Many plastic products in our daily lives have metal parts inside them. These products are made using a process called insert molding, which is a special type of injection molding. Insert molding lets manufacturers combine plastic materials with other materials, like metal, to create products that are strong, light, and resistant to wear.
To get the best results, it’s important to understand how the insert molding process works. This article will explain what insert molding is, how it works, and the common uses of insert molded parts. It will also provide useful design tips for creating parts with this process.
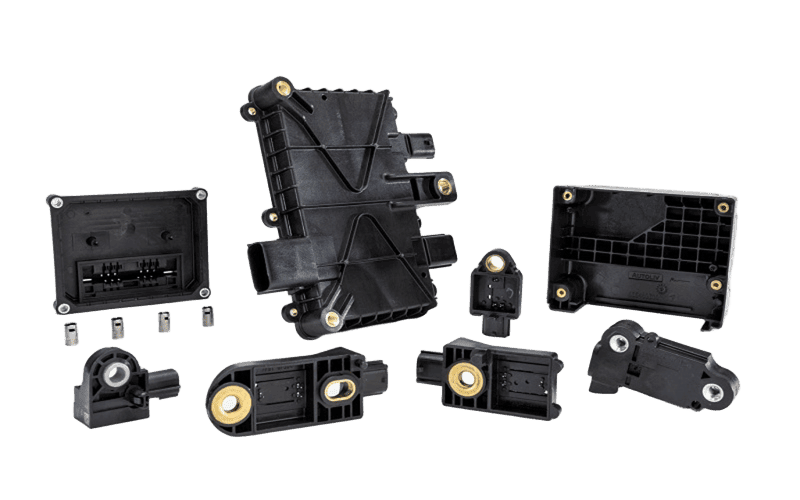
What is insert molding?
Insert molding is a process where plastic parts are formed around other materials, called inserts, which are not plastic. These inserts are placed into the mold before plastic is injected. When the plastic fills the mold, it surrounds and holds the inserts tightly in place.
This process allows manufacturers to combine different materials, like metal and plastic, into one product. It uses special plastics to improve wear resistance, strength, and reduce weight, while metal inserts add strength and help with conductivity.
Common Insert Molding Materials
Insert-molded components are usually made from a combination of plastic and metal. Different types of plastics are used in the injection molding process because of their strength, durability, or ability to conduct electricity. Here are some common types of plastic used:
- Thermoplastics: Polypropylene (PP), Nylons (Polyamides/PA), polycarbonate (PC), ABS (Acrylonitrile Butadiene Styrene), Polyethylene (PE) and Acetal;
- Thermosets: Polyester, Epoxy, melamine-formaldehyde resins, and urea-formaldehyde resins;
- Elastomers: Polyurethane, natural rubber.
For the metal inserts, common materials include:
- Stainless steel
- Brass
- Aluminum
Benefits Of Insert Molding
Insert molding has many benefits, some of which you may have already seen. Here are more advantages of using insert molding and why it is widely used:
Increases Design Flexibility
Insert molding gives designers and manufacturers the freedom to create almost any shape or design they want, which is harder to achieve with other methods like metal forming. For instance, when making a plastic electronic enclosure, insert molding allows you to integrate electrical leads and nodes directly into the design, making it more streamlined.
It also makes it easier to add aesthetic features, like labels or decorative parts, without needing extra steps. Designers simply select the right materials and incorporate the inserts into the mold design. This flexibility expands the range of possible designs for various plastic parts and applications.
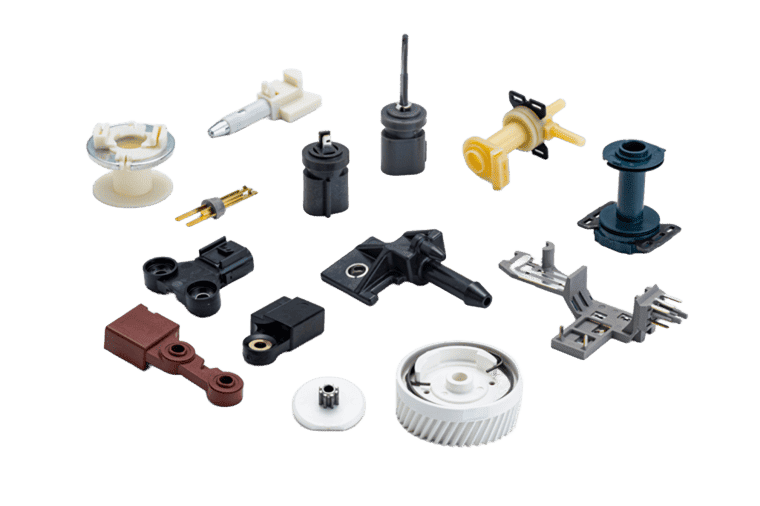
Reduce Costs
Insert molding combines multiple components into one step, making the manufacturing process more cost-effective. Since it’s a one-step process, there is less need for extra assembly work, which lowers labor costs.
Using just one injection to create a complete assembly reduces errors during manufacturing, helping cut down on waste and material costs. Insert molding also allows you to use plastic in ways that were once only possible with metal, offering a more affordable alternative to metal inserts and enclosures.
Increase Reliability
In this process, molten plastic flows around inserts, holding them securely as it cools. When metal inserts are used, they further increase the strength of the part. This reduces the chance of loose components, enhances durability, and improves shock resistance, resulting in more reliable and long-lasting products.
Reduce Size and Weight
Insert molding eliminates the need for adhesives, connectors, or fasteners in complex parts, as well as the need for metal enclosures. It also allows for the addition of metal inserts for added strength and durability. As a result, the plastic parts produced are smaller and lighter, while still being more functional and reliable than parts made with other methods. For example, in the automotive industry, insert molding can be used to create thinner doors and console components, freeing up space inside the car and reducing its weight.
Steps For The Insert Molding Process
The insert molding process is similar to regular injection molding because it also involves melting and injecting plastic into a mold. However, in insert molding, inserts are placed in the mold before the molten plastic fills the cavity. Here’s how the process works in 5 simple steps:
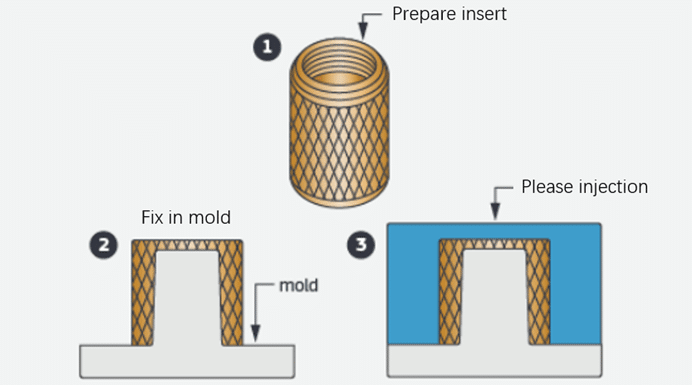
Step 1: Loading Inserts
Before the molten plastic is injected, the metal insert must be placed in the correct position. It should stay secure during the process, so the mold must be designed to hold the insert properly. There are two ways to place inserts into the mold: automated loading and manual loading.
Automated Loading uses robots or machines to place inserts into the mold. It is more precise, consistent, and faster, making it ideal for high-volume production. These machines can handle high temperatures and produce more parts in less time.
Manual loading involves placing inserts into the mold by hand. It works well for low-volume production and is more common because operators can inspect, package, and assemble the parts during the process, keeping costs low. However, it may not be as precise or consistent as automated loading.
Step 2: Injection
Once the inserts are in position, you can start the standard injection process. The injection unit pushes molten plastic into the mold under high pressure, ensuring it bonds tightly and completely to the inserts.
Step 3: Remove the Part
Once the plastic is fully injected, the next step is to open the mold and remove the part. Before doing so, it’s important to let the part cool and solidify properly. Maintaining a consistent temperature helps ensure even solidification. Holding pressure should also be applied to prevent shrinking and to keep the insert securely in place for long-term use.
Step 4: Remove the Sprues
After the part is molded, it will likely be attached to sprues, which provide support to keep the part rigid during the molding process. To use the part, you’ll need to cut off the sprues and trim any excess material, such as flashing, to achieve a clean, finished product.
Step 5: Post-Processing
Finally, plastic molds usually need some post-processing before they are ready for the market. Common post-processing treatments for insert-molded components include deburring, heat treatment, and adding a surface finish.
Common Types Of Inserts
Metal is the most common type of insert used in insert molding. Inserts are often used to help fasten and align plastic parts with other assemblies. The metal insert in an insert-molded product can serve various purposes, enhancing the durability or performance of the thermoplastic part. Here are a few ways metal inserts can improve the final product:
- Electrical Contacts
- Studs, screws, pins or clips
- Reinforcement
- Threads
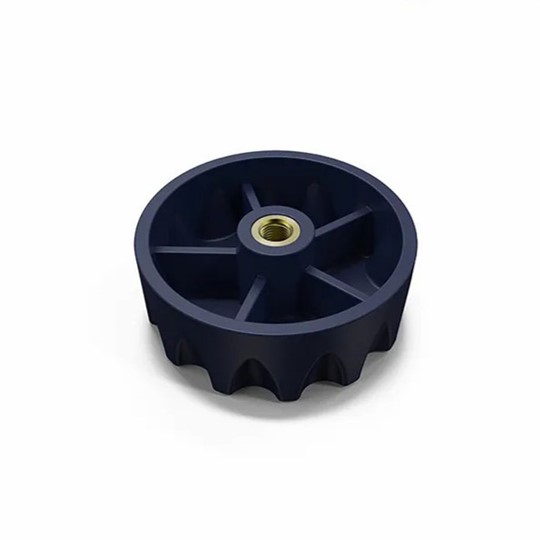
Considerations before Insert molding
Before starting insert molding, there are several factors to consider in order to ensure the success of the process and the quality of the products. Here are some key considerations:
Choose the Right Insert
Select inserts that meet your specific requirements. It’s important to understand the properties of the inserts you choose for the application. Insert molding involves high temperature and pressure, so the insert must be able to handle these conditions. You should consider the material, size, and surface finish of the insert to determine the best molding process.
Put Insert in right Location
The location of the insert is important because it affects the forces acting on it over time. It’s also important to consider how the insert will be used and how much plastic is needed to hold it securely in place. Make sure the insert stays in position throughout the process, as any movement can impact the molding and make the part unusable. When designing the insert placement, ensure there is enough plastic around the insert to prevent it from coming loose after use.
Keep Narrow Gap Between Plastic and Metal
A narrow gap helps prevent voids and improves the part’s structural strength. Be sure to design a small gap in your mold where the insert will be placed, so the plastic can mold around the metal insert and fuse the two together. A large gap will keep the materials separate, causing the insert to come loose.
Choosing the Right Mold
A well-designed mold is essential for ensuring uniform flow of molten plastic and keeping the insert in place during the molding process. It’s important to choose the right type of injection mold that is specifically designed to securely hold the inserts throughout the entire process.
Design guidelines for Insert Molding
At Kusla, we’ve compiled a list of design guidelines based on our experience with many real-world cases. You can use these guidelines when designing your product for the insert molding process to create a strong, reliable product. Let’s take a closer look at these design tips:
1. Brass is a commonly used insert material due to its resistance to rust and corrosion, ease of processing, and moderate cost. If there are no special requirements, choose brass as the insert material.
2. Use circular or axially symmetric shapes for inserts, and avoid sharp corners or angles to prevent deformation and breakage.
3. The extended portion of the insert should be designed as a cylinder for easier mold processing, as cylindrical holes are the easiest to machine in molds.
4. Inserts should have sealing protrusions or structures to prevent material overflow during the injection molding process, as shown in the picture below.
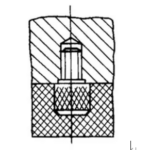
6. To prevent ripple-like shrinkage marks on the bottom of the plastic, which can affect both appearance and strength, the minimum distance “T” between the insert’s bottom surface and the plastic wall should be greater than D/6, where “D” is the diameter. The picture below illustrates each dimension.
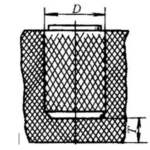
7. The distance between the insert and the product’s side wall should be at least 0.5mm to ensure the mold has sufficient strength, as shown in the picture below.
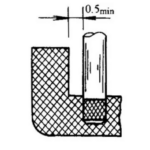
8. When setting the insert in the boss, to ensure stability and strength of the attachment, the insert should extend to the bottom of the boss (while maintaining a minimum bottom thickness). The top of the insert should have rounded edges. The picture below shows an example.
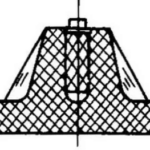
Applications Of Insert Molding Parts
Insert molded components are used in many different industries. Here are some common Industries where insert molding is applied:
Electronics Industry
In the electronics industry, insert molding is widely used to create parts like terminals, connectors, and pins, which are often embedded in plastic casings. This provides insulation, structural support, and protection from the environment, while still allowing electrical conductivity.
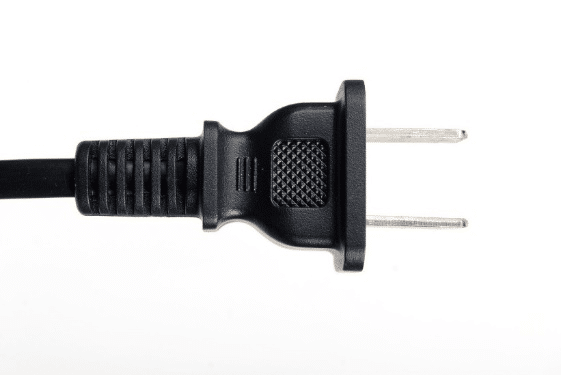
Automotive
In the automotive industry, insert molded parts are often used as an alternative to metal parts. These plastic parts are lighter, more durable, and cost-effective. Common insert molded parts in cars include threaded fasteners, gears, and electrical sensors.
Medical Devices
Insert molding is highly beneficial in the medical field, as plastic parts are easier to sterilize. It is used to make various medical devices, such as dental instruments, tubes, prosthetics, medical equipment parts, enclosures, knobs, and surgical tools.
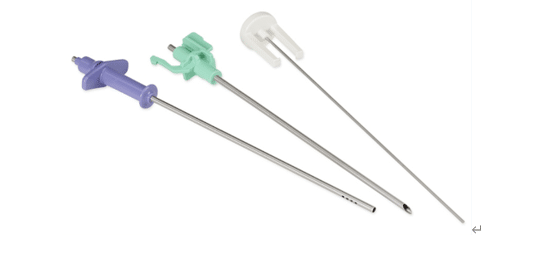
Consumer Products
In our daily lives, insert molding is used to combine metal and plastic in products like toothbrushes, kitchen tools, and power tools. This process improves the product’s strength, functionality, and overall quality, enhancing the user experience.
Conclusion
In summary, Insert molding is a highly popular method and one of the best ways to integrate metal features into plastic parts. If you need high-quality insert-molded components, KUSLA is here to help. With extensive experience in insert molding projects, we offer support during the design phase to ensure your product is optimized for production. Contact us today for your insert molding needs.
FAQ
What is the difference between overmolding and insert molding?
The main difference between overmolding and insert molding is the materials used and how they are combined. Overmolding is typically used to combine two different types of plastic materials, such as applying a soft plastic layer over a hard plastic part. On the other hand, insert molding involves placing a non-plastic insert, usually made of metal, into the mold and injecting plastic around it. The metal insert becomes permanently embedded in the plastic part, adding strength, conductivity, or other specialized properties. In short, overmolding combines two types of plastic, while insert molding integrates plastic with metal or other materials.
Is insert injection molding compatible with large parts?
Not recommended. Insert injection molding is generally best suited for small to medium-sized products. For larger parts, the process can become more challenging due to factors such as increased tooling costs and the complexity of properly placing the inserts. These challenges can make it more difficult to maintain the quality and efficiency of the molding process for larger parts.