Aluminum alloys are widely used in industries such as automotive, construction, and aerospace due to their strength, lightweight nature, and resistance to corrosion. There are many types of aluminum alloys designed for different applications. Among them, two of the most common are 6061 and 7075 aluminum. Engineers often need to choose between these alloys for various applications, making it essential to understand their differences in strength, composition, cost, and other key properties. This article compares these two alloys, focusing on their attributes to help you make the best choice for your needs.
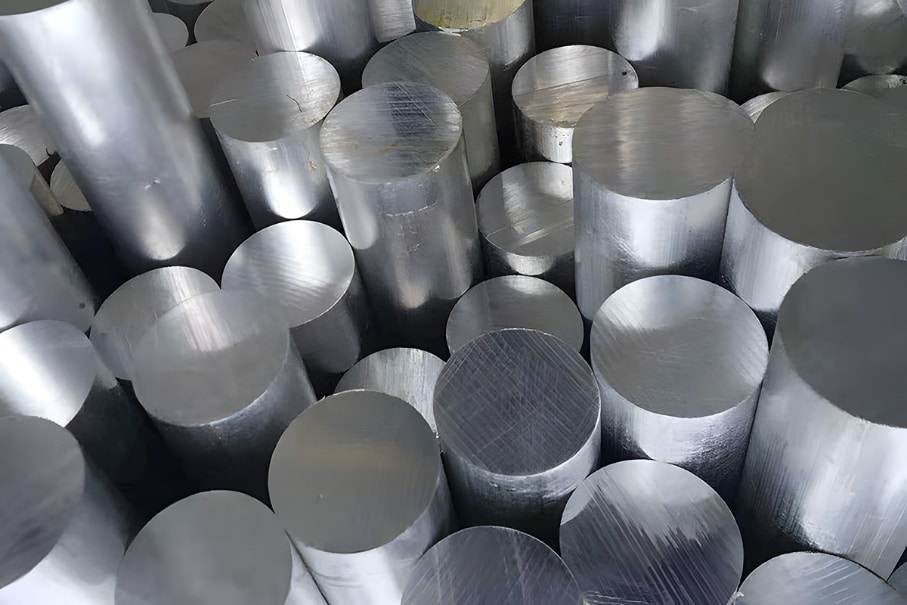
What Is 6061 Aluminum Grade?
Aluminum grade 6061 is one of the most commonly used aluminum alloys. it is Composed primarily of aluminum(97.9%) and magnesium, silicon, copper, chromium, and a tiny amount of other elements. it is the most famous member of the 6000 series of aluminum alloys. Due to the perfect balance of hardness and machinability, 6061 aluminum alloy is referred to as structural aluminum.
Key benefits of 6061 Aluminum
Compared to other aluminum alloys, 6061 aluminum is known for several key properties as below:
- Good Corrosion Resistance
- Good Weldability
- Medium Strength
- Machinability
- Cost-Effective
What Is 7075 Aluminum Grade?
Aluminum 7075 is a high-strength aluminum alloy used for highly stressed structural parts. As a primarily zinc-based aluminum alloy, It contains 5.6% zinc, 2.1% magnesium, and 1.2% copper. it is a member of the 7000 series aluminum alloys. Its increased mechanical strength makes it popular in the defense and aerospace industries.
Key benefits of 7075 Aluminum
Compared to other aluminum alloys, 7075 aluminum is known for several key properties as below,
- High Strength
- Superior Fatigue Resistance
- Good Stress Corrosion Cracking Resistance
- Toughness
- Impact Resistance
Next, we will make a full comparison between 6061 and 7075 aluminum in terms of chemical composition, mechanical properties, fabrication capability, and applications. Let’s dive in!
6061 aluminum vs 7075 Aluminum: Chemical Composition
Below is a table to show the Chemical Composition of both materials and you will find how each Chemical affects the performance of the materials.
Element | Property Affected | Aluminum 6061 Composition (%) | Aluminum 7075 Composition (%) |
Aluminum (Al) | Strength, Hardness | Approximately 97.9 | Balance (Over 90%) |
Silicon (Si) | Machinability | 0.4 – 0.8 | 0.4 |
Magnesium (Mg) | Strength, Corrosion Resistance | 0.8 – 1.2 | 2.1 – 2.9 |
Zinc (Zn) | Strength | 0.25 | 5.1 – 6.1 |
Copper (Cu) | Corrosion Resistance., Strength | 0.15 – 0.4 | 1.2 – 2.0 |
Iron (Fe) | Strength | 0.7 | 0.5 |
Manganese (Mn) | Strength, Machinability | 0.15 | 0.3 |
Chromium (Cr) | Corrosion Resistance | 0.04 – 0.35 | 0.18 – 0.28 |
Titanium (Ti) | 0.15 | 0.2 |
6061 aluminum vs 7075 Aluminum: mechanical Properties
Mechanical properties have a significant impact on the functionality of final aluminum parts. Let’s go through them one by one, comparing 6061 aluminum to 7075 aluminum.
Tensile Strength
Tensile strength measures a material’s resistance to a longitudinal pulling force. Aluminum 7075 has nearly twice the tensile strength of 6061 aluminum, which is why it is commonly used in applications where high strength is critical, such as aerospace components.
Yield Strength
Yield strength indicates the point at which a material begins to deform plastically. Aluminum 7075 has a much higher yield strength than 6061, so it has a good ability to withstand deformation.
Hardness
Hardness refers to a material’s resistance to surface indentation, scratching, or abrasion. Aluminum 7075 has a higher hardness compared to aluminum 6061, so it is more resistant to wear, damage, and surface deformation under stress than aluminum 6061. This property is important for aerospace components due to harsh conditions over time.
Elongation
Elongation measures how far a material can stretch before breaking. Aluminum 6061 is more ductile in this regard, meaning it can undergo significant deformation before reaching its breaking point, unlike 7075, which is less ductile and more prone to fracture under similar conditions.
Young’s Modulus(Modulus of Elasticity)
Young’s Modulus defines a material’s stiffness and its ability to return to its original shape after deformation. Both alloys have similar values for Young’s Modulus, but 6061 is slightly more elastic, which makes it more commonly used in structural components and frameworks.
Thermal Conductivity
Thermal conductivity refers to how efficiently a material conducts heat. Aluminum 6061 has higher thermal conductivity than 7075, so it is widely used for heat sinks and cooling systems, where efficient heat transfer is needed.
Elasticity
Elasticity reflects a material’s ability to deform and return to its original shape under applied stress. Aluminum 6061 has higher elasticity compared to 7075, this means it can be flex more easily without permanent deformation.
Temperature Resistance
Temperature resistance indicates how well a material can withstand elevated temperatures. Aluminum 7075 performs better in high-temperature environments due to its higher melting point and better thermal stability when compared to aluminum 6061.
Corrosion Resistance
Corrosion resistance refers to a material’s ability to withstand deterioration when exposed to corrosive substances. Both alloys exhibit good corrosion resistance, but aluminum 6061 is superior, particularly in harsh environments such as marine and coastal applications.
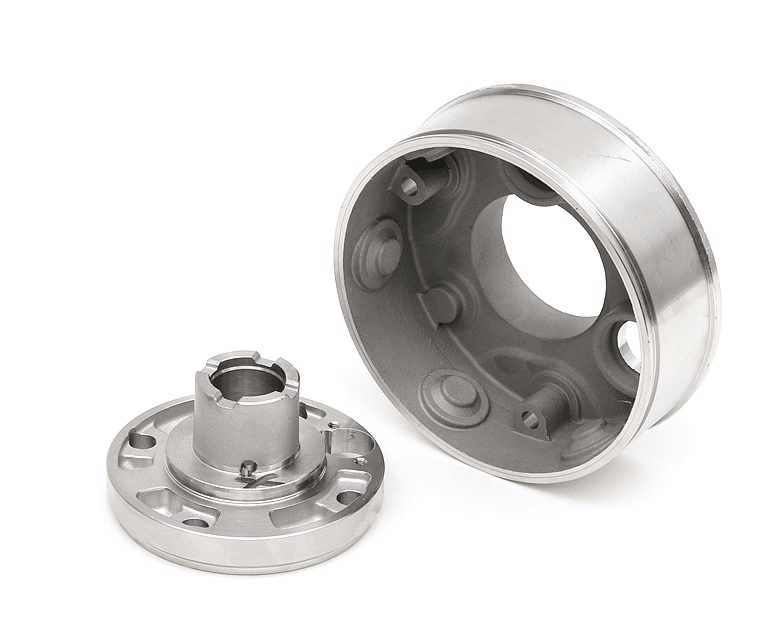
6061 Aluminum vs 7075 Aluminum: Fabrication capability
Fabrication capability is a key property when deciding which processes can be used to work with a material. Here, we compare the fabrication capabilities of 6061 and 7075 aluminum to help you choose the right processes for manufacturing your aluminum parts.
CNC Machinability
Aluminum 6061 is easy to machine and tends to produce longer, continuous chips during CNC machining. In contrast, aluminum 7075 generates shorter, segmented chips. This means 6061 aluminum is easier to machine than aluminum 7075 and results in more manageable chip formation.
Anodizing Suitability
Anodizing is a popular finish for aluminum parts. According to the Aluminum Anodizers Council, only the 5xxx and 6xxx series are suitable for anodizing. 6061 aluminum provides better anodizing results than 7075, which is why 6061 is commonly used in industries like construction and automotive. Its flexibility also allows for a wider range of anodizing applications.
Weldability
In terms of weldability, Aluminum 6061 is better. It is adaptable to various welding techniques, including TIG and MIG welding with a good result. Although Aluminum 7075 is weldable, it demands more expertise and careful control of welding parameters.
Bending
For bending operations, Aluminum 6061 is highly formable and can be bent to various angles without the risk of cracking or distortion. In contrast, Aluminum 7075 is less ductile and more prone to cracking during bending, especially at sharp angles or under high stress.
Sawing
Both alloys can be cut effectively, but Aluminum 6061 is easier to saw. Standard sawing equipment can easily cut 6061, ensuring precise and clean cuts. In contrast, Aluminum 7075 requires specialized sawing equipment and more careful handling to achieve optimal cutting results due to its higher hardness.
EDM (Electrical Discharge Machining)
Wire EDM is not commonly used for Aluminum 6061 due to its excellent machinability with conventional methods like milling and turning. However, for Aluminum 7075, EDM becomes a more viable option, especially when producing high-precision components or intricate features that are difficult to achieve with traditional machining methods. EDM offers a high level of accuracy and is useful for hard-to-machine alloys like 7075.
Tool Wear
Tool wear is a key consideration during machining, as it directly impacts both the quality of the workpiece and the longevity of the tools. Aluminum 6061 exhibits low tool wear, making it more cost-effective in terms of tool maintenance. In contrast, Aluminum 7075, causes higher tool wear due to its increased hardness. This means that machining 7075 requires more frequent tool replacements or sharpening, leading to higher costs and more careful attention to machining parameters.
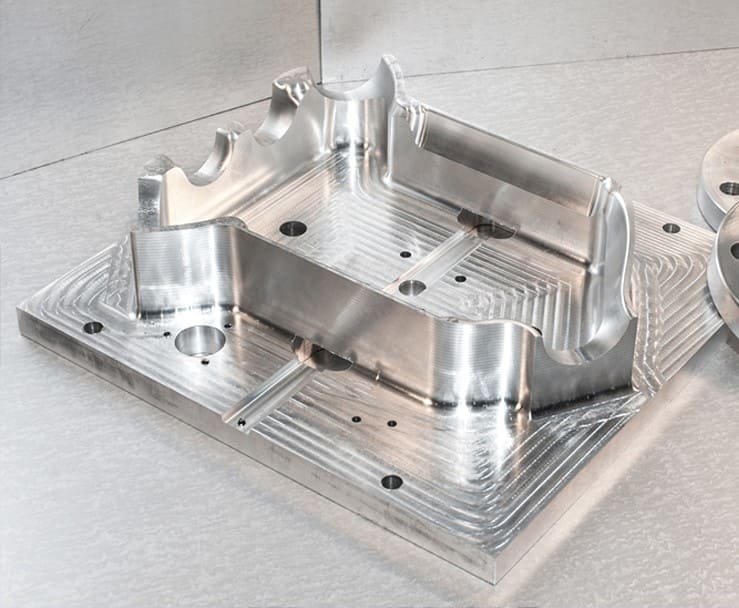
6061 aluminum vs 7075 Aluminum: Applications
Both 6061 and 7075 aluminum alloys are widely used in industries like aerospace, automotive, and construction, but they differ in specific applications based on their properties. 6061 is favored for applications requiring formability, ductility, and ease of welding, such as tanks and rounded structures. While 7075 is ideal for high-strength applications, especially where durability and precision are essential, like aerospace and industrial tooling. here we list some parts made by these two materials:
6061 Aluminum Applications:
- Automotive parts (frames, wheels)
- Building materials (structural components)
- Electrical parts (connectors, housings)
- Bicycle components (frames, handlebars)
- Piping (due to corrosion resistance and weldability)
7075 Aluminum Applications:
- Aerospace (wings, fuselages)
- Missile parts
- Gears and shafts (high-stress machinery)
- Regulating valves (high-performance systems)
- Fuse parts (wear resistance)
Conclusion
Both 6061 and 7075 aluminum alloys have distinct advantages, and by carefully evaluating your project’s requirements, you can make an informed decision that ensures optimal results. However, contacting a professional supplier can quickly help you determine the best alloy for your specific application. KUSLA is a leading manufacturer providing precision aluminum machining services in China. Feel free to reach out to us for expert guidance and assistance with your aluminum machining projects.
FAQ
What is the price difference between 6061 and 7075 aluminum?
Generally, 7075 aluminum is about 20% to 25% more expensive than 6061 aluminum, although the price difference can vary depending on the local market and current conditions. Due to the increased strength and specialized manufacturing requirements of 7075, it typically commands a higher price.
What grade in 6061 aluminum is used for machining?
The most commonly used grade of 6061 aluminum for CNC machining is 6061-T6, which offers a good balance of strength, machinability, and corrosion resistance, making it ideal for a wide range of machining applications.
Is 7075 aluminum stronger than steel?
The anwser is it depends. 7075 aluminum is one of the strongest aluminum alloys and can be comparable to certain grades of steel. For example, its ultimate tensile strength of 503 MPa is higher than that of structural steel, which typically has a tensile strength of around 420 MPa. However, some high-strength steel grades can exceed 1000 MPa in tensile strength, making them stronger than 7075 aluminum.
Is 6061 or 7075 aluminum stronger?
7075 aluminum is stronger than 6061 aluminum. 6061 has a yield strength of 276 MPa, while 7075 boasts a much higher yield strength of 572 MPa.
Which aluminum is better in anodizing response, 6061 Or 7075?
6061 aluminum (from the 6xxx series) responds much better to anodizing compared to 7075 aluminum. It is a high-strength, easily machinable alloy, and when it comes to anodizing in various colors (especially for hard anodizing), 6061 is the preferred choice for many shops.