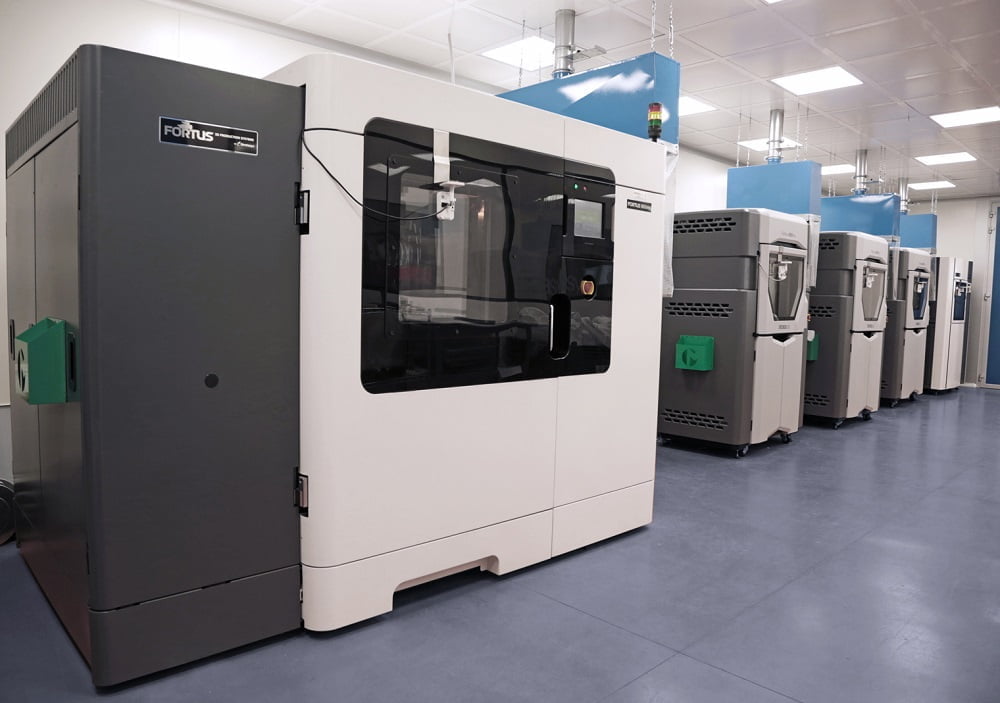
Online 3D Printing Services
Fast 3D printing for prototypes and production, ready in as little as 1 day. Get a quick quote with design feedback today.
15+ YEARS OF EXPERIENCE
MULTIPLE 3D PRINTING CAPABILITIES
One-stop Machining and Finishing
Rapid Prototyping Services & Rapid Manufacturing
Fast 3D printing for prototypes and production, ready in as little as 1 day. Get a quick quote with design feedback today.
15+ YEARS OF EXPERIENCE
MULTIPLE 3D PRINTING CAPABILITIES
One-stop Machining and Finishing
Our online 3D printing service lets you print custom parts whenever you need them. We use different 3D printing methods to turn your designs into plastic, metal, or rubber-like parts. With over 100 printers, we can quickly deliver parts in just a few days. We also offer a wide range of materials and finishing options to improve looks or strength.
Stereolithography (SLA) uses an ultraviolet laser to draw on liquid resin, building parts layer by layer until they are complete.
FDM uses a heated nozzle to melt thermoplastic filament, depositing it layer by layer to create the final part.
Selective Laser Sintering (SLS) uses a CO2 laser to fuse nylon-based powder, building parts layer by layer.
Direct Metal Laser Sintering (DMLS) uses a fiber laser to draw on a layer of metal powder, welding it together layer by layer.
A variety of 3D Printing metal and plastic part options are available for an instant online quote.
3D printing is an additive manufacturing process that builds objects from 3D model data (CAD) by joining materials layer by layer. Each layer fuses with the one below it to create the final shape. 3D printing can use materials like plastics, photopolymers, metals, composites, glass, and more.
3D printing can produce prototypes in hours or days, instead of weeks or months with other methods.
3D printing allows for the design and print of more complex designs than traditional manufacturing processes
3D printer is cheap, So as a single step manufacturing process, 3D printing saves time and costs of the parts
Most frequent questions and answers
3D printed prototype with minimal post-processing and assembly can cost range from $10 to $1000, depending on the size and complexity of the design.
Yes, with a desktop 3D printer, you can make the simple prototype at home according to the instructions.
yes, if you have a kind of 2D to 3D printer at home, but only simple pictures.
No, 3D printing is a cheap solution compare with other process when making prototypes.
Get in touch with our professional team today, and we will respond to you within 48 hours.
Get in touch with our professional team today, and we will respond to you within 24 hours.
Marketing Director
Project Manager
Project Manager
Technical Sales
Technical Sales
Technical Sales
Get in touch with our professional team today, and we will respond to you within 24 hours.
Marketing Director
Project Manager
Project Manager
Technical Sales
Technical Sales
Technical Sales