented by the deflection temperature under load (DTUL), also known as the heat deflection temperature (HDT). Another related measure is the Vicat softening temperature, which indicates the temperature at which a polymer starts to soften. While DTUL measures mechanical deflection, the Vicat temperature is closer to the material’s actual melting or softening point, so the Vicat number is typically higher. These temperature-related properties are crucial for determining whether a material is suitable for your product’s intended use. If the application involves temperatures that exceed these values, the material is not a viable option, regardless of its other properties.
Tensile Strength
Tensile strength is a Another property to consider when choosing an injection molding material, as it indicates the material’s ability to withstand stretching or pulling forces without breaking. It is typically measured by the maximum amount of stress the material can handle before it begins to deform or fracture. This property is essential for determining how well the material will perform under load in various applications. Materials with higher tensile strength are better suited for products that need to endure significant stress or mechanical force during use. If the material’s tensile strength is too low for the intended application, it may fail under normal operating conditions.
Impact Resistance
Impact resistance measures the material’s ability to withstand sudden forces or shocks without breaking. The higher the impact resistance, the more durable the material is in applications where the product may be exposed to rough handling, drops, or other impact-related stresses. Materials with low impact resistance may fail or break easily under such conditions, this is why this property is critical for products that need to endure high-force impacts.
Melt Flow Rate
Melt Flow Rate (MFR) captures an important aspect of a material’s behavior with a single number. It is commonly used by processors to gauge how a material will flow during the molding process. A higher MFR indicates that the material flows more easily, which can be advantageous for filling complex mold shapes efficiently. Understanding the MFR helps optimize the injection molding process, ensuring smooth material flow and consistent part quality.
Injection Molding Materials Comparison Chart
To better understand the properties of easy-to-mold materials and make it easier to compare the injection molding materials we’ve introduced, here is a comparison chart to explain the key differences.
Material | Max Temp (°C) | Approx. Tensile Strength | Impact Strength (J) | Melt Flow Rate | Cost (Low to High) |
Acrylic (PMMA) | 85-100 | 8000 psi | Low | Medium | Medium |
PC | 120-140 | 9500 psi | High | Medium | High |
ABS | 95-105 | 5900 psi | High | Medium | Low |
PP | 120-150 | 4800 psi | Medium | Easy | Low |
Nylon (PA) | 160-200 | 12400 psi | High | Medium | High |
PE | 60 -100 | 800 – 13100 psi | High (LDPE) High (HDPE) Low (PET) | Easy | Low |
POM | 100-120 | 6400 -10600 psi | Very High | Medium | High |
PBT | 150-170 | 7,000 -10,000 psi | High | Medium | Medium |
PEI | 180-220 | 7,000 – 12,000 psi | Medium | Hard | High |
PS | 90-100 | 2560 – 7690 psi | High | Easy | Low |
TPE | 60 -100 | 290 – 8200 psi | High | Medium | High |
TPU | 60 – 80 | 4060 – 13900 psi | NA | Medium | Medium |
Tips: Different grades or blends of the same material can have slightly different thermal properties.
Top Injection Moulding Materials manufacturer
There are many plastic resin manufacturers in the world, Here we list the 5 famous manufacturers for you to download the datasheet of each material from their websites.
Conclusion
There are also many other plastic materials besides the above common injection molding materials, each has advantages and disadvantages. To make high-quality injection molded parts, different injection molding parameters need to be used. KUSLA has many years of injection molding experience and could help you with prototype injection molding project. Contact us now if you have any questions about the injection molding materials.
FAQ
What is the strongest material for injection molding?
Generally, the strongest material for injection molding in terms of tensile strength, impact resistance, and durability is Polyoxymethylene (POM), also known as Acetal. POM is known for its excellent mechanical properties, including high tensile strength and outstanding impact resistance.
What is the cheapest material for injection molding?
Polypropylene (PP) is the cheapest material for injection molding due to its low material cost and ease of manufacturing. Its simple processing requirements, combined with its widespread use in various industries, contribute to its affordability.