Acrylic, also known as plexiglass, is a strong and clear material often used as a substitute for glass due to its high transparency. One of the most common acrylic fabrication ways to make acrylic parts is through CNC machining. CNC machining cuts acrylic precisely and carefully, creating accurate parts without damaging the material. This method is fast and efficient, using machines like lathes and mills to shape the acrylic.
How does CNC machining work with acrylic? What makes acrylic special? Why should you choose acrylic over other clear plastics? This guide will answer all your questions about CNC machining acrylic, including the best machines, settings, and tools to use. It’s perfect for beginners wanting to learn how to create acrylic parts.
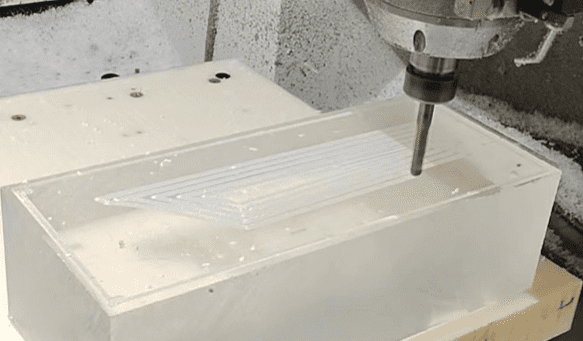
What Is Acrylic?
Acrylic, also called PMMA (Polymethyl Methacrylate), is a clear, lightweight, and durable thermoplastic often used as a glass alternative. It is a colorless polymer that can come in different forms such as small granules, pellets, or sheets. It is strong and resists shattering, scratching, and damage from sunlight or weather.
Key Properties of Acrylic
Acrylic is a popular material used in many industries for making different products. it has lots of outstanding properties that are useful for a plastic part. Let’s explore what makes acrylic special:
Optical Clarity
Acrylic is extremely clear, allowing up to 92% light transmission. With a refractive index of 1.49, it is clearer than glass and most other plastics, making it perfect for optical products and displays.
Lightweight
Acrylic is much lighter than glass, about half the weight. This makes it easier to handle, transport, and machine, while also offering more flexibility in design.
UV Resistance
Acrylic is resistant to UV light, meaning it won’t fade or weaken in the sun. This makes it ideal for outdoor products.
High Impact Resistance
Acrylic is tough and can withstand strong impacts, being up to 17 times more resistant than glass. It can also be heated and shaped into various designs, and once molded, it holds its shape well, especially when cooled quickly.
Scratch Resistance
Acrylic has a hard surface that resists scratches better than many other clear plastics, keeping it looking new longer.
Chemical Resistance
Acrylic doesn’t react with most chemicals, including weak acids, alkalis, and detergents. This makes it safe for use in medical and industrial applications, such as in fluid containers and medical devices.
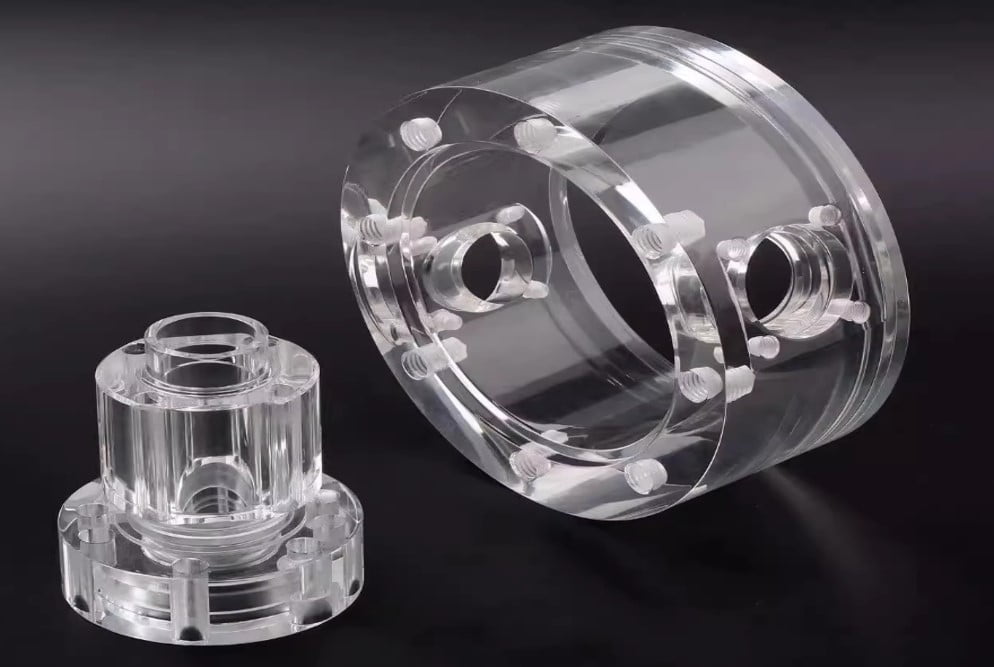
Advantages Of Using Acrylic For CNC machined parts
Acrylic is a top choice for CNC machining because of its unique properties and cost-effectiveness. It combines ease of machining, strength, easy bonding, and the ability to be easily polished and maintained. Let’s explore these advantages in more detail:
Easy to machine
Acrylic is prefered by CNC machinist because it’s easy to shape and work with. As a thermoplastic, acrylic can holds its shape well when cooled, ensuring accuracy during CNC machining. During the cutting process, acrylic doesn’t produce stringy waste, which helps minimize material loss and improves efficiency.
Material Strength
In terms of strength, acrylic is much more durable than glass. It has over 10 times the impact resistance of regular glass. This toughness means that acrylic is less likely to break or crack during machining, reducing the risk of damage to parts or tools. If it does break, acrylic shatters into large, blunt pieces, which is safer compared to glass, making it a preferred choice for applications where safety is critical.
Easy to polish
After CNC machining, plastic parts will have milling marks or surface imperfections. Acrylic is much easier to polish than other plastics, like polycarbonate. With the right polishing techniques, these marks can be easily smoothed out, result in a clear, glossy finish. This makes acrylic a great choice for applications where a high-quality, Glossy and clear appearance is required, such as in display cases, signage, or optical products. Its ability to be easily polished ensures that CNC-machined acrylic parts maintain a professional and attractive look.
Bonding Capability
In CNC machining, parts are sometimes split into smaller pieces due to the limitations of the machining process, such as size constraints or complex geometries. Acrylic’s excellent bonding capabilities help overcome these challenges, allowing separated parts to be securely joined together. Acrylic can be bonded effectively with specialized adhesives, creating strong, seamless connections between parts. Combined with its other properties, acrylic is a reliable choice for CNC-machined parts that require both precision and structural integrity.
Easy to Maintain
Acrylic parts are easier to maintain than many other plastic parts due to their nature properties. To clean the acrylic parts, simply use a damp microfiber cloth to wipe off any marks. It’s important to avoid using rough towels or ammonia-based cleaners, as these can scratch or damage the surface. Proper maintenance ensures that CNC-machined acrylic parts have a longer lifespan.
What are the Types of Acrylic Suitable for CNC Machining?
Acrylic sheets used for CNC machining are typically produced in two ways: extrusion and casting. Each method has different characteristics that can impact the machining process. so let’s explore how the Acrylic sheets are made.
Extruded acrylic sheet
Extrusion acrylic involves melting acrylic pellets and pushing the liquid through a mold to create sheets. This method is commonly used to produce large, thick sheets of acrylic. However, extruded acrylic tends to have internal stresses, which can make it more brittle and prone to cracking. When CNC machining extruded acrylic, it’s important to be cautious of these potential defects.
Cast acrylic sheet
Casting acrylic is produced by melting acrylic pellets and pouring the liquid into a mold, which is then cooled and removed. Cast acrylic is generally better for CNC machining because it has a more consistent structure, making it less likely to crack or deform during processing.
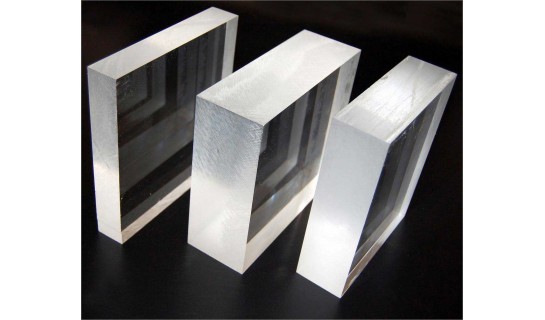
Machines used for CNC acrylic machining
There are different kinds of CNC machines to cut or engrave acrylic in the market based on the complexity and shape of the products as well as the precision level of the product. Here we introduce the three main CNC machines for machining acrylic and explain how they work:
CNC router
A CNC router is a computer-controlled machine to carves out complex shapes from soft materials like wood, plastic, and expanded foam. It is the most common machine used for CNC acrylic because it can cut acrylic fast and offer fast reproduction. it is widely used for creating Acrylic signs and stands. However, CNC routers only work for low-precision acrylic machining due to their stationary workpiece design.
CNC milling center
A CNC milling center works with a round rotating tool that cuts into a block of material. Simliar technology like CNC router but It can be used to create high-precision acrylic products such as optic parts. Not like CNC routers only work for soft materials, and CNC Milling machines also work for hard and strong materials such as steel, and aluminum.
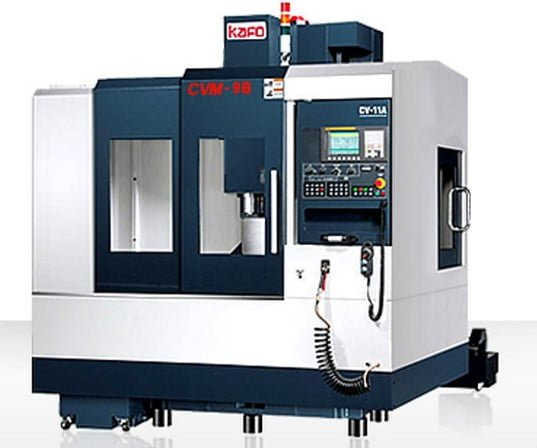
CNC lathe
A CNC lathe uses a rotating acrylic workpiece and a fixed tool to make precise cuts. When machining acrylic, the machine moves the tool in a straight line across the surface of the acrylic, working around the edges and removing material until the part reaches the desired shape.
CNC laser cutting machine
Computer Numeric Controlled (CNC) Laser cutting machines use a focused high-power laser beam to cut the block of material and get the desired shapes of the product. They are specially used to cut acrylic products with high precision details with a very clean cut. However, it only works for thin acrylic blocks, usually less than 20mm, and is commonly used for making markings on acrylic products.
How To CNC Machining Acrylic?
CNC machining acrylic is a precise and efficient way to create high-quality parts with smooth finishes. To achieve the best results, it’s important to follow a clear and organized process. Here’s a step-by-step guide to help you machine acrylic effectively:
Step 1: Design the Product in CAD
First, create the design of your acrylic product using CAD software. Keep in mind the limitations of CNC machining, like the size of the cutter, to make sure the design is possible to machine.
Step 2: Prepare the Acrylic Block
Next, prepare a block of acrylic that is larger than your final product. The block should be about 100mm bigger than the desired size, so the CNC machine can remove extra material during the machining process.
Step 3: Secure the Acrylic Block
Fix the acrylic block onto the machine table using clamps or glue. This keeps it in place and prevents any movement that could affect the accuracy of the machining.
Step 4: Set Up the CNC Machine and Tool
Choose the right cutting bits for the job. Set the CNC machine with the proper settings, like spindle speed, feed rate, and cutting depth, based on the type of acrylic you’re machining.
Step 5: Program the CNC Machine
Convert the CAD design into G-code, which tells the CNC machine how to move the cutting tool to shape the acrylic. This code controls the path and actions of the CNC machine.
Step 6: Machine the Acrylic Block
Start the CNC machine and let it follow the programmed path. The machine will cut the acrylic block into the final shape and size according to the design.
Step 7: Surface finishing
Once machining is complete, perform finishing processes to smooth the surface and polish the acrylic for a clean, professional look.
What is the best CNC bit for acrylic?
Based on our experience, a 1/4-inch solid carbide O-Flute End Mill Bits is the best for CNC machining Acrylic. this is because they are specifically designed for acrylic cutting and drilling. it can effectively pull out the chips as the cutting occurs and prevent plastic chips from building up inside the curve of the cut.
What are the best CNC settings for acrylic?
Up on the requirement and complexity of the acrylic product, different settings may be needed for each case. but here we summarize the general settings for machining acrylic as below, you can take it as a reference to make your acrylic part.
- Feed Rate: Generally between 75-300 IPM.
- RPM: Use at least 18,000 RPM
- Cutting depth: Set as 1/2 of the diameter of the bit
- Ramping: set a ramp around 1-3 inches for each tool path
Surface Finishes For CNC Machined Acrylic
After CNC machining, acrylic parts can go through different finishing techniques to improve their appearance, durability, or function. Here we introduce some popular finishing methods for CNC machined acrylic and you will learn how they work.
Sanding: Sanding helps smooth out small imperfections and prepare the acrylic surface for further finishing. It’s often the first step in finishing and can be used to create a specific texture or smooth surface.
Buffing and Polishing: This process uses soft cloths and abrasive compounds to smooth the surface of acrylic, making it shiny and clear. however, it requires more labor resources to finish the job. It’s perfect for applications where clarity and smoothness are important, like lenses or high-end decorative pieces.
Flame Polishing: This method uses a flame to gently melt the edges of acrylic parts, giving them a smooth, glossy finish. Compare with other polishing techniques, Flame polishing can be done very quickly and usually works for the edges of acrylic parts.
Vapor Polishing: In this method, a chemical vapor is used to slightly melt the surface of the acrylic, giving it a glass-like finish. Vapor polishing is great for improving clarity, especially for parts with complex shapes that are hard to polish by hand.
Chemical Polishing: This technique involves dipping the acrylic part in a chemical solution that smooths out imperfections. It enhances the natural clarity of the acrylic without using physical abrasion, making it a good choice for delicate parts.
Bead Blasting: Bead blasting uses fine beads to gently roughen the surface of acrylic, giving it a consistent matte finish. This method is useful for hiding fingerprints or light scratches without damaging the material.
Painting and Coating: Painting or coating acrylic gives it color and additional properties, such as better UV resistance or increased hardness. Acrylic holds paint and coatings well, offering plenty of options for customization in color and finish.
Dyeing: Dyeing acrylic allows you to add vibrant colors to the material. This process involves soaking the acrylic in a dye solution, allowing the color to penetrate the surface. Dyeing is ideal for creating custom-colored acrylic parts and is often used for decorative items, signage, or products where color is important.
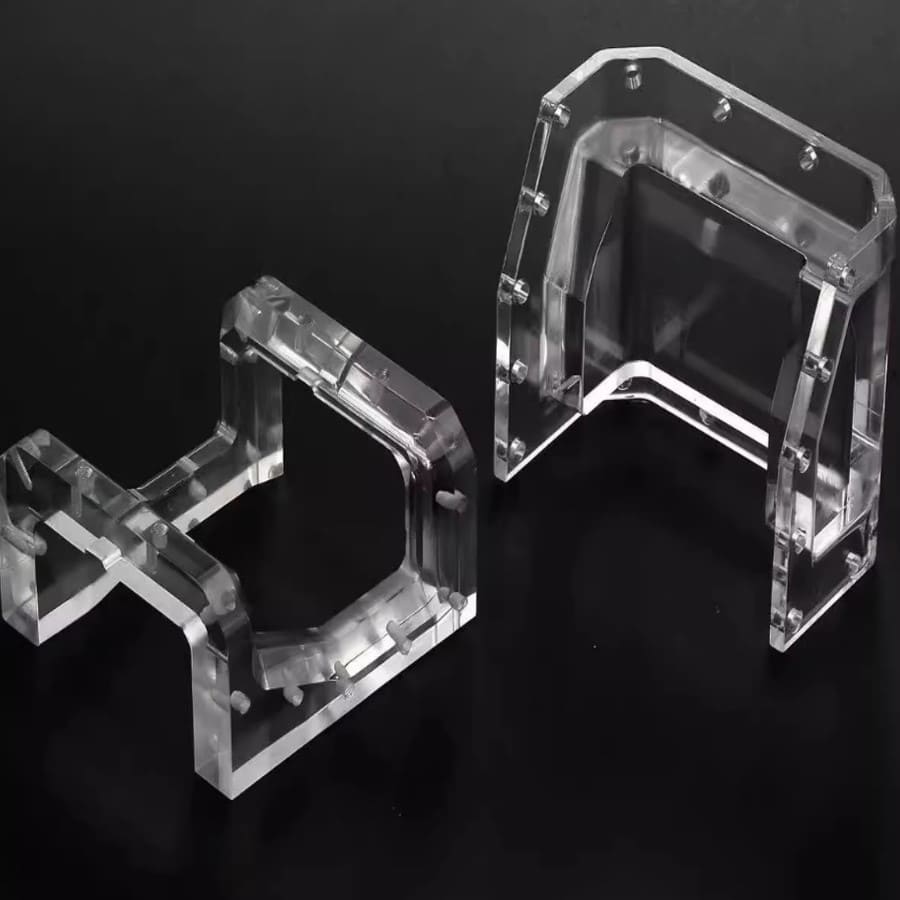
Applications Of CNC Acrylic Parts
CNC acrylic parts have many uses across various industries such as lighting, Automotive, construction, and medical. This is becasue of the benefits of Acrylic parts bring to these applications. Let’s explore some of the common uses of CNC-machined acrylic parts in these industries:
Lighting
Acrylic’s transparency makes it a top choice in the lighting industry. Its high light transmission and optical clarity make it perfect for products like lamps, light tubes, and light-emitting components.
Automotive
Acrylic is commonly used in the automotive sector for car windows, panels, fenders, and motorcycle windshields. Its ease of fabrication and surface hardness also make it suitable for producing covers for car lights, indicator lights, and other components.
Construction
Acrylic’s high impact and UV resistance make it ideal for construction projects. It’s used in building doors, canopies, panels, window profiles, and façade designs, offering durability and aesthetic appeal.
Medical
Acrylic is widely used in the medical field for making cabinets, incubators, glove boxes, and other medical devices. Its ease of cleaning and maintenance make it a popular choice. Additionally, acrylic’s compatibility with biologics makes it a preferred material for dental fillings and other medical applications.
CNC Acrylic Parts with KUSLA
CNC machines use advanced technology to create precise and accurate components from acrylic, but the process requires careful attention. At KUSLA prototype, we specialize in sculpting and cutting acrylic using the latest CNC machining technology. Partner with our Acrylic CNC machining service, We can help you choose the best type of acrylic for your project and recommend the right machining techniques to ensure your parts have excellent durability, consistency, and clarity. Contact us today to learn more.
FAQs
How to secure acrylic on CNC?
Besides the clamp, using some strips of double-sided tape on the back side could help secure the acrylic on CNC.
Is Acrylic Better Than Glass?
Acrylic sheets offer several benefits compared to glass and other plastics. They are much lighter, yet their surface hardness is significantly higher. Acrylic is also shatter-resistant and has excellent UV stability, making it more durable and long-lasting.